发条式定时器作为机械计时装置的核心部件,广泛应用于家用电器、工业设备及传统钟表领域。其工作原理依托发条弹簧蓄能驱动齿轮组传动,通过擒纵机构实现规律性间歇运动。随着使用时间的增长,发条疲劳、齿轮磨损、润滑失效等问题会直接影响定时精度与工作稳定性,因此建立系统化的检测体系对确保设备安全运行和延长使用寿命具有关键作用。
一、外观完整性检测
通过目视检查与测量工具评估外壳完整度,重点检测发条盒是否存在锈蚀、变形或裂纹现象,确认齿轮轴孔配合间隙是否在0.05-0.1mm设计范围内。同时验证刻度盘标记清晰度与指针装配垂直度,要求最大偏移角度不超过±2°。
二、发条力矩特性测试
使用扭矩测试仪在满弦状态下连续测量发条输出力矩曲线,要求有效工作行程内力矩波动值不超过标称值的15%。对新型NBR密封圈进行500次上弦循环测试,检测力矩衰减率应控制在5%以内。
三、走时精度校准
在标准温度(20±1℃)环境下,采用高精度时间校准仪进行48小时连续监测。一级精度定时器允许偏差为±30秒/24小时,工业级设备需达到±5分钟/周的标准要求。同步检测温度补偿装置在-10℃至50℃区间的走时稳定性。
四、齿轮传动系统评估
运用工业内窥镜观察三级减速齿轮组的啮合状态,检测齿形磨损量超过0.1mm需更换。采用频闪仪分析传动系统震动频率,确保主传动轴摆动幅度不大于0.08mm。对黄铜材质齿轮进行硬度测试,要求表面硬度达到HB80-100标准。
五、擒纵机构动作分析
使用高速摄影机(1000fps)捕捉擒纵叉与摆轮的相互作用过程,测量释放角度应稳定在42°±3°范围内。游丝刚度测试要求每圈弹性系数误差不超过2%,摆轮轴尖粗糙度需达到Ra0.2μm以上。
六、耐久性综合测试
在模拟工况下进行5000次完整工作循环试验,检测项目包含:发条疲劳强度下降率≤8%、齿轮传动效率保持率≥92%、触点开关动作次数误差<3%。试验后需重新进行力矩输出和走时精度验证。
通过建立包含6大类28个具体指标的检测体系,可全面评估发条式定时器的机械性能和可靠性指标。建议维护周期设定为:普通家电每3年检测一次,工业设备每年实施预防性检测,极端环境设备需缩短至半年检测周期。检测数据应建立数字化档案,为预测性维护提供趋势分析依据。
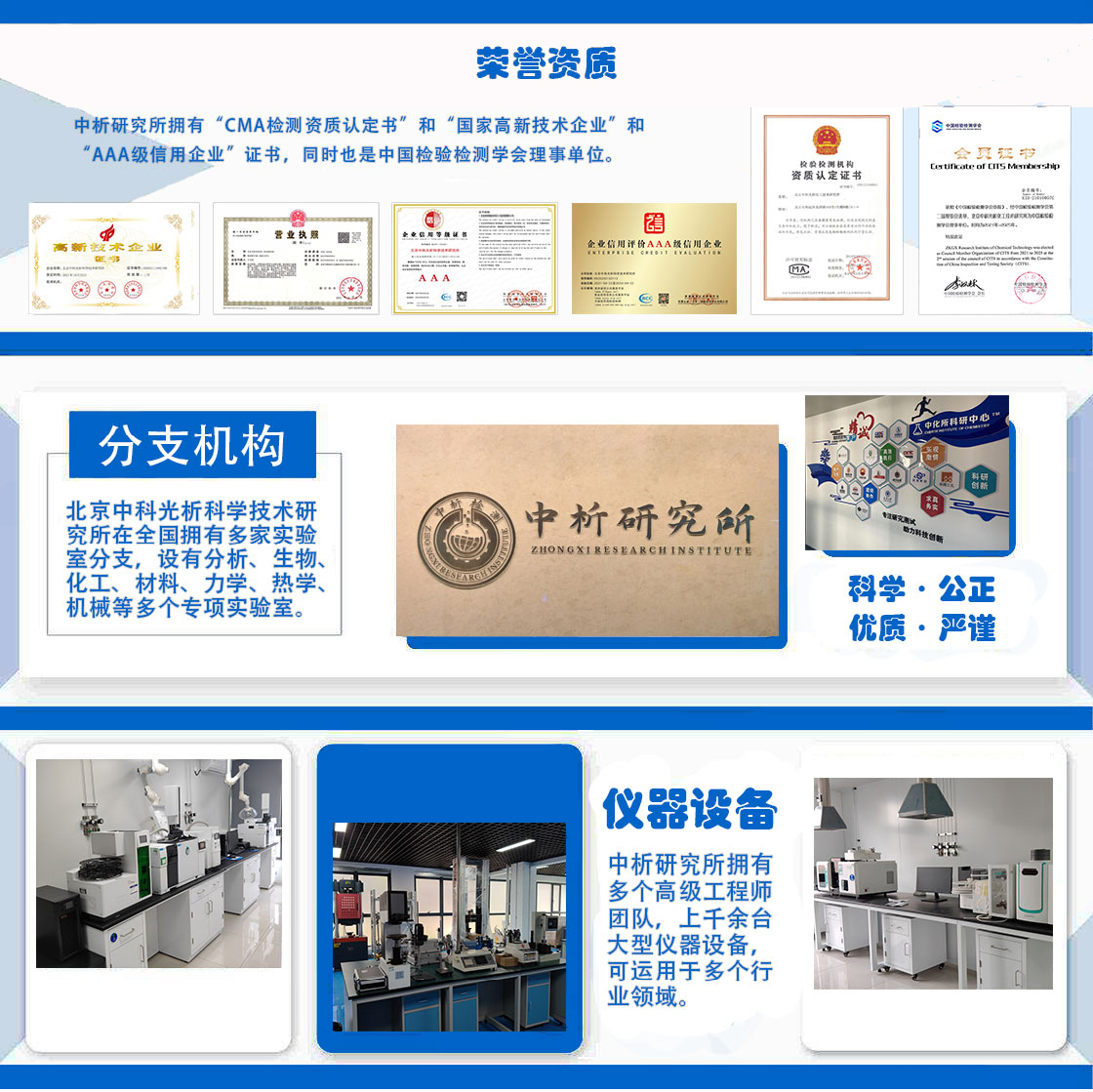
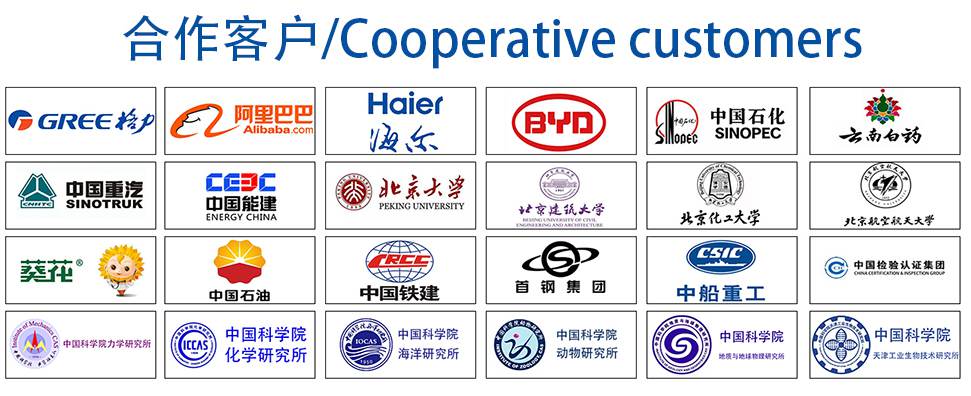