随着国家双碳战略的深入推进,节能技术改造项目已成为工业企业提质增效的重要手段。作为项目成效验证的核心环节,节能检测通过专业化的测试手段,能够准确评估改造工程的实际节能量,发现潜在运行隐患,并为后续优化提供数据支撑。依据《工业企业能源管理导则》(GB/T 15587)要求,项目竣工后需开展系统性检测,确保技术改造达到预期节能目标。
一、热工系统效能检测
针对锅炉、窑炉等热力设备,运用烟气分析仪、红外热像仪等设备,检测燃烧效率、排烟温度、炉体散热等关键指标。重点验证余热回收装置换热效率是否达到设计值的±5%误差范围,同步检测保温层导热系数是否满足GB/T 4272标准要求。
二、电力系统谐波与能效检测
使用电能质量分析仪对改造后的变频器、无功补偿装置进行检测,包括总谐波畸变率(THD)、功率因数等参数。对照《三相异步电动机经济运行》(GB/T 12497)标准,测试电机负载率与效率曲线匹配度,确保设备在最佳工况区间运行。
三、暖通空调系统性能检测
采用温湿度巡检仪、风量罩等设备,检测热泵机组COP值、输配系统水力平衡度、末端设备能效比等指标。重点验证智能控制系统对室内环境参数的调节精度,确保空调系统综合能效比(EER)提升幅度不低于改造方案的承诺值。
四、照明系统优化效果检测
依据《建筑照明设计标准》(GB 50034),使用照度计、光谱分析仪对LED灯具进行光通量维持率、色温一致性检测。通过对比改造前后单位面积照明功率密度(LPD),验证节能率是否达到30%以上的行业基准值。
五、余热回收系统检测
对ORC发电、热管换热等装置开展热力学性能测试,测定热媒流量、温差利用效率等参数。通过热平衡计算验证系统整体余热回收率,检测排放烟气温度是否低于改造设计阈值,确保符合《工业余能资源评价方法》技术要求。
六、数据监测系统验证
对新建的能源管理系统进行72小时连续测试,校验计量仪表的精度等级是否达到0.5级要求。检测数据采集完整率、传输稳定性等指标,验证能耗预测模型与实际运行数据的吻合度,确保在线监测系统满足GB/T 28750标准。
七、环境排放指标检测
按照《大气污染物综合排放标准》,对改造后单位产品碳排放强度、废气排放浓度等进行取样检测。重点监测NOx、SO2等污染物的减排效果,验证节能改造与环境效益的协同提升效果。
八、设备运行效率追踪检测
在项目投运3个月后开展能效复测,通过对比同期生产数据,分析设备实际运行效率与验收检测值的偏差率。对能效衰减超过5%的设备启动专项诊断,排查机械磨损、控制系统失调等问题。
九、系统联动控制检测
模拟不同生产工况,测试能源供应系统与生产设备的协调控制能力。验证负荷调节响应时间是否小于设计值,检测联锁保护装置动作准确性,确保全系统具备智能调峰能力。
十、改造效果持续性验证
建立为期1年的能效跟踪机制,每月采集关键设备运行数据。采用回归分析法评估节能效果的稳定性,对波动幅度超过8%的异常数据启动故障溯源,确保技术改造效益持久可靠。
节能检测机构应依据GB/T 15316《节能监测技术通则》开展检测工作,检测报告须包含基准能耗、实测节能量、节能率计算过程等核心要素。企业应根据检测结果及时优化运行策略,对未达标项目启动整改,真正实现技术改造投入的价值转化。
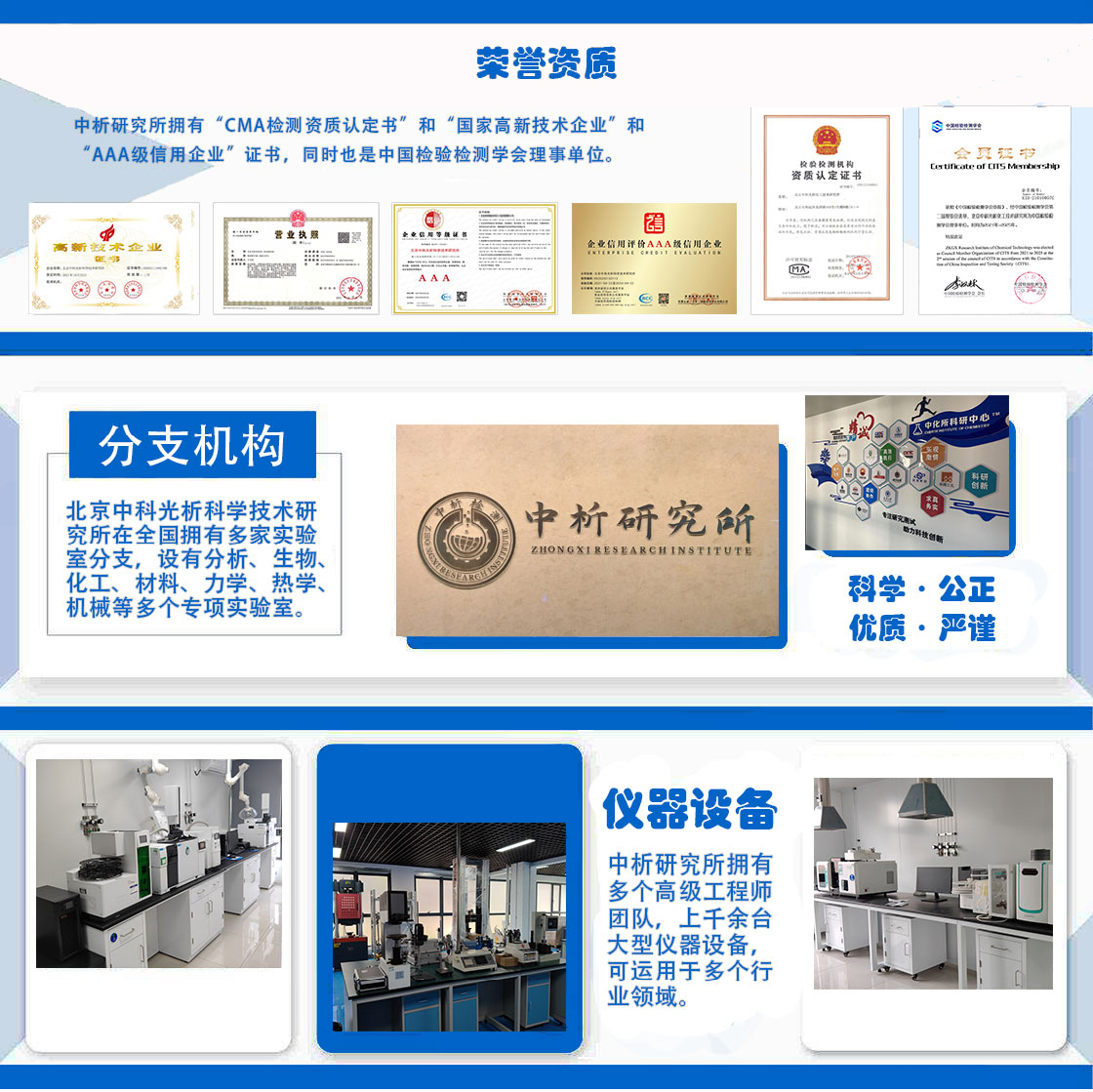
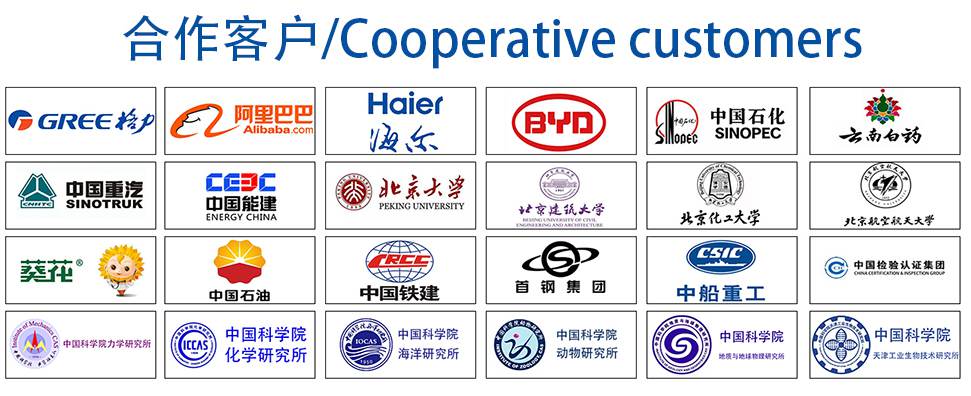