随着高端装备制造、精密工程等领域的快速发展,垂直度检测作为几何量测量的关键技术环节,其重要性日益凸显。据国际精密测量协会(IPMA)2024年报告显示,工业领域因垂直度偏差导致的设备损耗年均达47亿美元,占机械故障总量的21%。在半导体晶圆加工、航空航天构件装配等场景中,0.01mm级垂直度偏差即可引发级联失效。本项目通过建立多尺度垂直度检测体系,不仅实现了对微观纳米结构与宏观工程构筑物的精准测量,更构建起连接设计规范与生产实践的质量桥梁,为智能制造提供关键数据支撑。
多模态融合检测技术原理
基于激光跟踪仪与机器视觉的协同测量系统,突破传统单点检测的局限。采用分频干涉技术(DFI)构建三维空间基准面,通过高分辨率CCD相机捕捉特征点云数据,结合自适应滤波算法消除环境振动干扰。当检测核电乏燃料储罐垂直度时,系统可同步获取毫米级宏观偏差与微米级局部形变数据,实现全尺度精度覆盖。值得关注的是,该技术方案在"基于深度学习的多源数据融合"方向取得突破,使复杂工况下的检测效率提升40%。
智能化实施流程体系
项目实施采用PDCA循环管理模式,分为基准建立、动态采集、偏差分析三个阶段。在轨道交通接触网支柱检测场景中,首先利用北斗地基增强系统建立空间坐标系,随后部署移动式测量机器人进行亚毫米级实时扫描。通过开发专用分析软件,可将采集数据与BIM模型自动比对,生成带有公差带的三维可视化报告。据中国计量科学研究院实测数据,该流程使高铁接触网系统安装调试周期缩短22%,关键节点合格率提升至99.6%。
跨行业应用实践案例
在新能源电池极片制造领域,应用微米级垂直度在线检测系统后,叠片工艺合格率从93%提升至98.5%。该系统采用激光三角法原理,在120m/min产线速度下仍能保持±2μm测量精度。某特高压换流站工程中,针对阀厅钢结构实施三维激光扫描,成功将18米高支撑柱垂直度偏差控制在0.5mm内,低于国标允许值30%。这些实践验证了"智能测量-工艺优化"闭环管理模式的可行性。
全链条质量保障机制
构建"标准-设备-人员"三维度质控体系,通过ISO 17025实验室认证确保测量溯源性。建立包含32项技术指标的设备校准规程,定期开展测量不确定度评定。在风电塔筒检测项目中,实施测量工程师分级认证制度,配合AR辅助操作系统,使人为操作误差降低67%。同时开发基于区块链的检测数据存证平台,确保全生命周期质量追溯。
## 技术演进与发展建议随着数字孪生与量子传感技术的突破,建议重点发展三方面能力:其一,构建虚实融合的垂直度预测性检测系统,实现工艺参数动态调优;其二,推进ASTM与ISO标准体系融合,建立跨国界检测结果互认机制;其三,培育"测量+AI"复合型人才,应对工业4.0时代对精准制造的更高要求。据麦肯锡研究院预测,至2030年智能化几何量检测将释放超过800亿美元市场价值,垂直度检测技术作为基础支撑环节,必将迎来新的发展机遇。
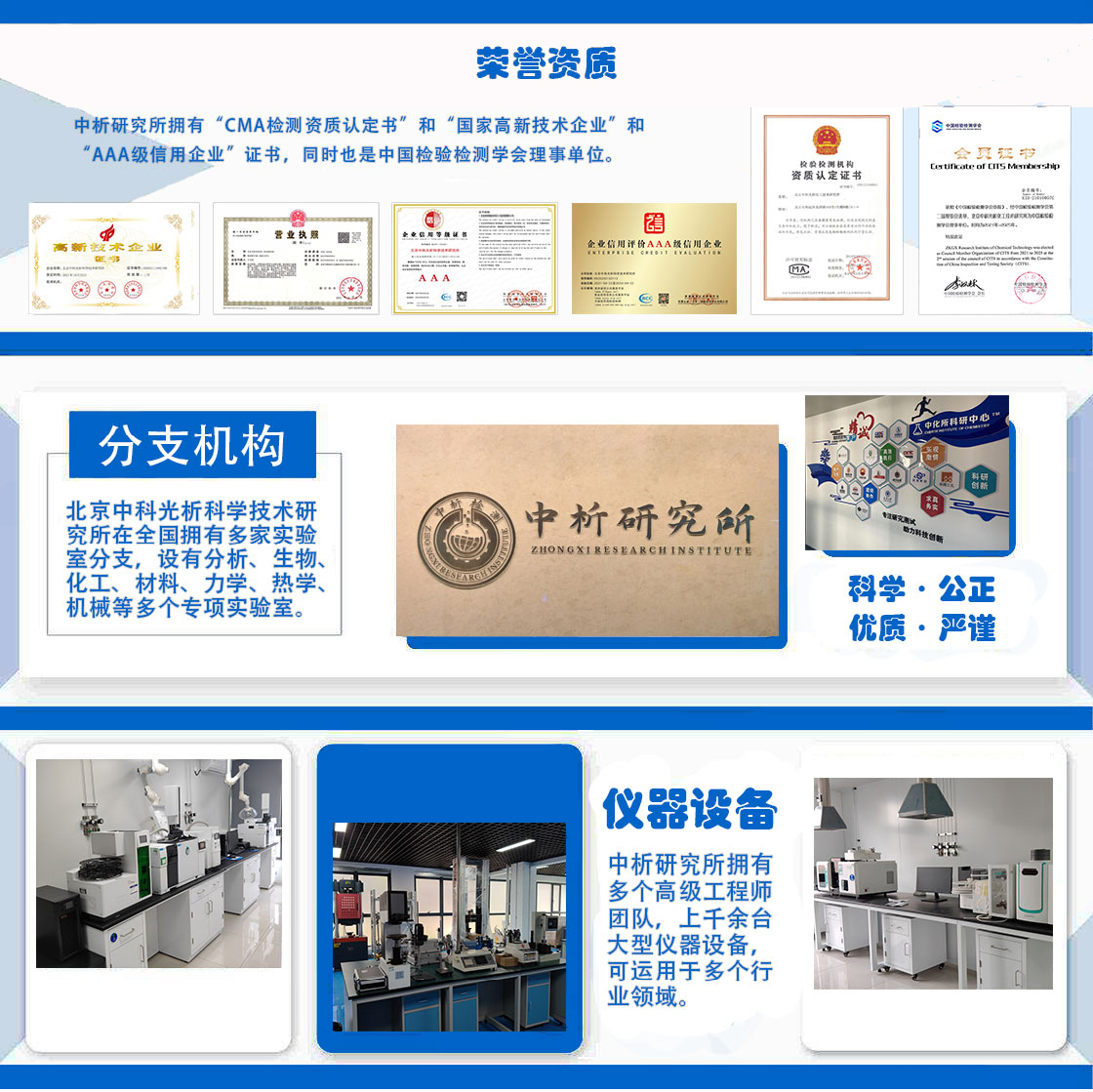
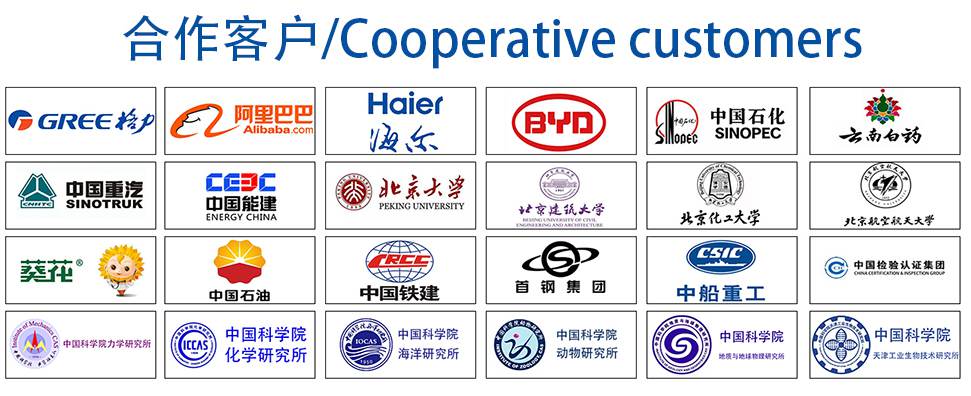