汽车、摩托车用燃油传感器检测的重要性
燃油传感器作为车辆燃油系统的核心部件之一,承担着实时监测油箱油量并将数据传递至仪表盘的重要任务。其性能直接影响驾驶者对剩余油量的判断,进而关系到车辆续航能力、燃油经济性及行车安全。然而,由于长期工作在复杂环境中(如高温、油液腐蚀、机械振动等),传感器易出现精度下降、信号失真甚至失效等问题。因此,定期对燃油传感器进行系统化检测,是保障车辆可靠运行和延长部件使用寿命的必要手段。
检测项目及技术要求
1. 电气性能测试
通过专用检测设备测量传感器的电阻值、输出电压或电流信号是否符合标称参数,验证信号线性度与油量变化的对应关系。需模拟不同液位状态,确保全量程范围内信号输出稳定,无跳变或断点现象。
2. 机械性能检测
包括浮子组件运动灵活性测试、传感器杆件耐压强度试验以及接触点磨损评估。使用高精度位移装置模拟浮子运动轨迹,验证机械部件在10万次往复运动后的功能保持率,确保无卡滞、变形等问题。
3. 环境适应性验证
在温湿度试验箱中模拟极端工况(-40℃至120℃、湿度95%RH),检测传感器密封性和材料稳定性。同时进行振动试验(频率5-2000Hz,加速度30g),评估内部元件抗机械冲击能力,防止因共振导致结构损坏。
4. 标定与精度校准
采用标准液位测量装置与传感器输出数据对比,计算示值误差和重复性偏差。要求全量程误差不超过±2%,关键节点(如1/4、1/2、3/4油量)误差控制在±1%以内,并生成标定曲线用于故障诊断。
5. 密封性及耐腐蚀检测
对传感器壳体进行0.3MPa气压测试,保压5分钟后泄漏量需小于0.1mL/min。在盐雾试验箱中连续喷雾96小时,检查金属部件锈蚀等级是否符合ISO 9227标准的NSS 5级要求。
6. 信号抗干扰能力评估
模拟车辆电磁环境(如点火系统、电机干扰),测试传感器信号在100MHz-1GHz频段的抗干扰性能。要求信号波动幅度不超过标称值的3%,确保在复杂工况下数据传输的可靠性。
检测流程的规范化管理
现代检测需依托智能化测试平台,集成数据采集、分析及报告生成功能。建议建立包含初期功能验证、中期性能测试、终检全项检验的三级检测体系,同时引入AI算法对历史检测数据进行趋势分析,提前预警潜在故障风险。
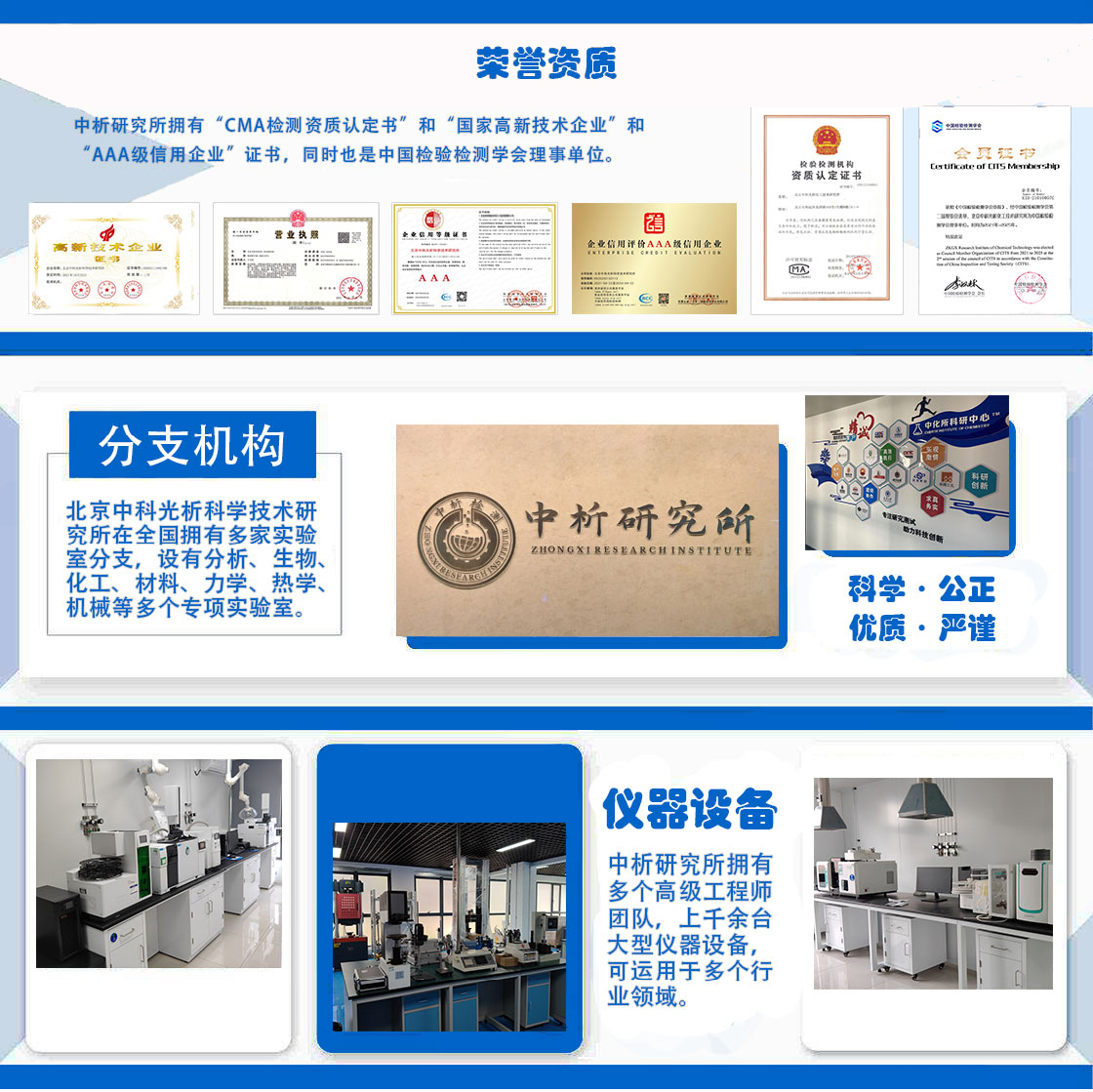
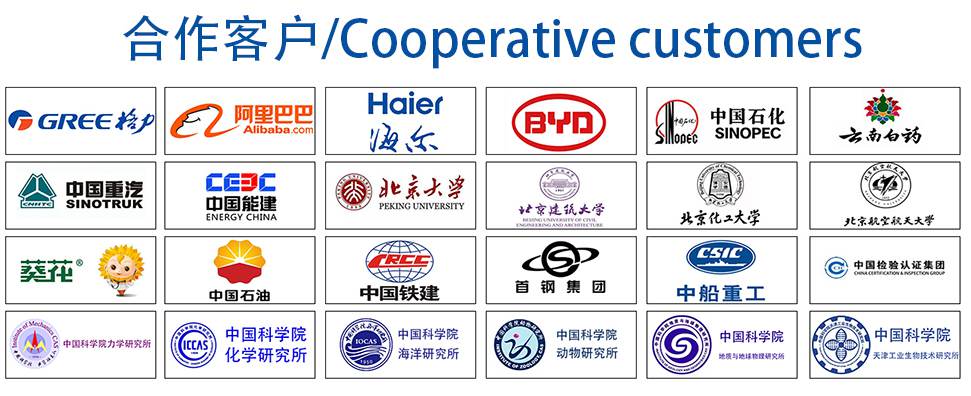