气路密封性检测的重要性
气路系统的密封性是保障设备安全运行和高效工作的核心要素之一。在工业制造、医疗器械、航空航天、汽车制造等领域,气路(如压缩空气管路、真空管路、气体输送系统等)的泄漏可能导致能源浪费、设备性能下降,甚至引发安全事故。例如,氧气输送系统的泄漏可能引发爆炸风险,而医疗呼吸机气路的微小泄漏则可能危及患者生命。因此,气路密封性检测不仅是设备安装与维护的必要环节,更是质量控制和安全生产的关键步骤。
气路密封性检测的核心目标是发现并量化系统中的泄漏点,确保气路在额定压力或真空条件下保持稳定。常用的检测方法包括压力测试、气泡测试、流量测试以及齐全的超声波检测技术等。随着智能化技术的发展,自动化检测设备与数据监测系统的结合进一步提高了检测效率和准确性。
气路密封性检测的主要项目
1. 气密性测试(压力保持测试)
气密性测试是气路检测的基础项目,通过向系统内充入压缩气体(如氮气或空气)并保持一定压力,观察压力变化来判断是否存在泄漏。检测时需记录初始压力值,并在规定时间内监测压力下降幅度。若压力下降超过标准阈值,则判定系统存在泄漏。此方法适用于管道、阀门、接头等部件的整体密封性评估。
2. 泄漏点定位(局部泄漏检测)
对于已确认存在泄漏的系统,需进一步定位具体泄漏位置。常用方法包括:
- 肥皂水检测法:在可疑区域涂抹肥皂水,观察是否产生气泡。
- 超声波检测法:利用超声波传感器捕捉泄漏点产生的高频声波信号。
- 红外热成像法:通过温度变化识别泄漏区域的气流异常。
3. 压力衰减测试
压力衰减测试通过持续加压并测量压力随时间的变化率,精确计算泄漏量。该方法适用于对密封性要求极高的场景,例如燃料电池的氢气输送管路或半导体制造中的惰性气体系统。检测中需结合温度补偿算法,避免环境温度波动对结果的影响。
4. 流量测试
通过测量气体流量与系统设计流量的偏差,间接评估密封性。若实际流量显著高于预期值,可能表明存在泄漏。此方法常用于连续运行的气路系统(如空压机管路),可结合流量计和压力传感器实现实时监测。
5. 真空保持测试
针对真空系统(如真空泵管路)的密封性检测,需抽真空至目标值后关闭阀门,监测真空度变化。若真空度快速下降,说明系统存在泄漏。此测试对检测仪器的精度要求较高,通常需使用高灵敏度的真空计。
6. 气体成分分析
对于输送特殊气体(如易燃、有毒气体)的管路,可通过气体传感器或质谱仪分析环境中的气体浓度,判断是否存在泄漏。此方法适用于高风险场景,例如化工厂的氯气输送管道。
检测方法与设备选择
气路密封性检测需根据系统特性选择合适的方法与设备:
- 便携式检漏仪:适用于现场快速检测,如汽车制动系统的气密性检查。
- 自动化检测平台:集成压力控制、数据采集与分析功能,适合批量生产中的质量检测。
- 无损检测技术:如激光干涉仪或氦质谱检漏仪,用于超低泄漏率场景(如航天器燃料管路)。
应用场景与行业标准
不同行业对气路密封性的要求差异显著。例如:
- 汽车制造业要求气动刹车系统的泄漏率低于0.1 mL/min。
- 医疗设备中,呼吸机管路需通过ISO 5361标准下的严格气密性测试。
- 工业压缩空气系统通常遵循ISO 8573标准,确保空气质量与密封性达标。
总结
气路的密封性检测是保障系统安全与效率的核心环节,需结合科学的检测项目、高精度设备和行业规范执行。随着物联网与人工智能技术的应用,未来的气路检测将更加智能化,实现实时监控与预测性维护,进一步降低泄漏风险,提升工业生产的可靠性。
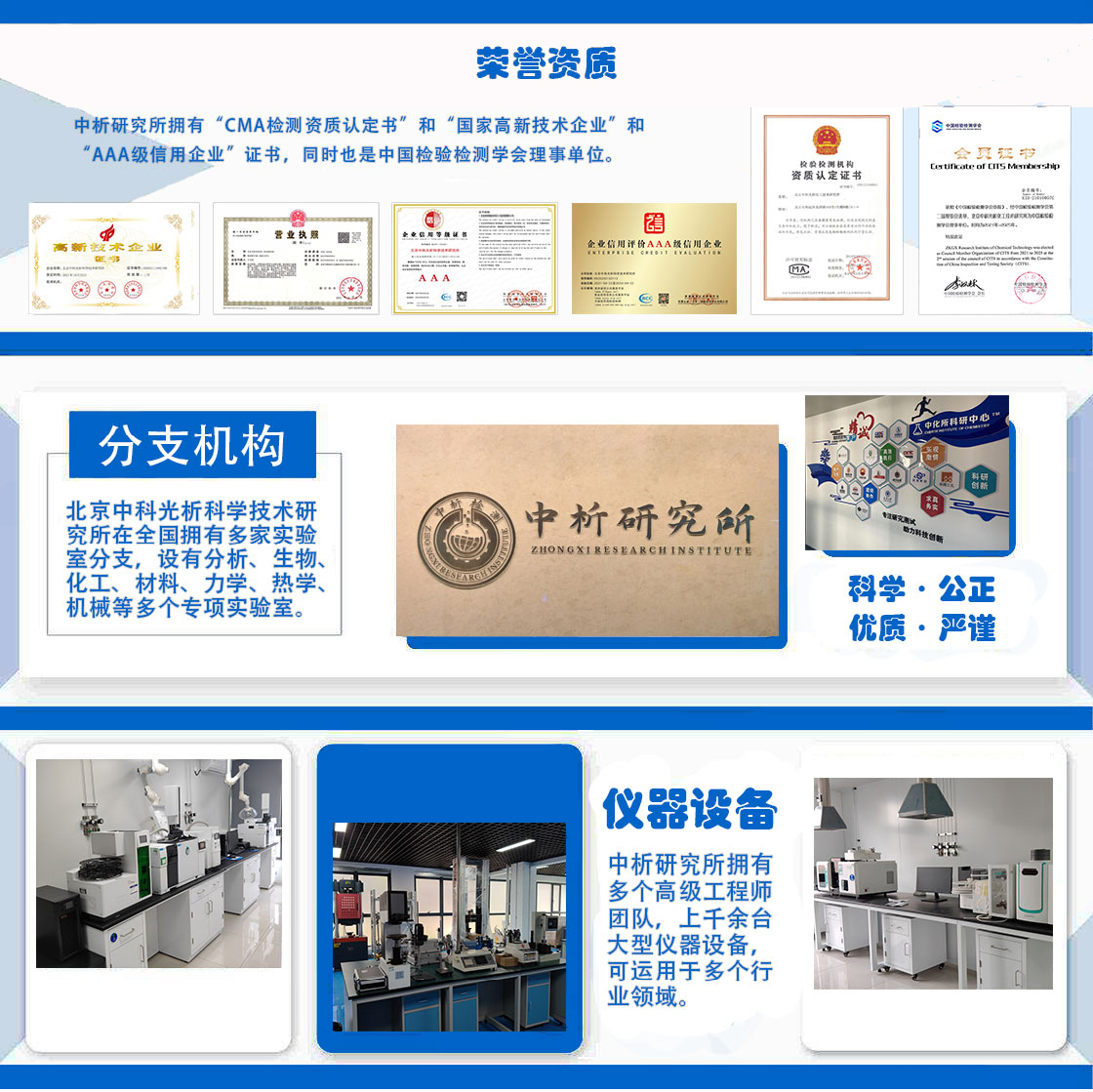
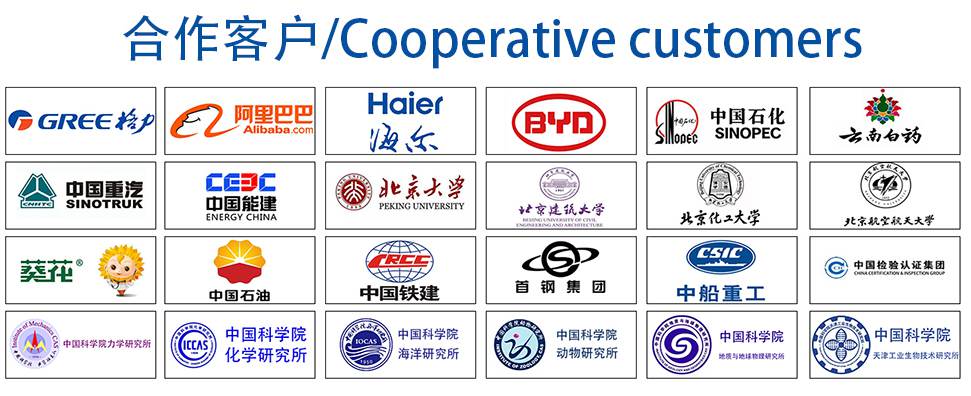