常数补偿器误差检测的核心内容及技术要点
在工业自动化系统、精密仪器仪表及伺服控制领域,常数补偿器作为消除系统固有偏差的关键组件,其误差性能直接影响设备整体精度。由于元器件老化、环境参数波动及制造工艺偏差等因素,补偿器可能产生零点漂移、增益误差等异常现象。误差检测通过量化补偿器输入/输出特性偏差,建立误差修正模型,已成为保障控制系统稳定性和测量精度的必要环节。本文围绕误差检测项目体系展开,重点解析六大核心检测指标及其关联性。
一、零点误差检测
在输入信号为零的基准状态下,通过高分辨率数据采集卡测量补偿器输出端的残余电压值。使用六位半数字万用表进行重复性测试时,需满足EN 60751标准规定的±0.1%FS精度要求。典型故障表现为温度敏感性导致的零点温漂,建议在-20℃至+80℃温箱内进行梯度测试。
二、线性度误差验证
采用标准信号发生器输入0-10V的阶梯电压信号,同步采集输出端响应曲线。通过最小二乘法计算实际特性曲线与理论直线的最大偏离值,工业级补偿器应满足IEC 61298-2规定的0.05%非线性误差限值。特别注意在拐点区域需加密测试点密度。
三、温度漂移系数测定
在恒温试验箱中设置温度变化梯度(通常5℃/min),使用J型热电偶实时监测补偿器壳体温度。记录-40℃~+125℃工况下的零点偏移量和增益变化率,依据MIL-STD-810G标准计算温度系数需≤10ppm/℃。对于汽车电子应用场景,还需进行温度循环冲击测试。
四、动态响应特性分析
通过函数发生器注入阶跃信号或正弦扫频信号,使用100MHz以上带宽示波器捕捉输出响应波形。重点测量上升时间(10%-90%)、建立时间(进入±1%误差带)及相位延迟等参数。伺服系统用补偿器要求阶跃响应超调量<2%,带宽需达到控制回路截止频率的5倍以上。
五、长期稳定性测试
在额定负载条件下进行1000小时持续老化试验,每8小时记录一次零点偏移数据。采用Allan方差分析法处理测试数据,评估由元器件老化引起的慢时变误差。航空航天领域要求年漂移量不超过满量程的0.003%,测试周期需延长至3000小时。
六、电磁兼容性误差评估
依据IEC 61000-4系列标准,在电波暗室中执行辐射抗扰度(80MHz-1GHz)和传导干扰(150kHz-80MHz)测试。监测补偿器在30V/m场强下的输出抖动值,工业环境应用要求电磁干扰引起的附加误差<0.02%FS。对于医疗设备等敏感场景,还需增加静电放电(ESD)8kV接触放电测试。
通过上述检测项目构建的完整评估体系,可准确诊断补偿器的误差来源:当零点误差超标时需检查基准电压源稳定性;出现非线性异常应重点检测运算放大器开环增益;温度漂移异常提示需要优化热设计或选用低温漂电阻网络。现代智能补偿器已集成自诊断功能,通过内置DAC和ADC实现闭环自校准,大幅提升误差检测效率。
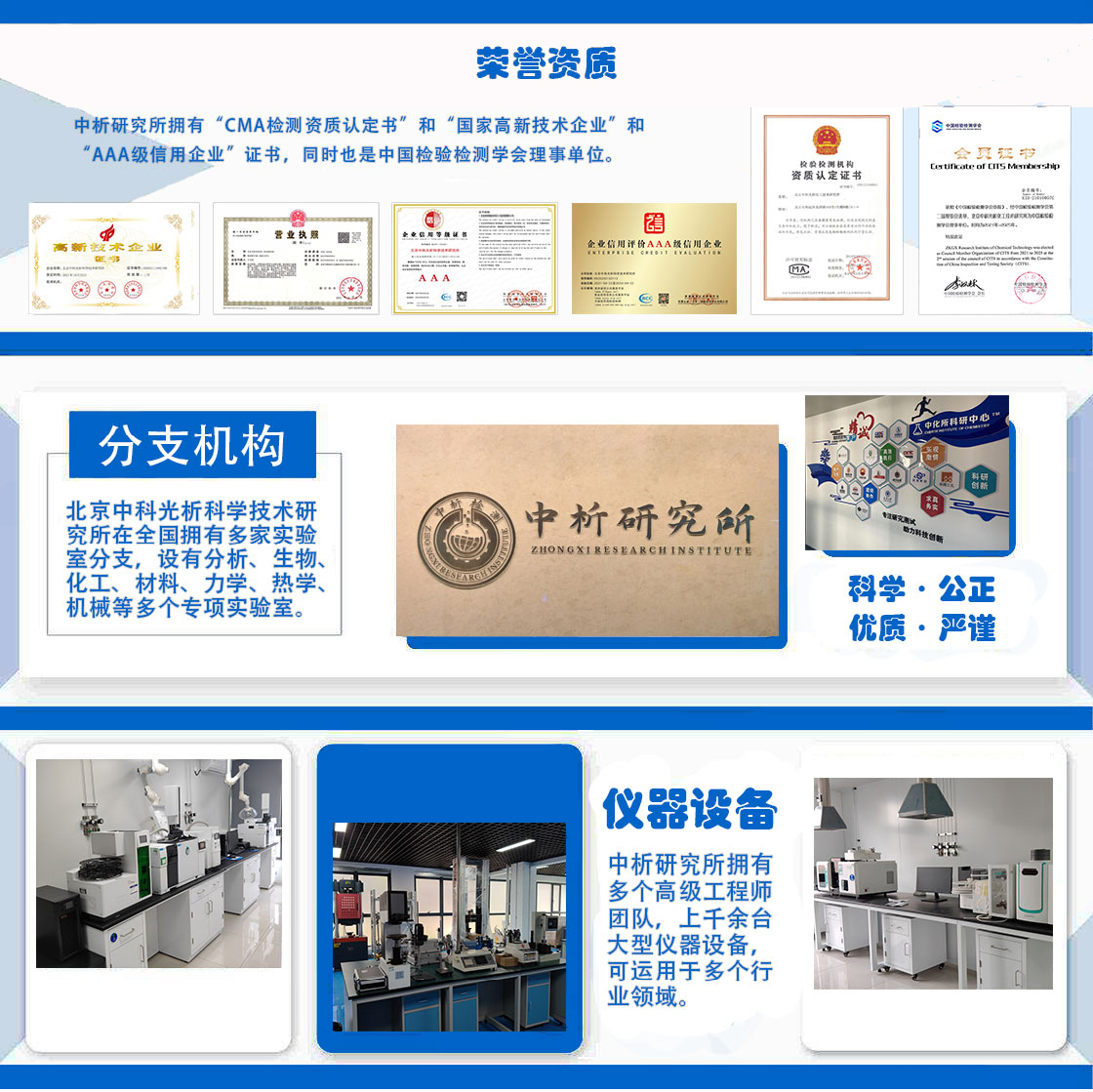
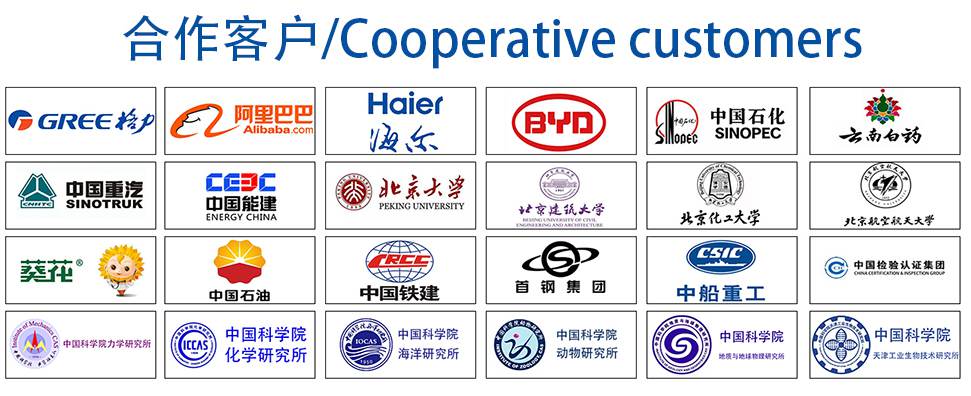