航空用桦木胶合板检测的核心意义
航空用桦木胶合板作为飞机内饰、货舱隔板及辅助结构的关键材料,其性能直接影响飞行安全与设备可靠性。由于该材料需长期承受高低温循环、振动载荷及气压变化等严苛工况,国际航空制造领域对其实施了极为严格的检测标准体系。从原料选择到成品验收,需通过物理性能、力学强度、化学兼容性及耐久性四大类检测,确保其符合ASTM D5681、GB/T 17657等国内外航空材料规范要求。
核心检测项目体系
物理性能检测
1. 厚度公差检测:采用电子千分尺测定各层单板厚度偏差,要求整体厚度误差≤±0.1mm
2. 含水率测试:使用干燥法测定板材平衡含水率,标准值控制在8%-12%区间
3. 密度均匀性检测:通过X射线密度仪扫描分析全板面密度分布,确保波动范围<5%
力学性能检测
1. 抗弯强度测试:依据ASTM D3043标准进行三点弯曲试验,典型值需≥85MPa
2. 层间剪切强度:采用双V形缺口试样法,要求剪切强度≥3.5MPa
3. 拉伸强度检测:通过电子万能试验机测定纵向/横向拉伸性能,保证各向异性比≤1.2
化学兼容性检测
1. 甲醛释放量:参照EN 717-1标准进行气候箱法测试,E0级要求≤0.05ppm
2. 胶合剂耐候性:85℃/95%RH环境下进行1000小时老化测试后保持80%初始粘接强度
3. 阻燃性能验证:依据FAR 25.853标准进行垂直燃烧试验,火焰蔓延时间>60秒
耐久性专项检测
1. 湿热循环测试:-40℃至+70℃温变循环100次后检查分层现象
2. 盐雾腐蚀试验:5%NaCl溶液连续喷雾500小时评估表面腐蚀等级
3. 动态疲劳测试:模拟飞机振动环境进行10^6次循环载荷试验
质量控制的延伸要求
除常规检测项目外,航空级桦木胶合板还需通过超声波探伤检测内部缺陷,使用红外光谱分析胶粘剂成分一致性,并建立全过程追溯系统记录每批次原木产地、胶合工艺参数等溯源信息。这些延伸检测要求体现了航空材料"零缺陷"的质量管理理念。
检测标准的发展趋势
随着复合材料技术进步,最新版AS/EN 9100标准新增了纳米级界面结合力检测要求,采用原子力显微镜(AFM)评估单板纤维与胶层的微观结合强度。同时引入数字孪生技术,通过有限元分析预测材料在极端工况下的失效模式,推动检测体系向智能化、预测性方向演进。
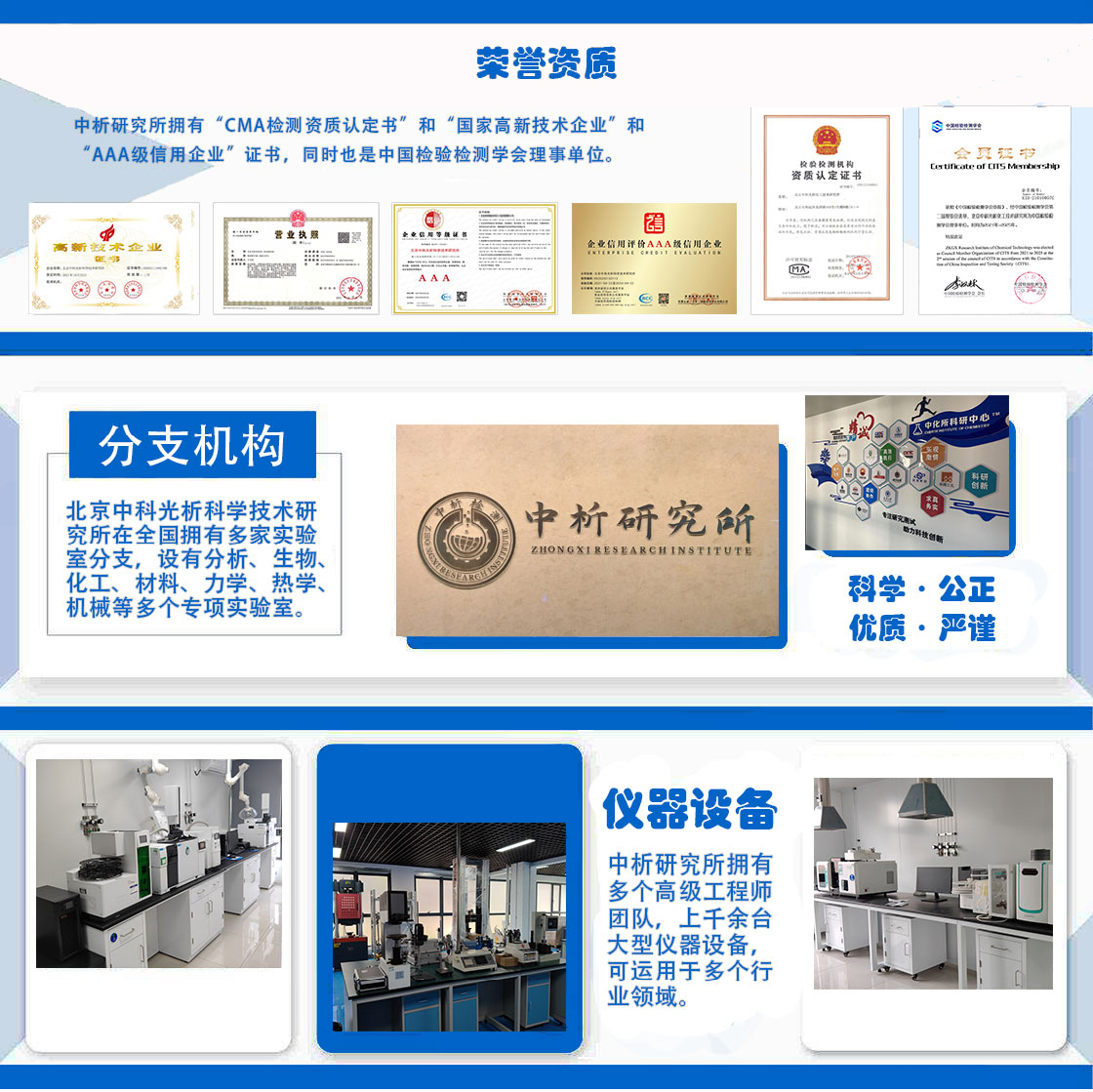
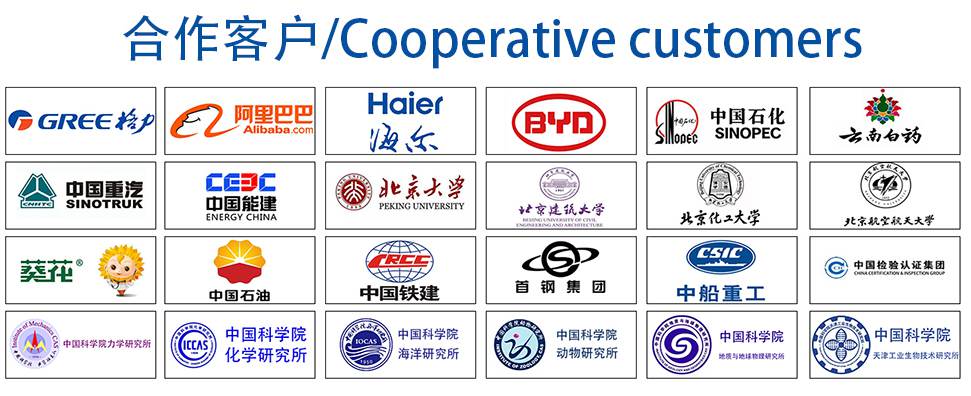