监测仪器质量检测的重要性与核心要素
在工业生产、环境监测、医疗诊断等领域,监测仪器作为数据采集的核心设备,其质量直接影响结果的准确性和可靠性。随着技术标准的提升和行业监管的加强,对监测仪器的质量检测已从简单的功能性验证发展为系统化、多维度的评估体系。通过科学规范的检测流程,可有效避免因仪器偏差导致的重大事故风险,同时为设备维护、生产优化提供数据支撑。
监测仪器质量检测的核心项目
1. 基本性能验证
包括量程范围测试、分辨率验证和零点漂移检测,通过标准参照物比对确认仪器的基础参数是否符合出厂指标。例如气体分析仪需测试最低检测限与量程上限的动态响应能力。
2. 准确性及重复性测试
采用标准物质或校准装置进行连续测量,计算示值误差和相对标准偏差(RSD)。典型场景如水质监测仪需通过不同浓度标准液的交替测试,确保线性误差≤±2%。
3. 环境适应性评估
模拟极端工况下的稳定性,包含温度循环试验(-20℃~50℃)、湿度测试(95%RH)、抗振动试验等。工业现场用仪器还需进行IP防护等级验证。
4. 数据接口与通讯测试
针对智能化设备的数字信号传输协议(如Modbus、4-20mA)进行兼容性验证,同时检测数据存储完整性和实时传输稳定性。
质量检测的技术标准体系
我国现行检测主要依据GB/T 15479《工业自动化仪表通用试验方法》、JJF 1001《通用计量术语及定义》等标准。环保类仪器需额外满足HJ/T 76《固定污染源烟气排放连续监测系统技术要求》等行业规范。
检测流程的关键环节
完整的检测流程包含五个阶段:设备预检→计量校准→性能测试→数据处理→证书签发。其中校准环节必须使用经 认证的标准设备,测试数据需满足至少3次重复试验的统计学要求。
常见质量问题与解决方案
约35%的故障源于传感器老化,表现为响应迟滞或基线漂移,需建立定期更换制度;22%的问题由电磁干扰引起,可通过屏蔽布线或加装滤波器解决。检测机构建议每季度开展预防性维护检测。
智能化检测技术的发展趋势
基于物联网的远程校准系统可将检测效率提升40%,AI算法实现异常数据自动诊断。2023年新发布的数字孪生检测技术,已能在虚拟环境中模拟90%以上的物理测试场景。
结语
建立全生命周期的质量检测体系,是保障监测仪器可靠运行的关键。未来随着检测技术的智能化和标准体系的完善,质量检测将逐步实现从被动维修向主动预防的转变。
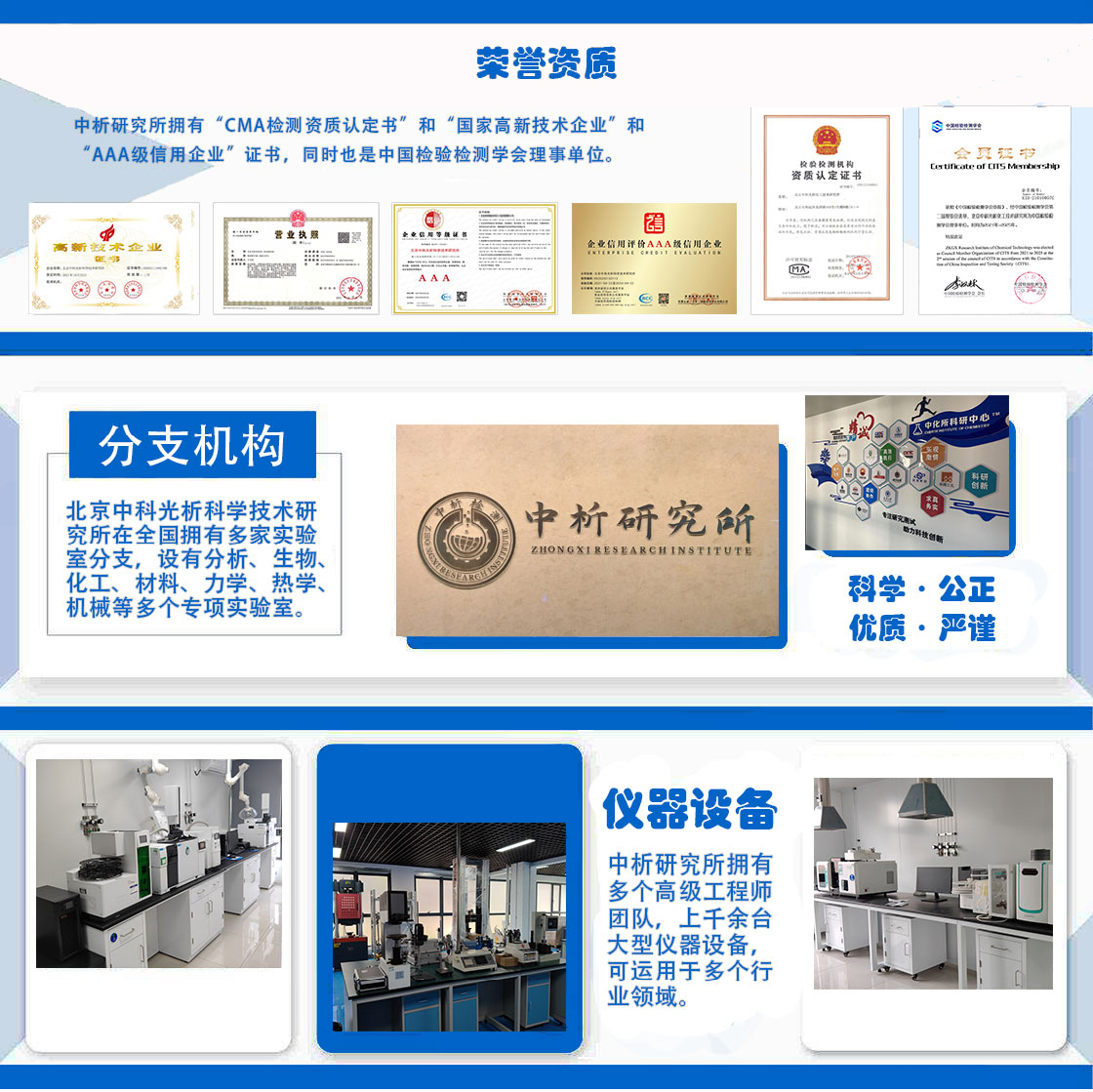
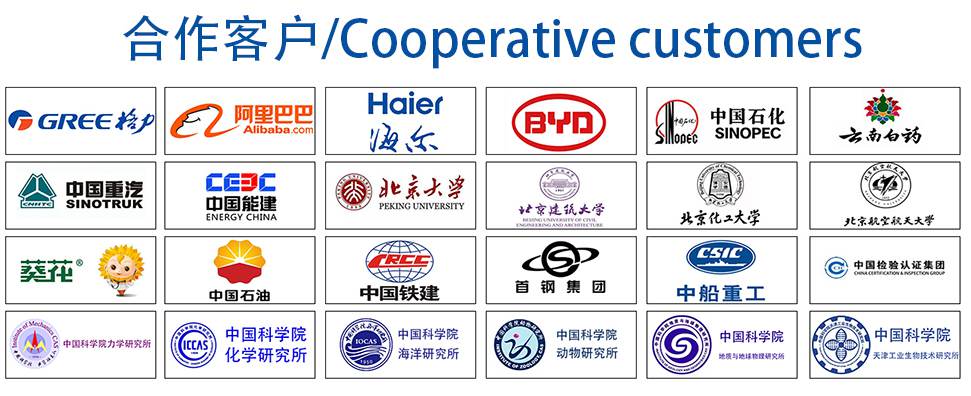