组合机床多工位移动工作台检测的重要性
组合机床多工位移动工作台作为自动化加工的核心部件,其精度、稳定性和可靠性直接影响到工件加工质量和生产效率。随着加工任务日趋复杂化,工作台需频繁进行多轴联动、快速定位和重复切换工位操作,任何微小的偏差都可能导致批量产品报废或设备故障。因此,定期开展系统性检测是保障机床性能的关键环节,涉及几何精度、动态特性、机械传动等多维度参数的测量与校准。
关键检测项目及方法
1. 几何精度检测
使用激光干涉仪或电子水平仪检测工作台的水平度、平面度及导轨直线度。重点关注X/Y/Z轴运动轨迹偏差,需满足ISO 230-1标准要求。对于多工位转台,需额外测量分度精度和重复定位精度,误差应控制在±3"以内。
2. 定位精度与重复定位精度验证
通过球杆仪或光栅尺进行闭环检测,记录各工位实际坐标与理论值的偏差。重复测试5-10次计算标准差,确保重复定位精度≤0.005mm。对于液压/气压驱动的夹紧机构,需同步检测锁紧状态下的位移量变化。
3. 传动系统健康状态评估
• 轴承游隙检测:采用千分表测量滚珠丝杠轴向窜动量,超过0.015mm需更换
• 齿轮齿条磨损分析:使用工业内窥镜检查齿面磨损情况
• 伺服电机扭矩波动测试:借助动态信号分析仪捕捉异常谐波分量
4. 动态性能检测
在满载工况下进行加减速测试,记录工作台的最大速度、加速度及振动频谱。使用三轴加速度传感器监测共振频率,确保与机床结构固有频率错开15%以上安全区间。
特殊工况下的附加检测
针对高温、高湿或重切削环境,需增加以下专项检测:
• 热变形补偿能力测试:通过红外热像仪监测温升曲线,评估热误差补偿算法有效性
• 密封性能验证:向导轨防护罩内注入0.3MPa压缩空气,保压5分钟泄漏量≤5%
• 抗冲击试验:模拟突发负载变化,检测反向间隙突变值是否超限
检测数据智能化管理
建议采用数字化检测平台,将各项参数导入MES系统建立设备健康档案。通过机器学习算法预测关键部件剩余寿命,例如根据丝杠振动特征提前2个月预警疲劳失效风险,实现预测性维护闭环管理。
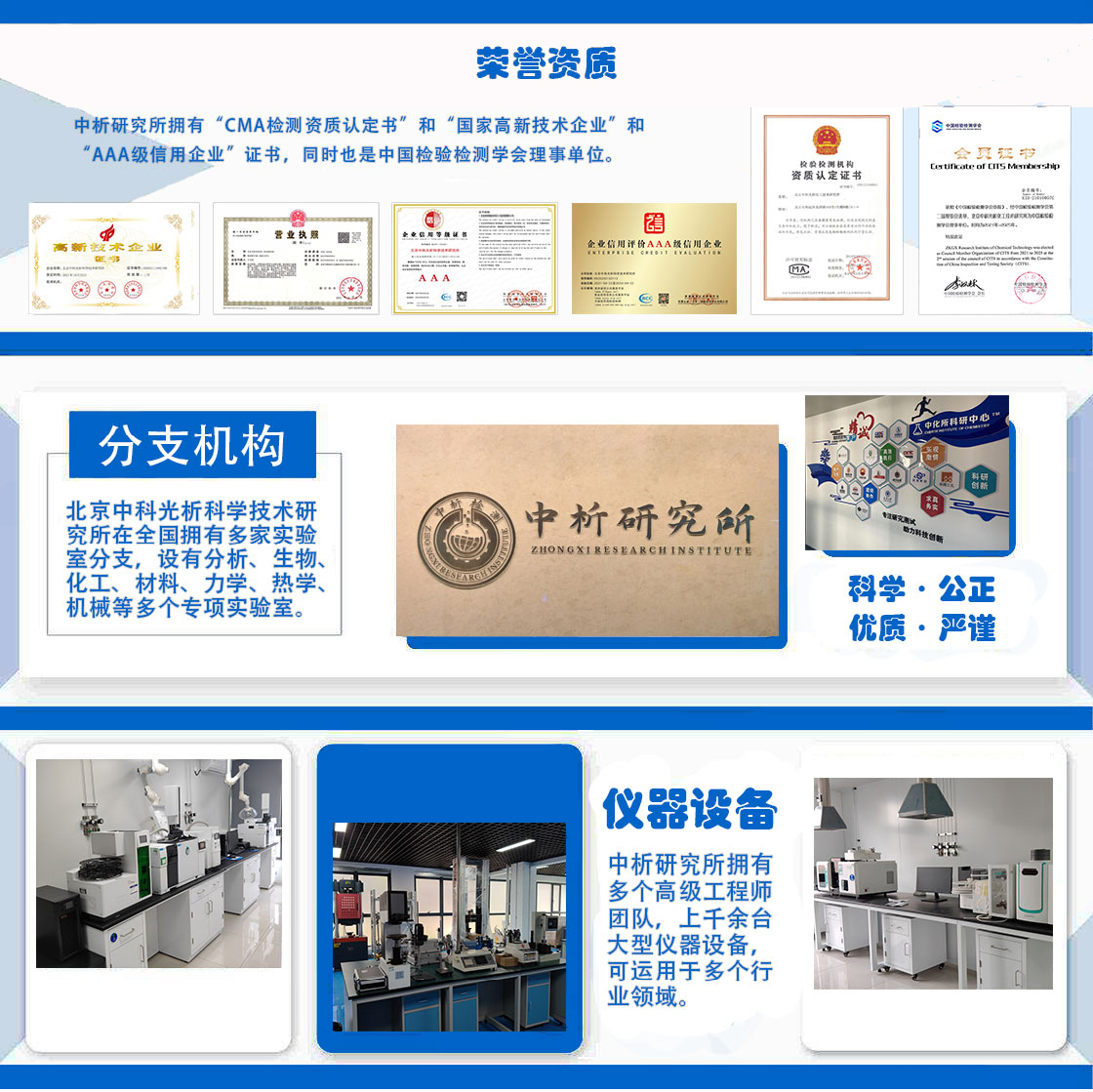
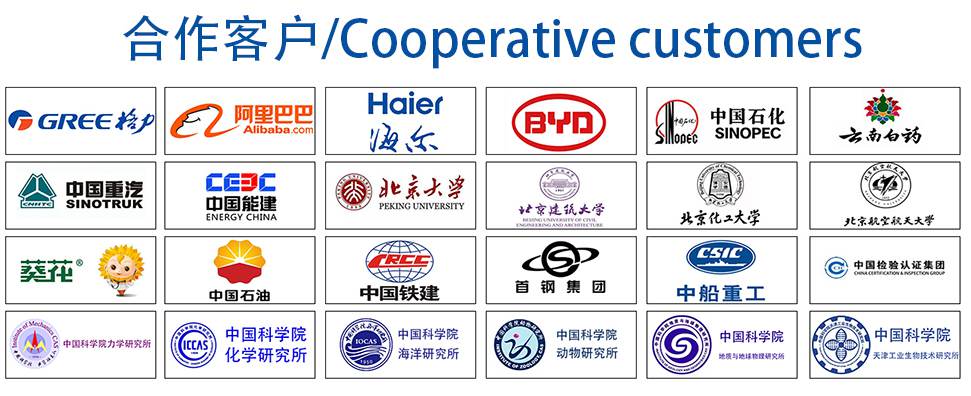