汽车轮毂用铝合金模锻件检测的重要性
随着汽车轻量化趋势的快速发展,铝合金模锻件因其高强度、耐腐蚀性和轻量化特性,已成为汽车轮毂制造的核心材料。然而,轮毂作为车辆行驶安全的关键部件,其性能与质量直接关系到驾驶安全性和车辆稳定性。因此,对铝合金模锻件的检测必须覆盖材料性能、尺寸精度、表面质量及耐久性等多维度指标,以确保产品符合行业标准(如GB/T 38472、ISO 7141)及主机厂的定制化要求。
核心检测项目及方法
1. 材料成分与力学性能检测
铝合金模锻件的材料成分直接影响其力学性能。通过光谱分析仪(OES)或X射线荧光光谱仪(XRF)对Al-Si-Mg系合金中的主元素(如Si含量8-12%、Mg含量0.3-0.6%)进行定量分析,确保符合A356.2等牌号标准。力学性能测试需通过万能试验机测定抗拉强度(≥310MPa)、屈服强度(≥220MPa)和延伸率(≥10%),同时采用布氏硬度计检测硬度值(90-110HB)。
2. 尺寸与几何精度检测
轮毂关键尺寸包括中心孔径(公差±0.05mm)、螺栓孔分布圆直径(PCD)及偏距(ET值)。使用三坐标测量仪(CMM)对轮毂的轴向跳动(≤0.3mm)、径向跳动(≤0.5mm)进行全尺寸扫描,配合激光轮廓仪检测轮辋壁厚均匀性(偏差≤0.2mm)。对于复杂曲面结构,需依据3D数模进行逆向工程对比验证。
3. 表面与内部缺陷检测
表面质量要求轮毂无氧化皮、裂纹或折叠缺陷。采用荧光渗透检测(FPI)识别0.1mm级表面微裂纹,通过粗糙度仪检测Ra值(≤3.2μm)。内部缺陷检测则依靠X射线探伤(可发现φ0.3mm以上气孔)和超声波探伤(UT),确保模锻件内部无缩松、夹杂等缺陷。金相显微镜需分析晶粒度(6-8级)和第二相分布状态。
4. 耐久性与环境适应性测试
动态性能测试包括径向疲劳试验(按SAE J328标准进行50万次循环载荷)、冲击试验(落锤能量≥600J)和盐雾试验(1000小时无红锈)。对于高端车型轮毂,还需进行高速动平衡测试(残余不平衡量≤5g·cm),并通过高低温循环试验(-40℃~150℃)验证尺寸稳定性。
数字化检测技术的应用
当前行业正推进智能化检测技术应用,如基于机器视觉的自动缺陷识别系统(ADS)可实现检测效率提升300%,工业CT扫描可生成三维缺陷分布图。通过大数据分析平台,可建立模锻工艺参数与缺陷率的关联模型,实现质量问题的预测性控制。
结论
汽车轮毂用铝合金模锻件的检测体系需贯穿原材料、工艺过程和成品全生命周期。通过多维度检测数据的交叉验证,不仅能保障产品合规性,更能推动材料优化和工艺改进,为新能源汽车轮毂的轻量化与高性能需求提供技术支撑。
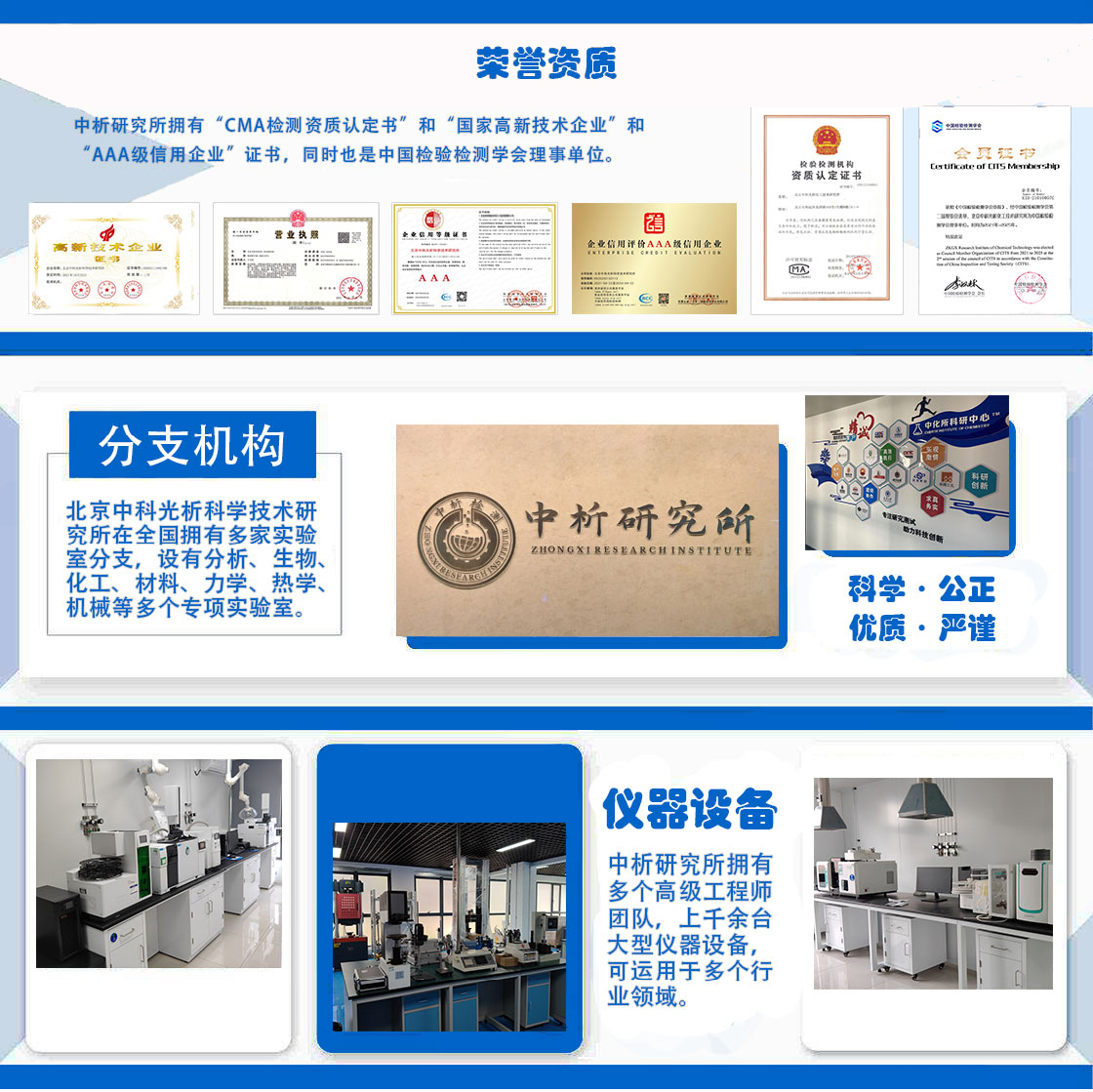
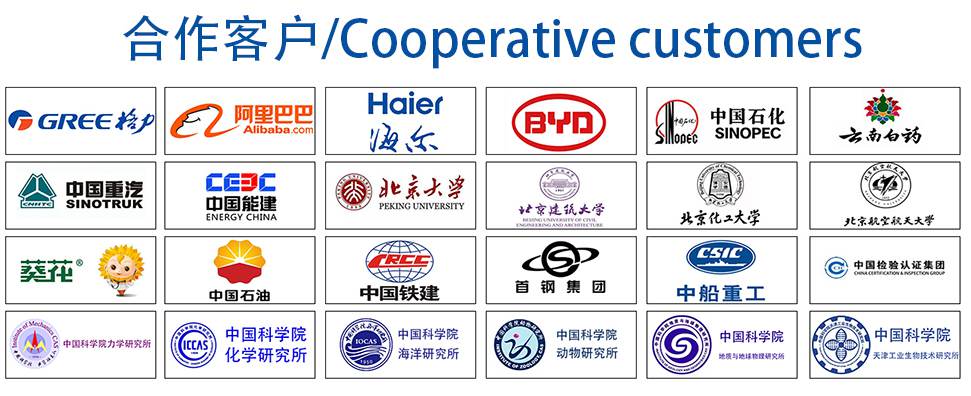