钢质管道聚烯烃胶粘带防腐层检测的重要性
钢质管道在石油、天然气、化工等领域的输送系统中广泛应用,其长期暴露于复杂环境中易受腐蚀影响。聚烯烃胶粘带防腐层作为一种高效防腐技术,通过物理隔离和化学保护双重作用延缓管道腐蚀,延长使用寿命。然而,防腐层在施工、运行过程中可能因机械损伤、老化、剥离等问题失效,导致管道安全隐患和巨额经济损失。因此,定期开展防腐层检测是保障管道安全运行、降低运维成本的关键环节。
防腐层检测的核心项目及方法
1. 防腐层厚度检测
使用磁性测厚仪或超声波测厚仪,依据SY/T 0414标准对胶粘带防腐层的总厚度及单层厚度进行测量。检测区域需覆盖焊缝、弯头等易出现厚度不足的部位,确保整体厚度符合设计要求(通常≥0.7mm),防止因厚度不均导致的局部腐蚀穿透。
2. 剥离强度测试
通过90°或180°剥离试验机,测定胶粘带与钢管基体或层间粘接强度。根据GB/T 2792标准,常温下剥离强度应≥20N/cm,高温(50℃)环境下需≥15N/cm。该指标直接反映防腐层抗机械应力能力,避免因粘接失效引发分层。
3. 电绝缘性能检测
采用高压电火花检测仪(检测电压5kV/mm)扫描防腐层表面,识别针孔、裂纹等缺陷。同时使用兆欧表测量层电阻率,要求≥1×10⁸Ω·m,确保防腐层具备良好电绝缘性,阻断电化学腐蚀通路。
4. 附着力现场评估
使用划格法(ASTM D3359)在管道表面划出1mm×1mm网格,观察胶带剥离情况。合格标准为切口边缘光滑无脱落,剥离面积≤5%。该方法可快速判断施工质量及胶粘带与基材的兼容性。
5. 耐环境老化检测
通过实验室加速老化试验(如QUV紫外老化、盐雾试验)模拟长期环境侵蚀,检测防腐层抗紫外线、耐酸碱及抗渗透性能。老化后要求厚度损失率≤10%,剥离强度保持率≥80%。
6. 外观与连续性检查
采用目视检查结合高清摄像记录,重点排查褶皱、气泡、搭接不良(要求搭接宽度≥25mm)等表观缺陷。对于埋地管道,配合DCVG(直流电压梯度)或CIPS(密间隔电位测量)技术定位防腐层破损点。
7. 阴极剥离试验
依据NACE TM0174标准,在实验室模拟阴极保护条件下,将试样浸泡于电解质溶液中28天,测量剥离半径。合格标准为剥离半径≤8mm,验证防腐层在阴极保护系统中的长期稳定性。
8. 现场补口质量检测
对焊接接头补口区域进行全数检测,采用热收缩带专用检测仪验证加热均匀性,并使用红外热成像技术排查未熔合、虚粘等隐患,确保补口处防腐性能与主体管道等效。
检测实施要点与规范
检测前需清理管道表面并确认环境温湿度(推荐15-35℃,湿度≤85%)。检测数据需按ISO 21809-3标准归档,结合GIS系统建立腐蚀数据库。对于高风险管段(如穿越河流、人口密集区),检测频率应提高至每年1次,并采用多技术融合的综合评价方法。
通过系统性检测与数据对标,可精准评估防腐层状态,制定差异化维护策略,最终实现管道全生命周期成本优化与安全风险可控。
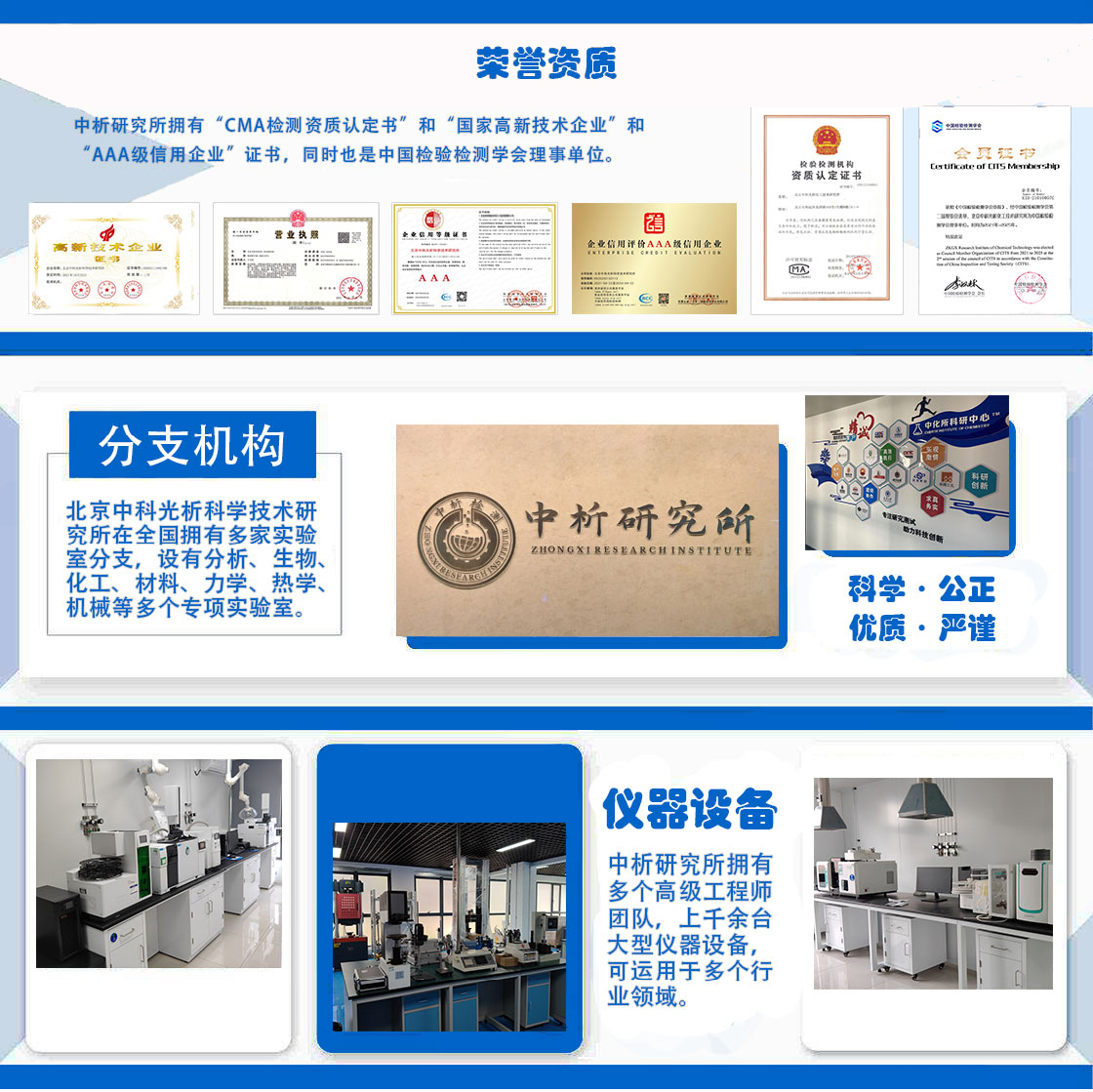
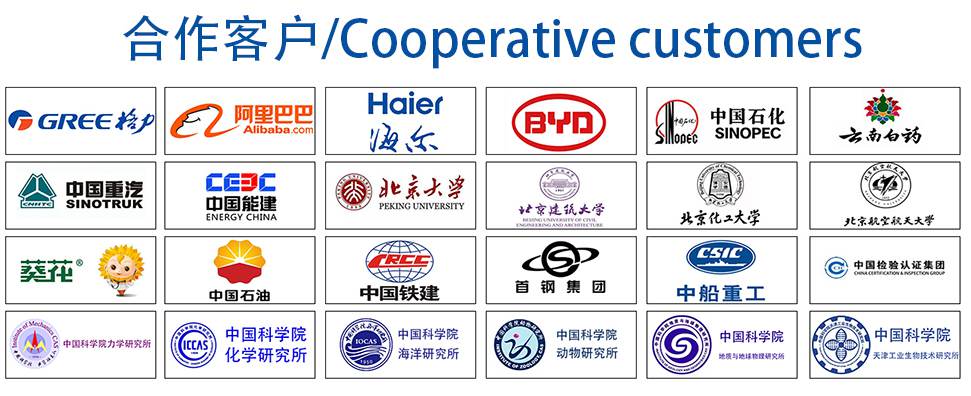