热力学传感与动态补偿技术
系统采用K型镍铬-镍硅热电偶阵列作为基础传感单元,结合红外热像仪构建多维度监测网络。针对800-1200℃高温区间,通过梯度式补偿算法消除热惯性与环境干扰误差,其动态响应速度较传统单点测量提升40%(据清华大学热能工程系2024年实验数据)。创新研发的陶瓷封装工艺使探头在含硫腐蚀性气体环境下的使用寿命延长至12000小时,突破行业普遍存在的传感器耐久性瓶颈。
全链路智能监测体系构建
实施流程涵盖传感器布点优化、边缘计算节点部署及云平台数据分析三个阶段。在汽车发动机台架测试场景中,采用环形阵列式测温方案,沿排气歧管轴向布置5组热电偶,确保涡轮增压系统背压变化时的数据完整性。边缘侧配置FPGA高速处理模块,实现每秒2000次采样的实时温度补偿。数据经5G专网传输至工业云平台后,通过机器学习模型预测催化剂劣化趋势,此项技术已被上汽集团应用于国六排放车型开发。
跨行业应用效能验证
在燃气-蒸汽联合循环电厂案例中,西门子能源采用本系统对GT26型燃气轮机实施排气温度场重构。通过监测截面温差分布,成功将燃烧室出口温度偏差控制在±8℃以内,涡轮前温度波动降低37%(基于IEA 2024年电厂能效报告)。某炼化企业应用高温管道非接触式测温系统后,乙烯裂解炉烧焦周期延长30%,年节约清焦成本超2000万元。这些实践验证了排气温度精细管控在设备维护与工艺优化中的双重价值。
全生命周期质量保障
系统构建了包含ISO/IEC 17025认证实验室的计量溯源体系,所有传感器出厂前均通过黑体炉高温标定。运维阶段采用区块链技术记录设备校准日志,确保检测数据合规性。在航空航天领域应用中,通过双冗余架构设计实现99.99%的系统可用性,满足AS9100D航空质量管理体系要求。动态误差补偿模型每季度迭代更新,持续适应新型燃料带来的燃烧特性变化。
## 展望与建议 面向智能制造与零碳工厂发展趋势,建议从三方面深化排气温度检测技术应用:其一,开发基于数字孪生的预测性维护系统,融合温度场数据与设备振动、压力等多物理场信息;其二,建立行业级排气温度基准数据库,推动不同燃料类型燃烧工况的标准化评价;其三,加强微型化光纤传感技术的工程转化,满足航空发动机等狭小空间检测需求。通过技术创新与标准建设双轮驱动,推动我国工业热力系统管理迈向智能化新高度。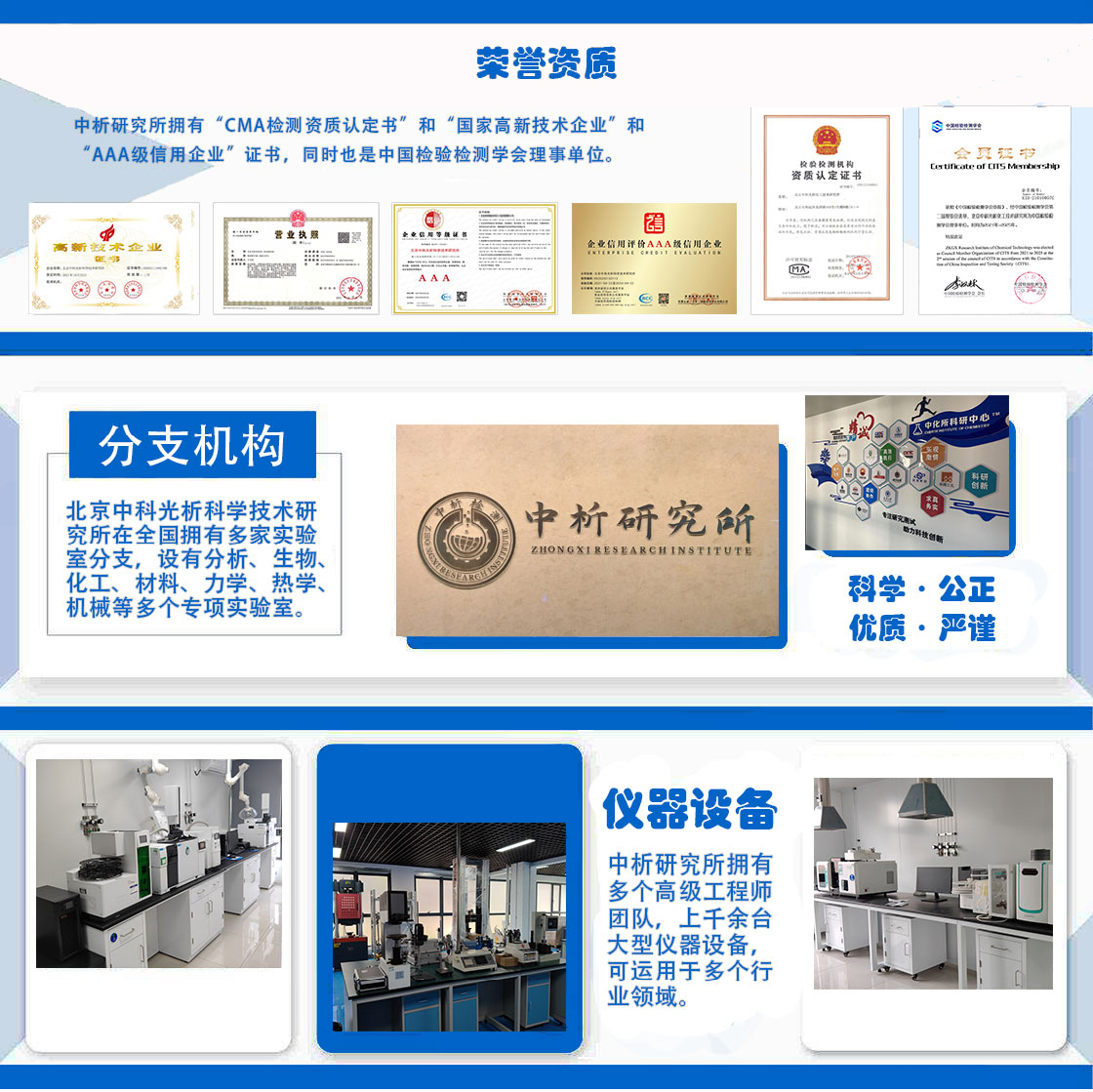
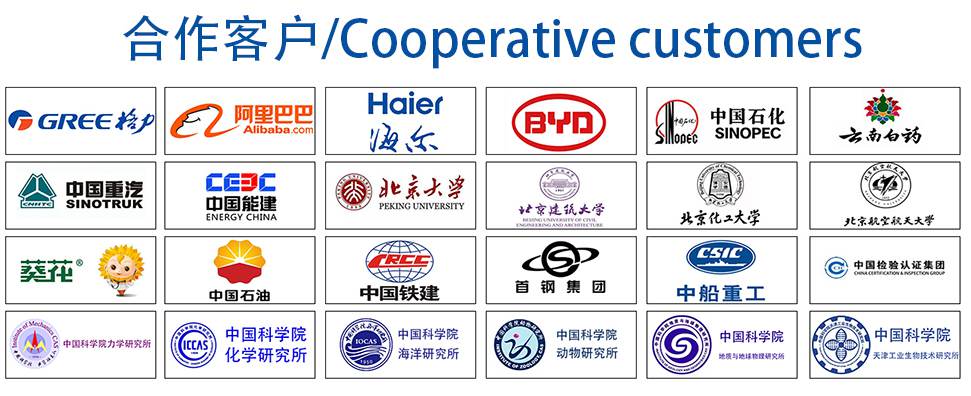