自动卷簧机检测的核心项目与技术要点
自动卷簧机作为弹簧制造行业的核心设备,其性能直接影响弹簧产品的精度、一致性和生产效率。随着制造业对弹簧质量要求的不断提高,设备检测已成为保障生产稳定性的关键环节。系统化的检测覆盖机械结构、电气系统、程序控制、成品质量等多个维度,需通过专业仪器与标准化流程,对设备运行参数、加工误差、动态稳定性等20余项指标进行量化分析,确保设备处于最佳工作状态。
一、机械系统精度检测
采用激光干涉仪检测主轴径向跳动(≤0.005mm),使用千分表测量凸轮轴定位精度误差(±0.01mm)。通过三点弯曲试验评估送线机构的定位重复性,要求送线长度误差≤±0.05mm。导轨平行度检测使用电子水平仪,要求纵向/横向偏差≤5μm/m。
二、电气控制系统检测
使用示波器检测伺服电机电流波形稳定性,谐波畸变率应<5%。通过PLC程序循环测试验证I/O响应时间,要求信号延迟≤3ms。编码器定位精度检测采用闭环反馈测试,要求角度分辨率误差≤0.001°。
三、程序运行参数验证
设置多组典型弹簧参数(线径0.5-6mm,圈数3-20),测试程序计算模型生成速度。对于变节距弹簧,验证程序插补算法的轨迹平滑度,检测拐点处加速度是否超出电机额定值15%。
四、成品质量追溯检测
采用自动影像测量系统检测弹簧几何参数(外径公差±0.02mm,自由高度误差±0.1%)。通过万能材料试验机进行压缩测试,验证负荷特性曲线与设计值的偏差(≤3%)。盐雾试验箱执行72小时腐蚀测试,评估表面处理质量。
五、动态稳定性测试
在连续8小时生产过程中,监测设备温升(电机绕组≤65℃)、振动幅度(X/Y/Z轴≤0.5g)。通过功率分析仪记录能耗曲线,评估全负荷状态下的能效稳定性。同时统计故障停机次数(目标值≤0.5次/班)。
现代自动卷簧机检测已形成涵盖ISO 9001、ASTM F382等标准的完整体系。建议生产企业建立月度预防性检测制度,利用物联网技术实现关键参数的实时监控,结合大数据分析预测设备寿命周期。通过科学的检测机制,可将设备综合效率(OEE)提升至85%以上,废品率控制在0.3%以内。
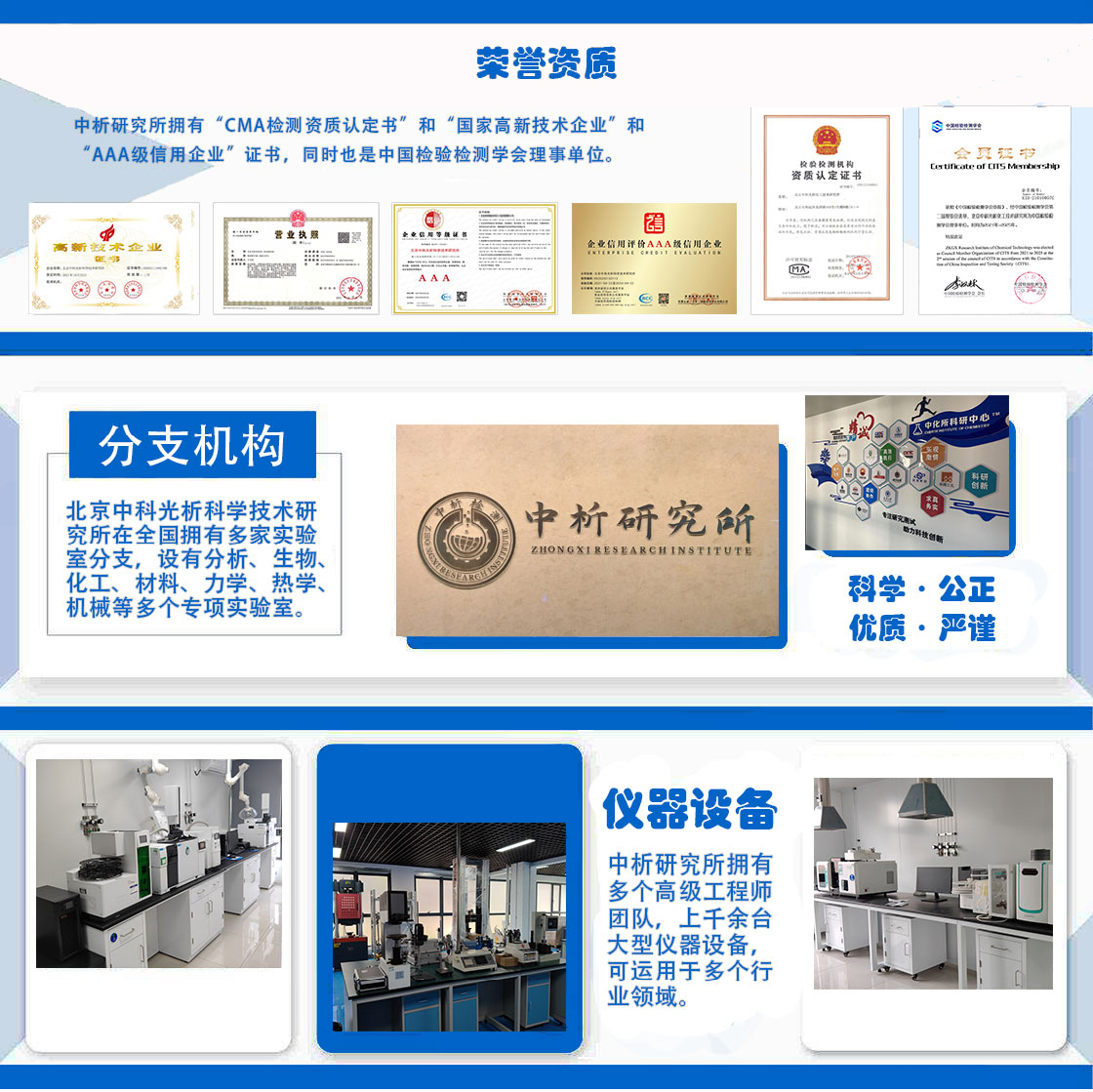
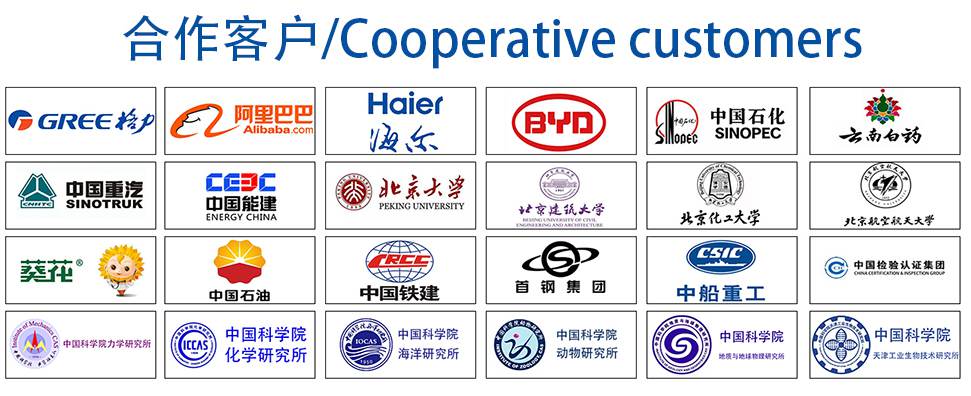