电池包和系统检测:新能源汽车安全与性能的核心保障
随着新能源汽车产业的快速发展,电池包及其管理系统(BMS)作为电动汽车的"心脏",其安全性、可靠性和耐久性成为行业关注的核心。电池包检测通过系统化的测试流程和严苛的评估标准,覆盖从电芯单体到整体系统的全生命周期质量验证,是确保车辆安全运行、延长电池寿命、提升用户体验的关键技术手段。根据行业统计,范围内超过60%的新能源汽车召回案例与电池系统缺陷相关,这使得电池检测从研发到量产的每个环节都显得尤为重要。
核心检测项目体系
1. 电性能测试
包括容量标定、充放电效率、循环寿命等关键指标验证。通过高精度充放电测试设备模拟不同工况,检测电池包的电压一致性、内阻变化和能量衰减特性。例如1000次循环测试需要持续3-6个月,容量保持率需达到80%以上才符合行业标准。
2. 环境适应性测试
在气候箱中模拟-40℃至85℃极端温度、95%高湿度的恶劣环境,验证电池包的充放电性能和安全保护机制。重点考察低温条件下的容量衰减和高温环境的热失控风险,满足GB/T 31467.3-2015等国家标准要求。
3. 安全性能验证
包含机械安全测试(振动、冲击、挤压)、电气安全测试(过充/过放、短路保护)、热安全测试(热扩散、针刺)三大维度。其中针刺测试需在专用防爆箱内进行,通过钢针穿透电芯触发内部短路,监测是否发生起火爆炸。
4. BMS功能验证
对电池管理系统的SOC估算精度、均衡控制、故障诊断等32项核心功能进行台架测试。采用硬件在环(HIL)技术模拟实际工况,验证SOC估算误差需控制在±3%以内,电压采样精度达到±5mV级别。
5. 热管理系统检测
通过CFD仿真与实测结合,评估液冷/风冷系统的冷却效率和温度均匀性。要求电池包内部温差不超过5℃,在快充工况下能将电芯温度稳定控制在45℃安全阈值以下。
智能化检测技术发展
新型X射线断层扫描(CT)技术可无损检测电芯内部缺陷,AI算法支持的海量数据建模能预测电池老化趋势,无线BMS测试系统实现毫秒级故障响应。这些创新技术将检测效率提升40%以上,推动行业向智能化检测时代迈进。
从实验室验证到整车匹配,电池包检测贯穿着产品开发的全流程。随着固态电池、CTC技术等新形态电池系统的出现,检测标准和方法也在持续演进,为新能源汽车的规模化应用构筑起坚实的技术防线。
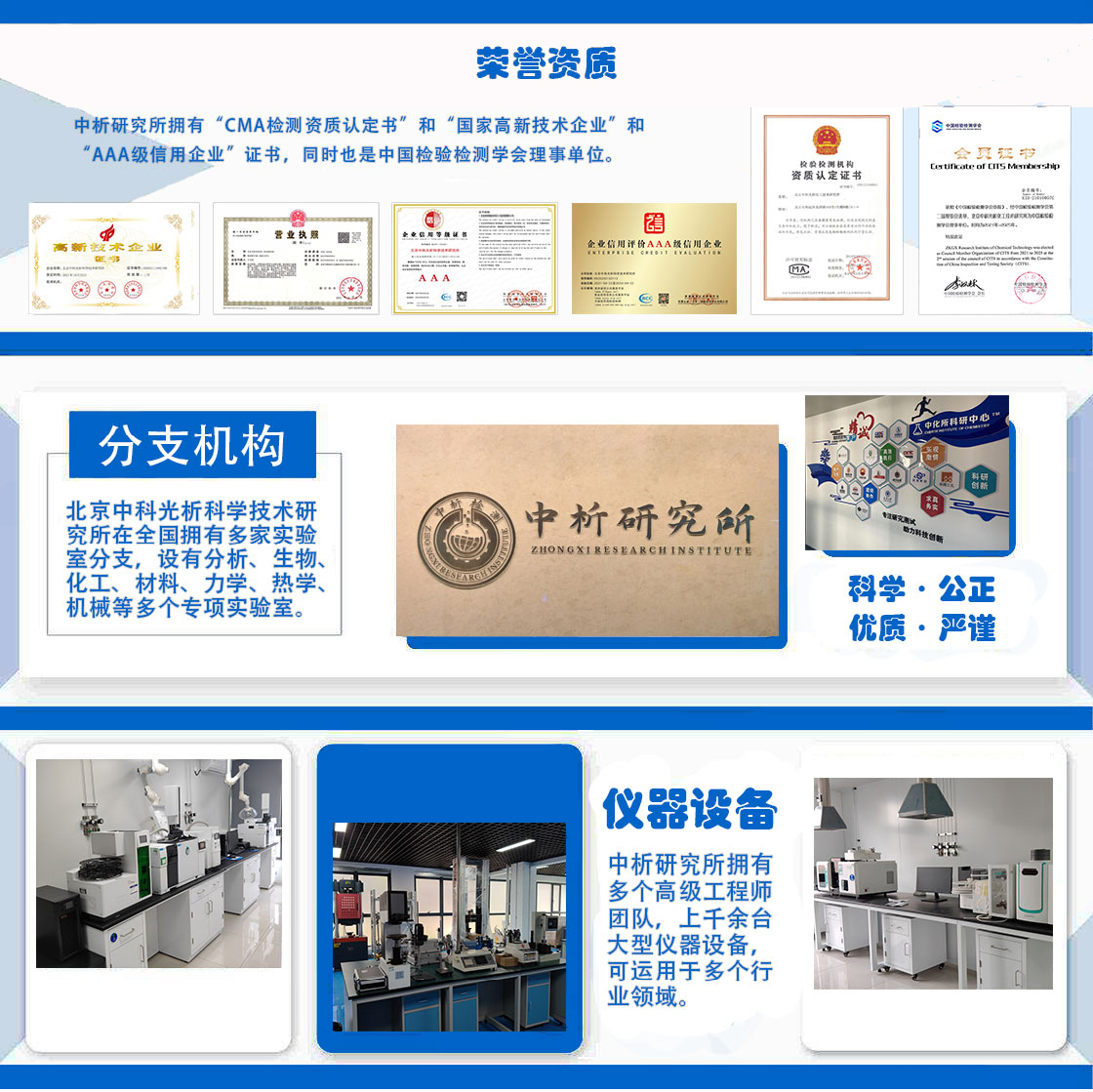
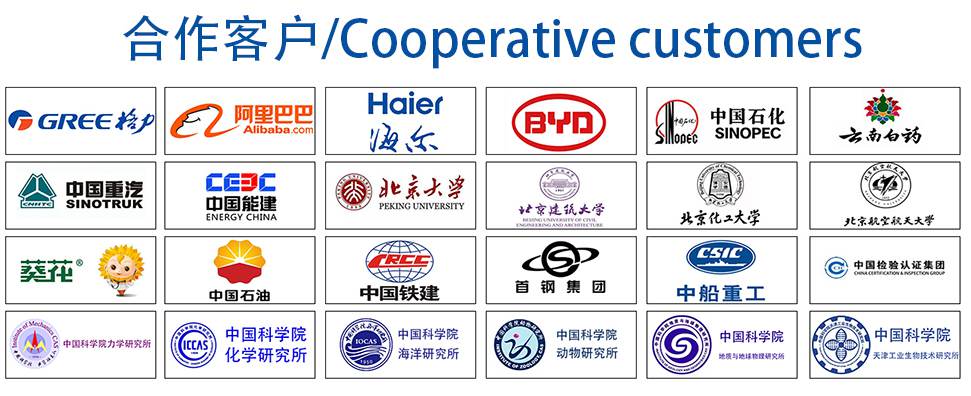