灯泡用氩气检测的重要性与技术要点
在现代照明工业中,惰性气体氩气(Ar)被广泛应用于白炽灯泡和节能灯的填充工艺中。氩气的化学惰性能有效减缓钨丝在高温下的氧化速率,同时降低热量损耗,从而延长灯泡使用寿命并提升发光效率。为确保灯泡性能与安全性,氩气的纯度、填充压力及密封性检测成为生产过程中不可或缺的关键环节。根据国际电工委员会(IEC)标准及各国行业规范,氩气检测需覆盖气体成分分析、泄漏测试、压力稳定性验证等多个维度,并通过精密仪器与标准化流程实现精准控制。
氩气纯度检测
氩气纯度直接影响灯泡的性能表现,通常要求工业级氩气纯度≥99.996%。检测时采用气相色谱仪(GC)或质谱分析仪,通过分子筛分离技术对气体中的氧气(O₂)、氮气(N₂)、水分(H₂O)等杂质进行定量分析。若杂质含量超标,会导致灯丝氧化加速、光效降低甚至玻璃壳体破裂风险。专业实验室还会通过红外光谱法检测痕量碳氢化合物,确保气体符合无污染填充要求。
氩气填充压力检测
灯泡内部氩气压力需严格控制在0.3-0.5MPa范围内,过高会导致玻璃外壳承压过大,过低则无法抑制钨丝蒸发。检测使用高精度压力传感器配合自动化充气系统,实时监测充气过程中的压力变化曲线。量产环节中,压力衰减测试是核心项目:将灯泡置于恒温环境中静置24小时后复测压力值,衰减率需低于0.5%/年,以此验证密封结构的可靠性。
氩气泄漏检测
泄漏检测分为宏观与微观两个层级。宏观检测采用负压气泡法,将灯泡浸入特制检测液后观察气泡生成情况;微观检测则使用氦质谱检漏仪,通过氦气示踪法检测细微泄漏(灵敏度可达10⁻⁹ Pa·m³/s)。近年新兴的激光吸收光谱技术(TDLAS)能实现非接触式在线检测,特别适用于高速生产线中实时监控氩气泄漏率。
工艺环境交叉污染检测
在灯泡封装过程中,需同步监测生产环境中氩气的浓度分布。通过便携式气体分析仪对充气工位、储存区进行多点采样,确保环境氩气浓度维持在安全阈值(通常≤19.5%体积分数)以下,避免因局部富集导致缺氧风险。同时需检测残留的焊接保护气体(如氮气)是否混入氩气系统,防止交叉污染影响灯泡性能。
总结
氩气检测贯穿灯泡生产的原料验收、充装工艺、成品质检全流程,其技术指标直接关联产品的光效、寿命及安全性。通过气相色谱、质谱分析、压力传感与氦检漏等综合检测手段,配合ISO/IEC 17025认证实验室的质量管理体系,可确保氩气参数完全符合照明器具的严苛要求。随着智能化检测设备的普及,氩气检测正朝着更高精度、更快响应、全流程自动化的方向持续升级。
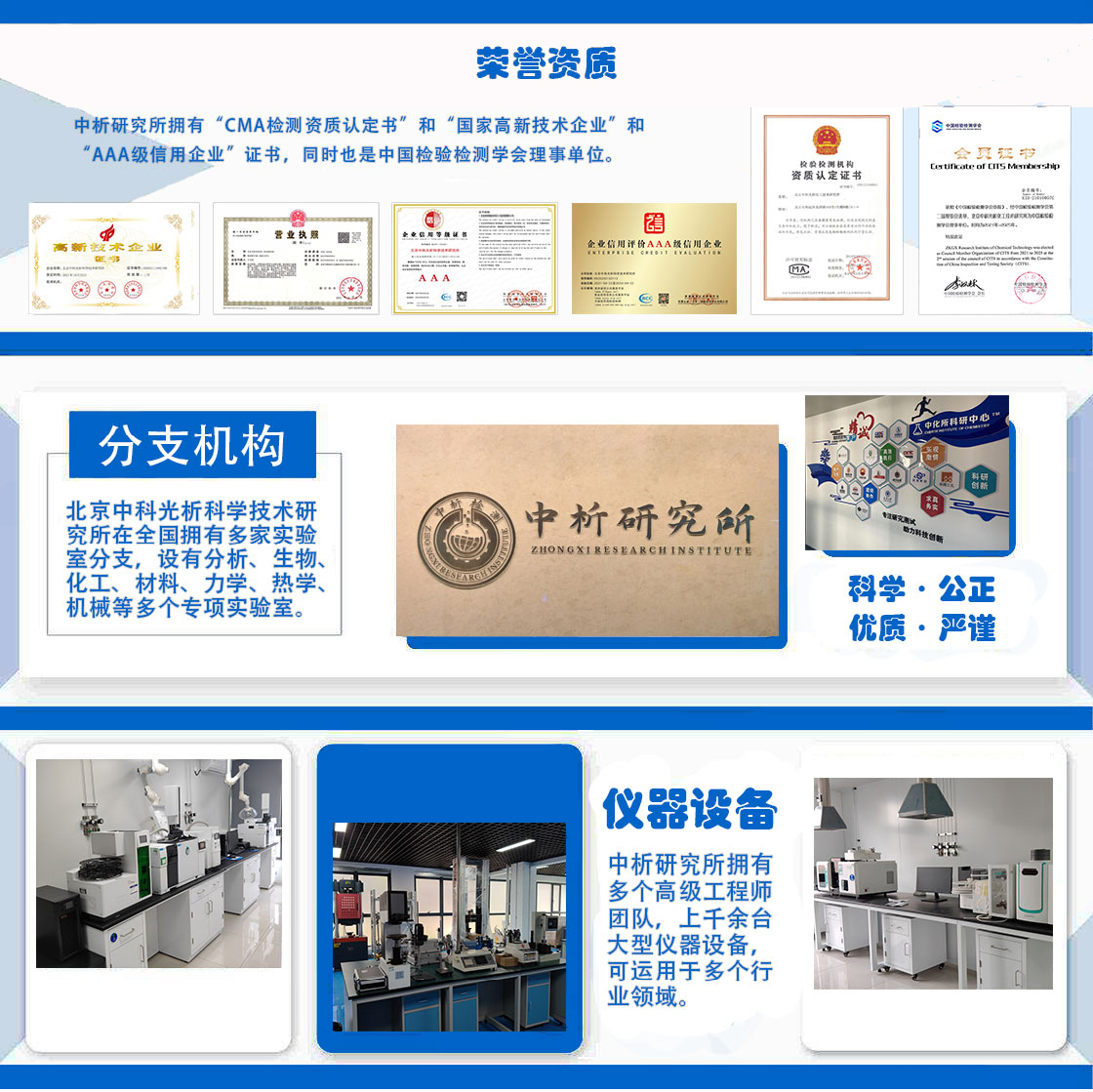
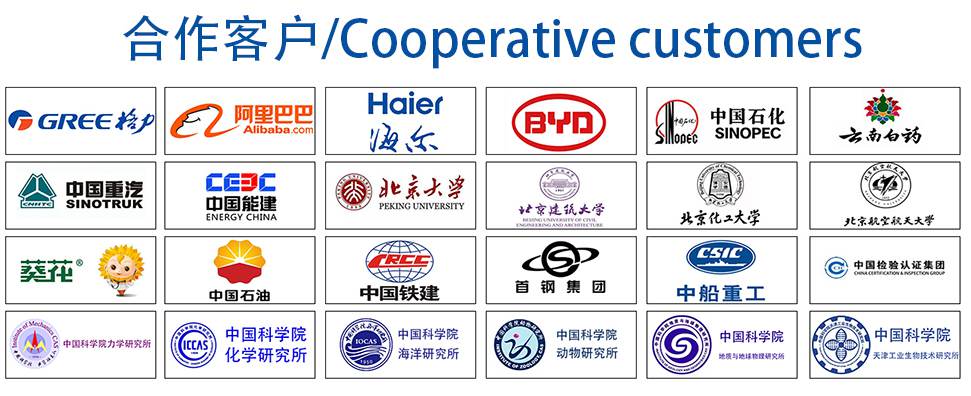