电动机综合保护装置检测的重要性与核心内容
电动机综合保护装置是保障工业电动机安全运行的核心设备,其集成了过载、短路、缺相、接地故障等多种保护功能。随着工业自动化程度的提升,电动机的运行环境日益复杂,保护装置的可靠性和精准性直接关系到设备寿命和生产安全。因此,定期开展电动机综合保护装置检测成为维护电力系统稳定性的必要环节。检测工作需覆盖电气性能、功能逻辑、环境适应性等多个维度,确保装置在异常工况下能够快速响应并切断故障。
核心检测项目与技术要求
1. 过载保护功能测试
通过模拟电机过载工况,验证保护装置的动作电流阈值和时间特性。需使用标准电流源输入1.2-1.5倍额定电流,记录装置从报警到切断电路的延迟时间,确保符合GB/T 14048.4标准要求的误差范围(±5%)。
2. 短路保护响应测试
利用大电流发生器瞬间施加6-10倍额定电流,检测装置在0.1秒内的脱扣能力。重点观察接触器分断速度及故障信号输出的同步性,避免因响应延迟导致设备损毁。
3. 缺相与不平衡保护验证
通过断开任一相电源或调整三相电流偏差至15%以上,验证装置是否能在设定时间内触发保护动作。需结合电压传感器数据与逻辑算法,确保对相位缺失的识别精度。
4. 绝缘电阻与耐压试验
使用兆欧表测量装置输入/输出端对地绝缘电阻(≥100MΩ),并施加2.5kV工频电压1分钟,检测是否存在击穿或漏电流超标现象。
5. 环境适应性测试
在高温(+55℃)、低温(-25℃)、湿热(95%RH)等极限条件下运行装置,评估其参数漂移和功能稳定性,确保复杂工业场景下的可靠性。
6. 通信与远程监控功能验证
针对带智能通信接口的装置,需测试Modbus、Profibus等协议的兼容性,并模拟网络中断场景检查故障数据存储与上传功能。
检测流程与结果判定
标准检测流程应包括预检参数录入→功能逐项测试→数据记录分析→生成检测报告四个阶段。所有项目需参照JB/T 10736-2021《电动机保护器》标准,对未达标项进行校准或更换部件,直至复检合格。检测报告需明确标注动作误差、响应时间等关键参数,为后续维护提供数据支持。
通过系统化的检测,可有效预防电动机因保护失效导致的绕组烧毁、轴承损坏等事故,延长设备使用寿命,同时降低非计划停机带来的经济损失。
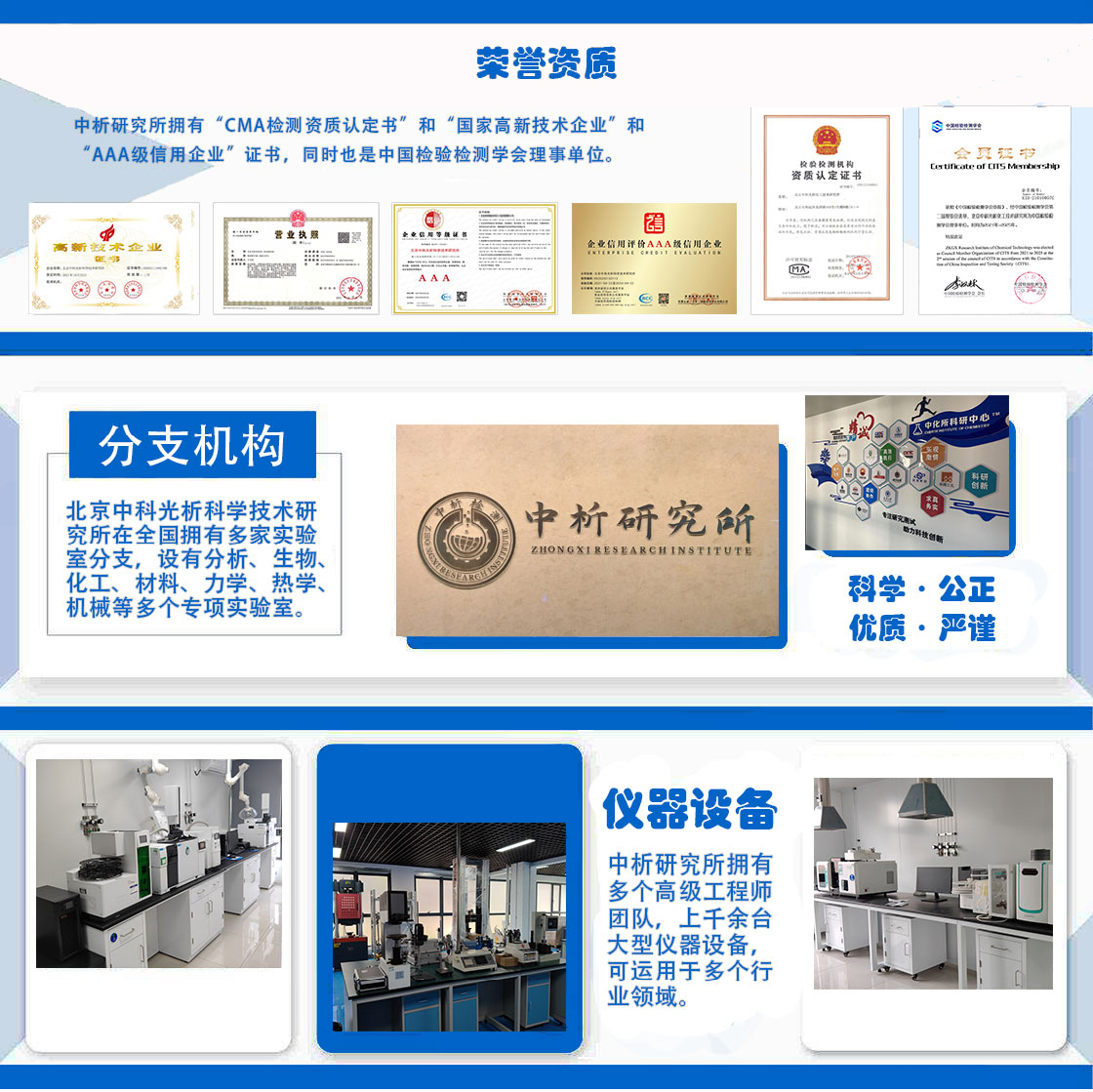
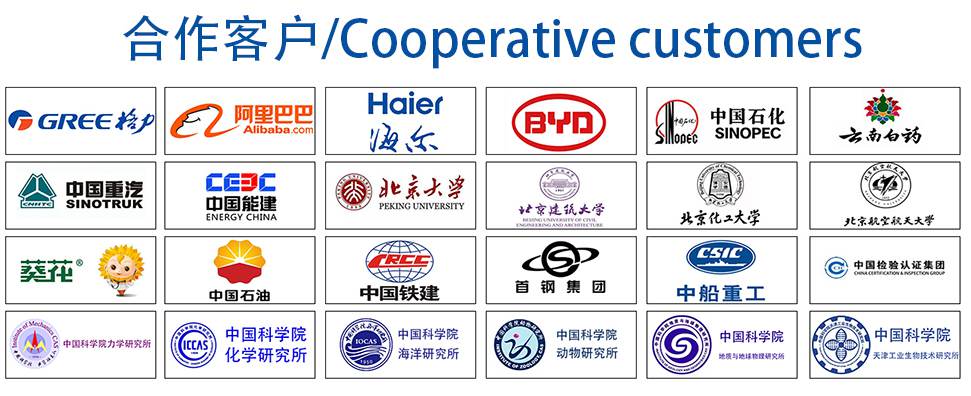