薄片检测的重要性与应用领域
薄片检测是一种针对超薄材料、半导体晶圆、光学薄膜及精密元件的关键质量控制手段。随着微电子、新能源、航空航天等行业的快速发展,薄片材料的厚度精度、表面完整性和物理性能直接影响产品的功能性及可靠性。在半导体制造中,晶圆厚度偏差可能导致芯片失效;在锂电池领域,隔膜厚度不均可能引发安全隐患。因此,通过高精度检测设备对薄片的几何参数、缺陷分布和材料特性进行系统性分析,已成为现代工业生产的核心环节。
核心检测项目与技术方法
厚度均匀性检测
采用激光共聚焦显微镜或光谱椭偏仪进行纳米级精度测量,通过多点扫描生成厚度分布云图,重点检测边缘减薄、局部隆起等异常。部分高端设备可同步监测表面粗糙度(Ra≤0.1μm)。
表面缺陷分析
基于机器视觉系统实现微米级缺陷识别,配置环形光源与高分辨率CCD相机(500万像素以上),可检测划痕(长度>10μm)、凹坑(深度>50nm)、异物污染(粒径>1μm)等32类缺陷,并结合AI算法实现缺陷自动分类。
材料组分检测
通过X射线荧光光谱(XRF)或能谱仪(EDS)进行元素分析,检测镀层材料成分及厚度(如Au镀层±5nm精度)。对半导体材料还需进行载流子浓度(1014-1019cm-3)和电阻率(0.001-100Ω·cm)测试。
力学性能测试
采用纳米压痕仪测量薄膜硬度(HV0.01-HV0.5)和弹性模量(50-500GPa),通过三点弯曲试验评估薄片抗弯强度(50-1000MPa)。针对柔性材料还需进行疲劳测试(>106次循环)。
前沿检测技术发展
太赫兹波谱技术可实现非接触式多层结构检测,扫描声学显微镜(SAM)能发现内部微裂纹(分辨率达5μm)。原子力显微镜(AFM)已实现原子级表面形貌重建,而同步辐射X射线可对纳米材料进行三维成像,推动检测精度进入埃米级时代。
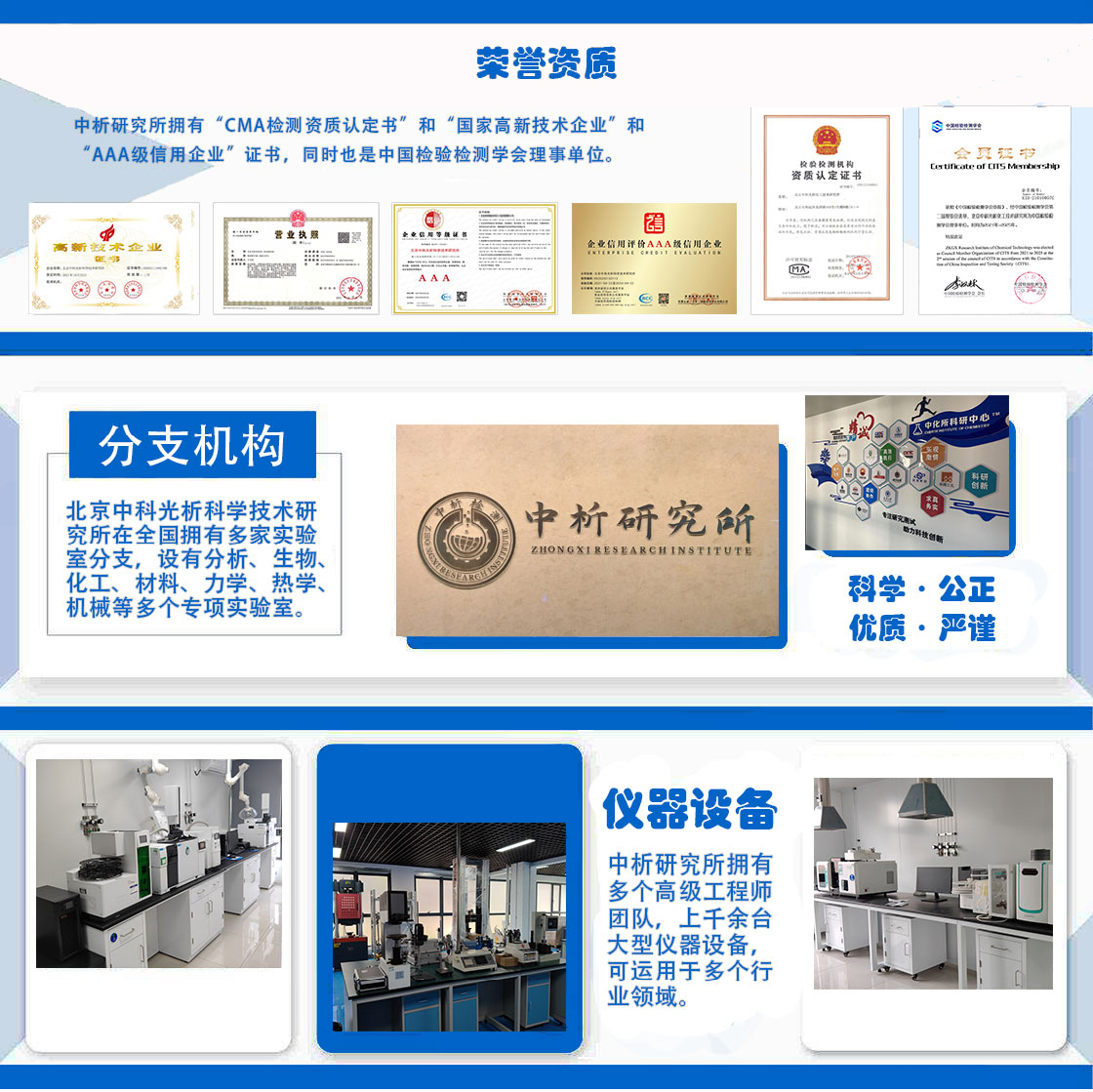
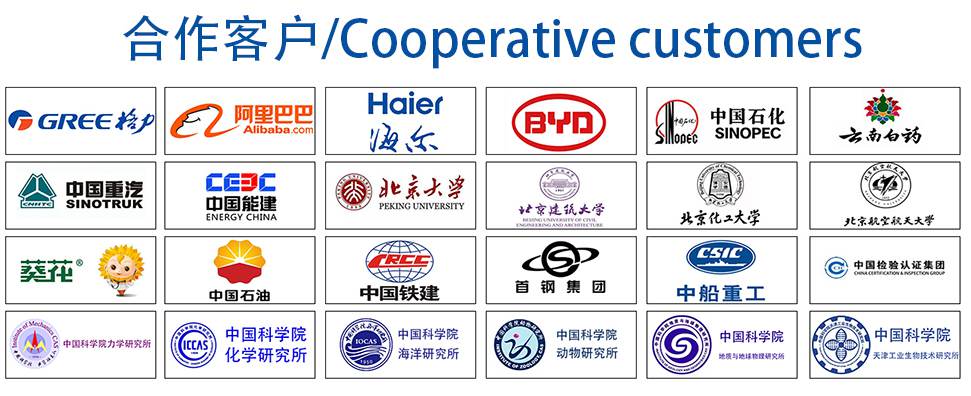