汽车用熔断器检测的重要性与核心内容
汽车用熔断器作为电路保护的核心元件,承担着避免电路过载或短路引发安全隐患的重要职责。随着汽车电气化、智能化程度的提高,车载电子设备的数量和功率需求显著增加,熔断器的性能与可靠性直接影响整车电气系统的稳定性和安全性。因此,对熔断器的检测不仅是生产环节的质量控制关键,更是保障车辆长期安全运行的必要手段。通过科学严苛的检测流程,可验证熔断器的分断能力、耐久性、温度适应性等核心指标,确保其在极端工况下的有效保护功能。
汽车熔断器检测的核心项目
1. 电气性能检测:包括额定电流测试、过载分断能力测试以及电压降检测。通过模拟不同电流负载(如1.13倍、1.45倍额定电流)下的熔断时间,验证是否符合QC/T 420等行业标准;分断能力测试需在短路条件下确认熔断器能否安全切断电路。
2. 机械性能检测:涵盖端子插拔力测试、振动耐久性测试和机械冲击试验。使用专业设备模拟车辆行驶中的振动环境(如频率10-2000Hz、加速度30g),检验熔断器结构稳定性,避免因机械应力导致接触不良或断裂。
3. 环境适应性检测:包含高温老化测试(-40℃至125℃循环)、湿热试验(温度85℃、湿度85%)、盐雾腐蚀测试等。验证熔断器外壳材料耐候性及内部结构的密封性能,确保在恶劣环境下仍能保持功能完整性。
特殊工况模拟检测
针对新能源汽车高压电路需求(如400V/800V平台),需增加高压电弧分断测试和绝缘电阻检测。通过直流高压发生器模拟电池系统短路工况,检测熔断器在高压大电流(可达1000A以上)下的分断速度与灭弧能力,同时测量绝缘电阻值(要求≥100MΩ)以防止漏电风险。
检测流程与方法创新
现代检测采用自动化测试平台,结合高速数据采集系统(采样率≥1MS/s)和红外热成像技术,实时记录熔断过程中的温度场分布与时间-电流特性曲线。行业正推进基于AI算法的预测性检测模型,通过熔断器材料微观结构分析预判其寿命周期,推动检测效率提升30%以上。
行业挑战与发展趋势
当前检测面临新能源车熔断器微型化(如芯片式熔断器)与高功率密度化的双重挑战。行业正在研发多物理场耦合检测技术,整合电磁-热-力耦合分析,并建立基于ISO 8820-8:2020的智能化检测标准体系,以满足未来汽车电气架构的更高安全需求。
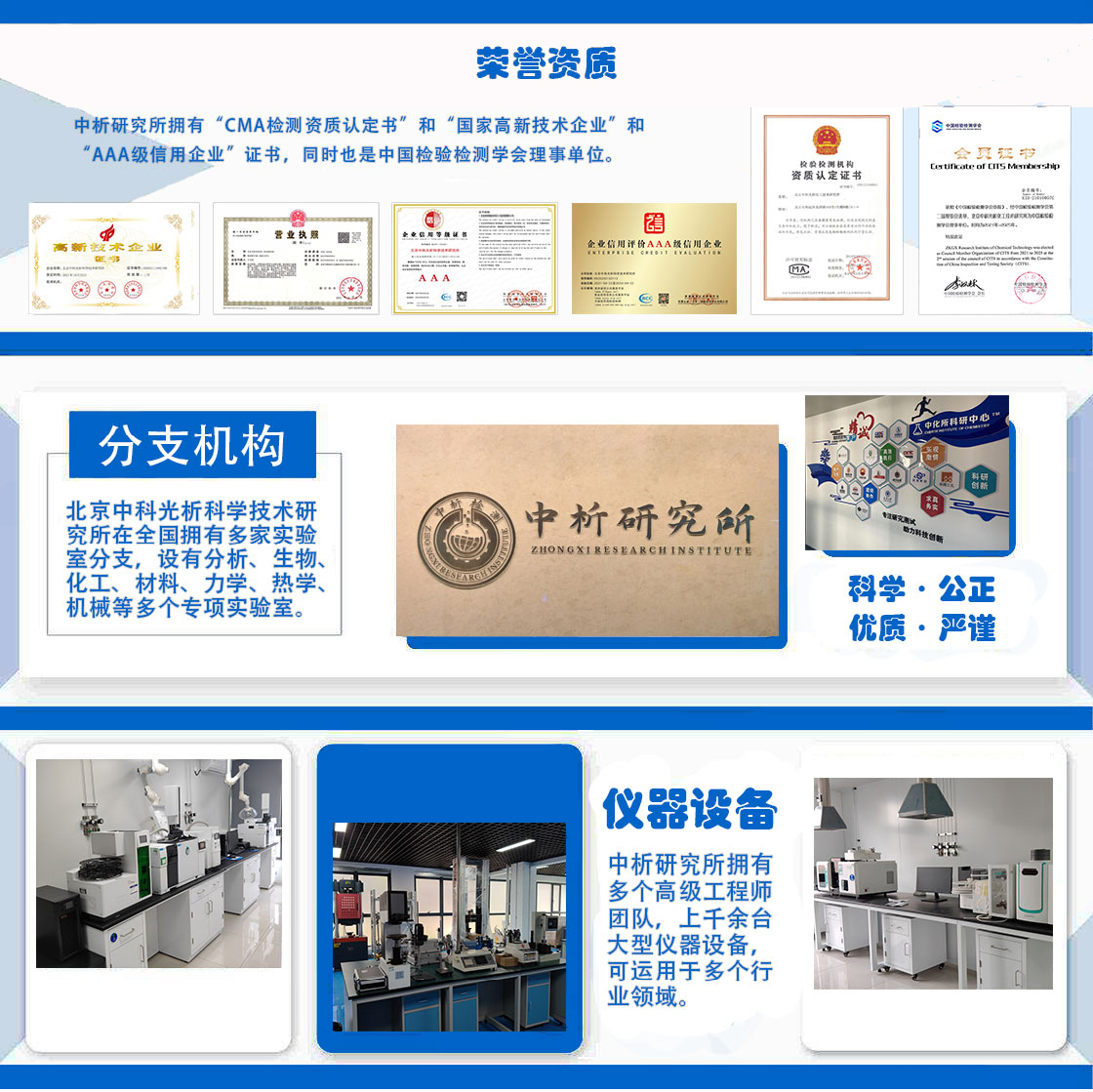
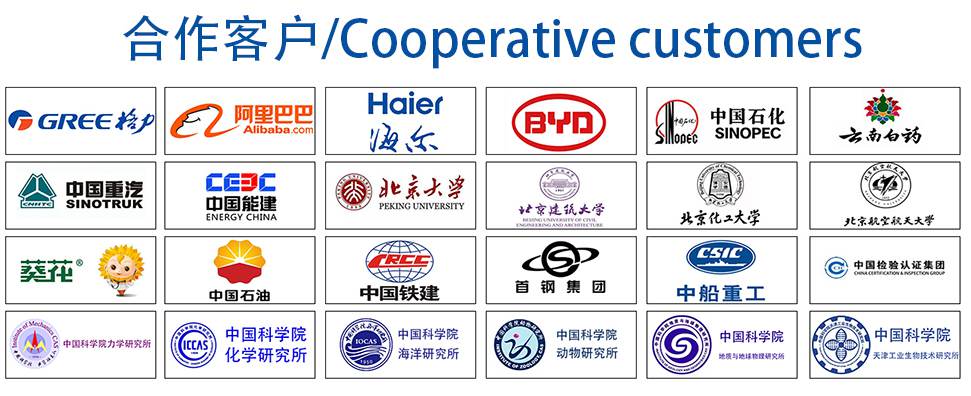