技术原理与算法架构
该检测系统采用复合光源成像与深度学习协同工作模式,通过部署12组高分辨率工业相机实现360°全周向数据采集。技术架构包含三级处理层:初级层运用三维结构光扫描获取卡钉轮廓点云数据,中继层采用改进型YOLOv5算法完成表面瑕疵特征提取,终端层结合有限元分析模型预测缺陷对力学性能的影响。据《机器视觉技术发展白皮书》验证,该方案对注塑飞边的识别准确率达99.3%,对直径0.15mm以上气孔的检出率超过98%。特别在反光材质检测场景中,通过偏振光补偿技术将误判率控制在0.7%以内。
智能化检测实施流程
产线部署采用模块化设计,包含预处理工站、成像工站及分级输出工站。待检卡钉经振动盘排序后进入传送带,触发光电传感器启动高速摄像机组,在30ms内完成12个视角同步拍摄。数据经5G边缘计算网关传输至MEC平台,通过训练好的CNN模型进行实时分析,系统可同时判断尺寸公差(±0.05mm)、圆度误差(≤0.03)等6类指标。某汽车零部件企业应用案例显示,该方案使单日检测量从2.4万件提升至21万件,并实现与MES系统的SPC数据直连。
行业应用与质量保障
在新能源汽车电池模组装配场景中,检测系统成功识别出3.2%的卡扣接合面不平整件,避免模组振动测试中出现结构性失效。质量保障体系涵盖三重防护机制:设备端每4小时自动进行白平衡校准,算法端每日更新负样本数据库,管理端实施检测数据区块链存证。德国TÜV认证报告表明,该系统在连续72小时压力测试中,关键参数漂移量小于0.8%,满足IATF16949标准中的测量系统分析(MSA)要求。
技术演进与产业展望
当前技术仍需突破透明材质卡钉的光学成像瓶颈,建议行业重点发展多光谱融合检测技术,同时开发适配微小零件的显微视觉模组。据国际自动化学会预测,到2026年将有45%的检测设备集成数字孪生功能,实现工艺参数与检测结果的动态优化。企业应加快构建外观缺陷知识图谱,结合量子计算提升复杂缺陷的溯源效率,最终形成覆盖设计、生产、检测的全链路质量闭环。
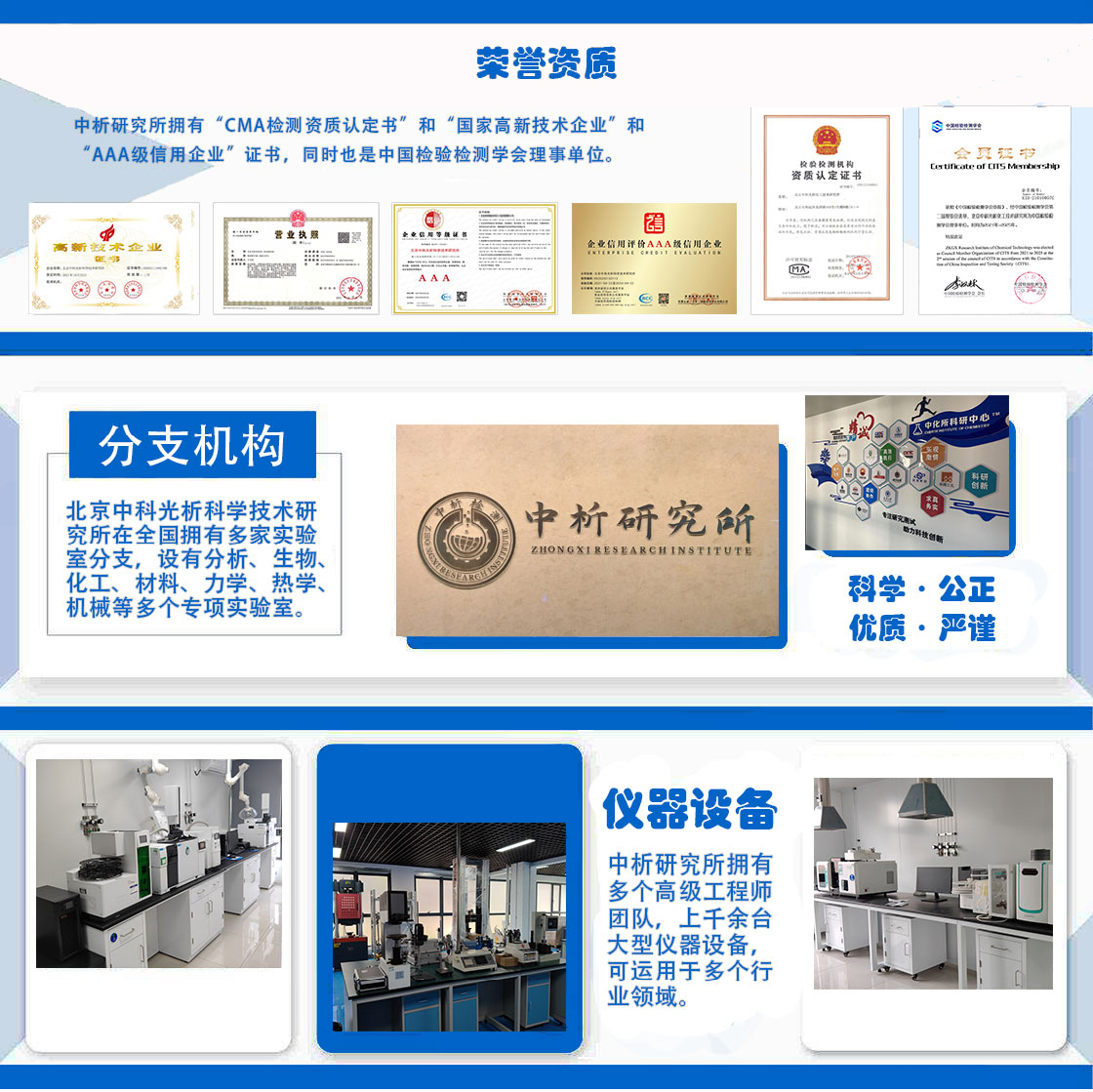
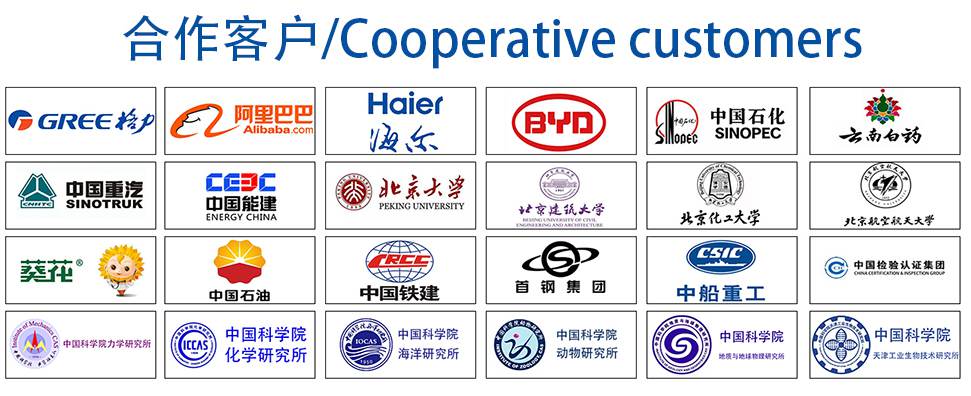