油气井套管及油管用钢管检测的重要性
在石油天然气勘探开发过程中,套管和油管作为井身结构的关键组成部分,承担着支撑井壁、密封油气层、传输介质等多重功能。由于长期承受高温高压、腐蚀性介质及复杂应力环境,其质量直接关系到油气井的安全性、使用寿命和生产效率。通过科学规范的钢管检测,能够有效发现材料缺陷、尺寸偏差和性能隐患,预防因管材失效导致的井喷、泄漏等重大事故,同时延长设备服役周期,保障油气田开发的稳定性和经济性。以下针对套管及油管用钢管的核心检测项目展开详细说明。
一、材料性能检测
材料性能是钢管质量的基础保障,主要检测项目包括:
1. 化学成分分析:采用光谱仪或化学滴定法验证碳、锰、铬、钼等元素含量是否符合API 5CT等标准要求;
2. 力学性能测试:通过拉伸试验测定屈服强度、抗拉强度和延伸率,利用冲击试验评估低温韧性,确保材料具备足够的抗变形和抗断裂能力;
3. 金相组织分析:观察微观晶粒结构,检测是否存在偏析、夹杂物等冶金缺陷。
二、几何尺寸与形位公差检测
精确的尺寸控制是保障管材密封性和连接性能的关键:
1. 使用激光测径仪或卡规测量外径、壁厚及椭圆度,确保符合公差范围;
2. 通过螺纹量规检测接箍螺纹的螺距、锥度及紧密距,验证螺纹加工精度;
3. 采用三维影像测量系统检查管体直线度及端面垂直度,避免安装过程中出现应力集中。
三、无损检测技术应用
针对钢管表面及内部缺陷的精准识别:
1. 超声波检测(UT):检测管壁内部裂纹、分层等体积型缺陷,精度可达毫米级;
2. 磁粉检测(MT):用于发现表面及近表面的磁性材料缺陷,如疲劳裂纹;
3. 涡流检测(ET):快速筛查管材表面微小裂纹和腐蚀坑,适用于大批量生产检测;
4. 射线检测(RT):通过X射线或γ射线成像技术定位焊接区域的气孔、未熔合等缺陷。
四、特殊工况性能验证
针对特定作业环境的附加检测需求:
1. 抗挤毁试验:模拟高压地层对套管的径向挤压力,测定临界失稳压力值;
2. 耐腐蚀试验:通过盐雾试验、HIC(氢致开裂)试验评估抗硫化氢腐蚀能力;
3. 高温高压密封性测试:在模拟井下环境中验证螺纹连接的气密封性能;
4. 疲劳寿命试验:通过循环载荷测试预测钢管在交变应力下的耐久性。
五、检测标准的执行与认证
所有检测项目均需严格遵循API 5CT、ISO 11960等国际标准,同时结合ASTM、GB/T等国家规范。第三方实验室认证(如 、DNV)可确保检测结果的权威性和度。通过建立完整的质量追溯体系,实现从原材料到成品管的全生命周期质量控制。
油气井管材检测技术的持续创新(如数字化检测、AI缺陷识别)正在推动行业向更高安全等级和智能化方向发展。只有通过系统化、多维度的检测手段,才能为深井、超深井及非常规油气开发提供可靠的材料保障。
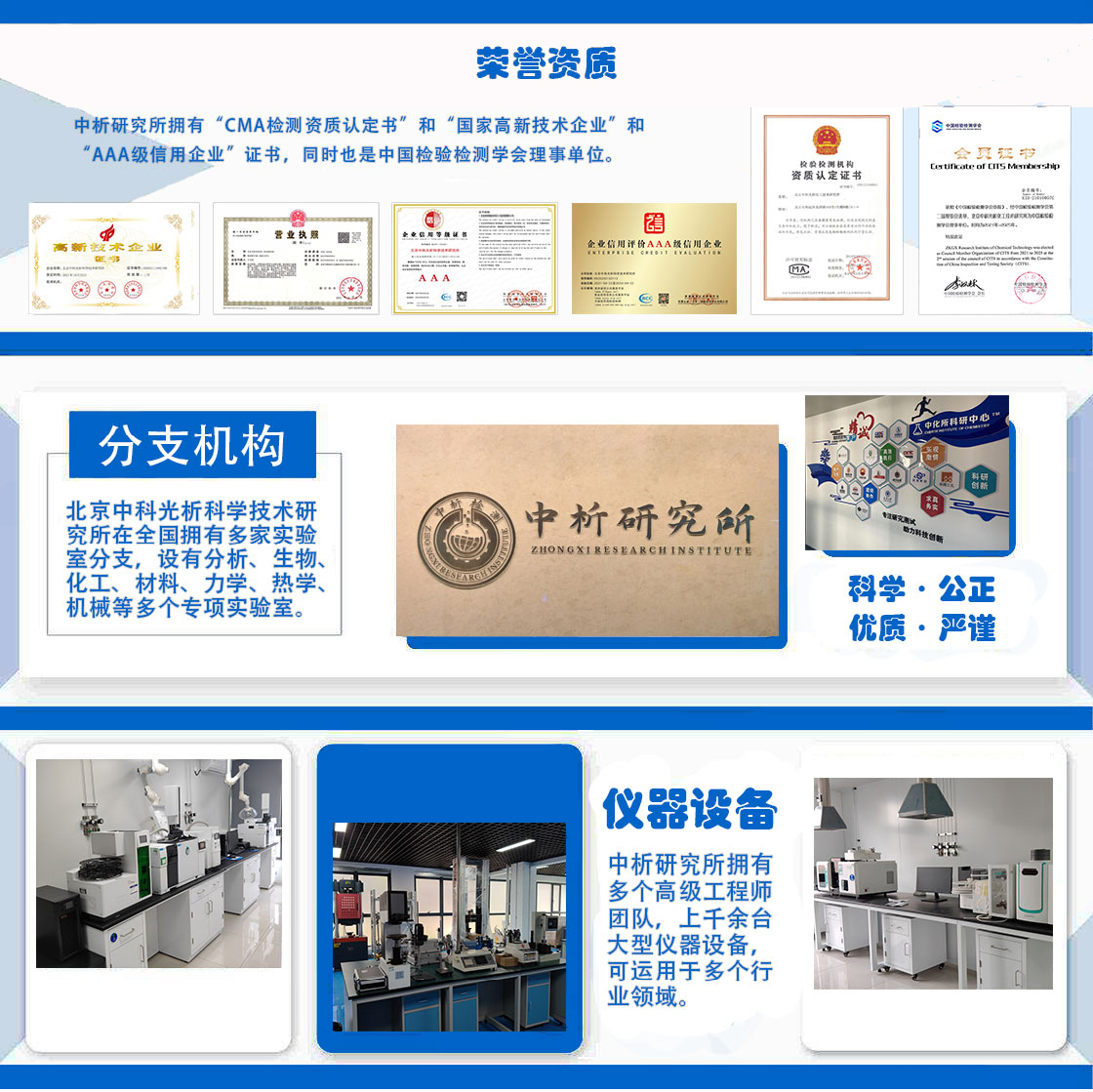
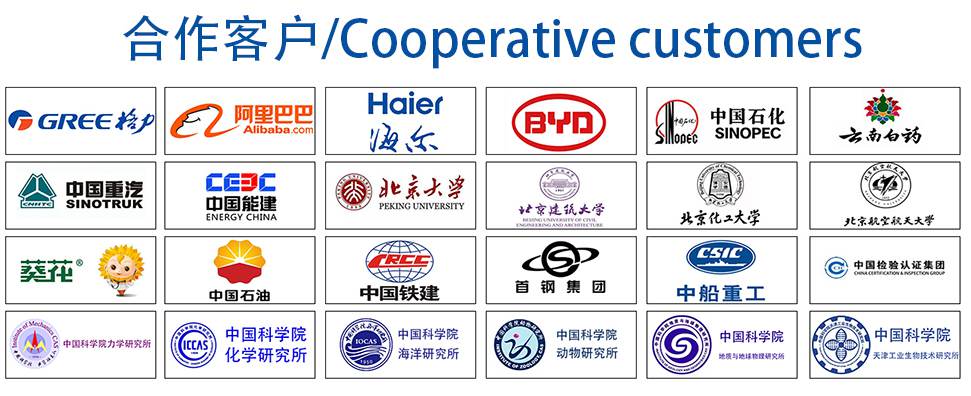