锥头与锥套检测的重要性及核心项目解析
锥头与锥套作为机械传动系统和结构连接中的关键部件,广泛应用于建筑工程、轨道交通、航空航天等领域。其质量直接关系到设备运行的稳定性、安全性和耐久性。由于锥头与锥套通过锥面配合实现动力传递或紧固连接,其几何精度、材料性能及表面质量的微小偏差都可能导致配合失效,进而引发重大安全事故。因此,建立科学完善的检测体系,对锥头与锥套的关键参数进行全面验证,是确保产品性能达标的核心环节。
核心检测项目分类与实施方法
1. 几何尺寸检测
使用三坐标测量仪、激光扫描仪等高精度设备,对锥头的锥角、大端直径、小端直径进行三维建模分析,要求锥度偏差不超过±0.05°。锥套需检测内锥孔的同轴度(≤0.02mm)和锥面圆度(≤0.01mm),确保配合面接触率≥85%。
2. 硬度与材料检测
通过洛氏硬度计(HRC)测试表面硬化层深度(0.8-1.2mm),结合光谱分析仪验证材料成分(如40CrMoV钢的Cr含量18-21%)。对热处理后的金相组织进行显微观察,确保无脱碳、过烧等缺陷。
3. 表面完整性检测
采用白光干涉仪检测表面粗糙度(Ra≤0.8μm),使用磁粉探伤或渗透检测排查裂纹缺陷(裂纹深度≤0.1mm)。对于防腐处理的锥套,需通过盐雾试验验证镀层耐腐蚀性(480小时无红锈)。
4. 配合性能试验
在液压试验机上模拟实际工况,检测锥头-锥套组件的轴向压入力(120-150kN)和抗拉强度(≥800MPa)。采用扭力传感器记录动态扭矩传递效率(≥95%),并监测配合面磨损量(≤0.05mm/万次循环)。
5. 无损检测技术应用
引入工业CT扫描技术对内部缺陷进行三维重构检测,分辨率达到5μm级。超声波测厚仪用于测量锥套壁厚均匀性(偏差≤0.1mm),相控阵检测系统可实时监控锥面接触应力分布。
检测标准体系与质量控制要点
检测过程需严格遵循GB/T 343-2019《锥面配合件通用技术条件》、ISO 12110-2:2013金属材料疲劳试验标准等规范。重点控制锥面自锁性能(滑移量≤0.02mm)、疲劳寿命(≥5×10⁶次循环)以及环境适应性(-40℃~150℃工况性能稳定)等关键指标。
通过建立全流程检测数据库,实现质量参数的数字化追溯。建议采用统计过程控制(SPC)方法,对关键工序的CPK值实施动态监控,确保制程能力指数≥1.33。对于高精度应用场景,应增加模拟工况下的动态载荷测试,验证产品在实际应力状态下的可靠性。
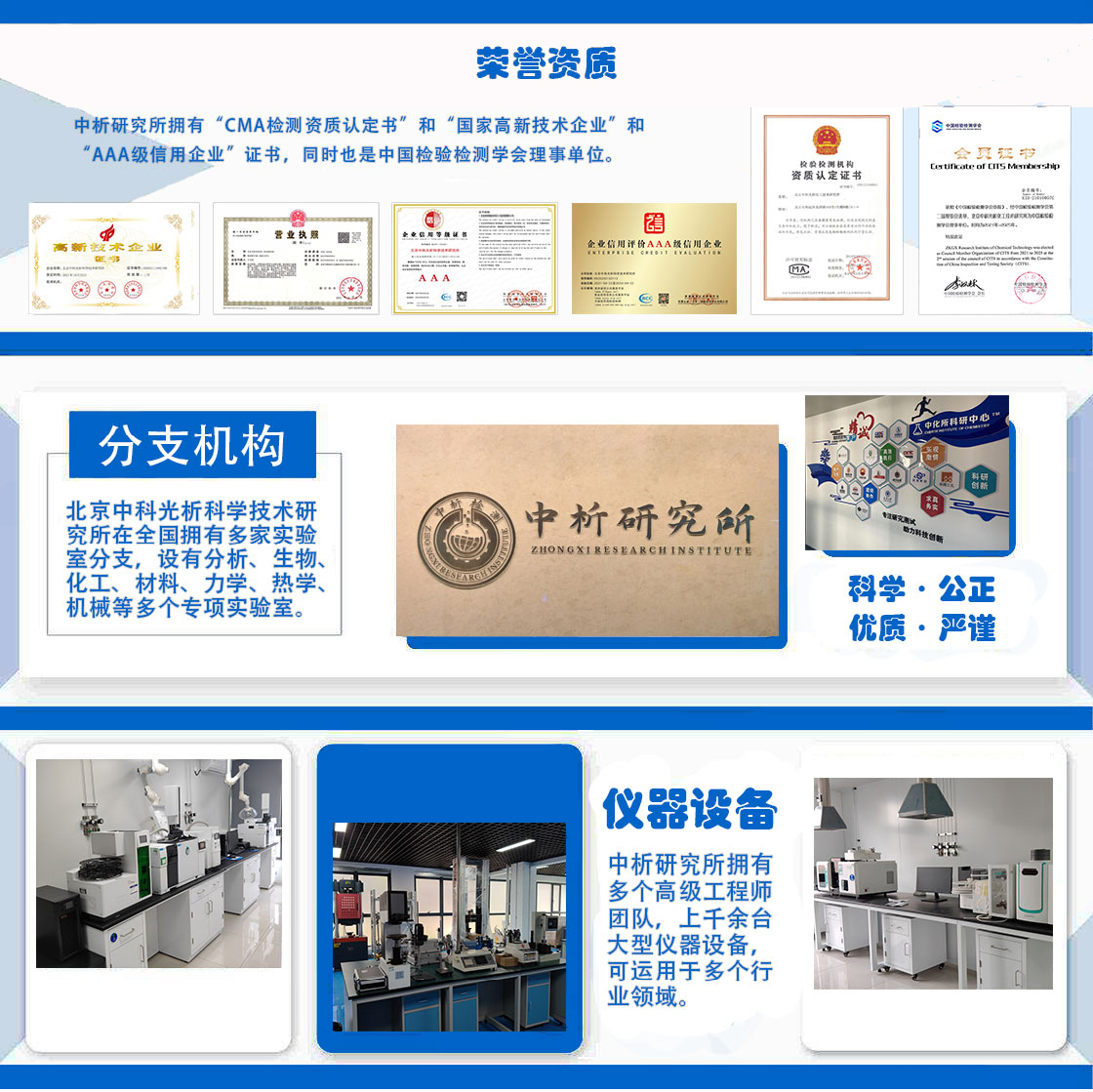
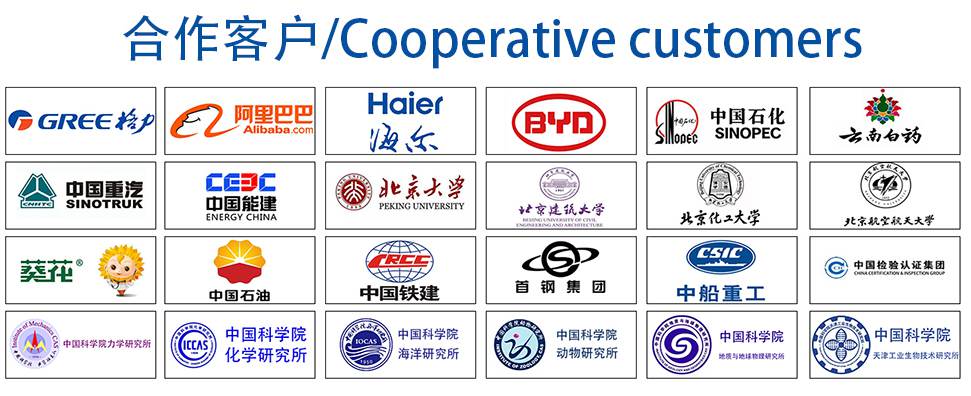