不含气液体灌装机检测的重要性
不含气液体灌装机广泛应用于饮料、药品、日化产品等行业的灌装生产中,其性能直接关系到产品灌装的精度、效率和安全性。随着行业对生产自动化和质量控制的严格要求,对灌装机进行系统性检测成为保障企业合规性和市场竞争力的关键环节。检测不仅能够验证设备是否符合国家标准(如GB/T 19001、GB 4806.1等)及行业规范,还能提前发现潜在故障,避免因设备误差导致的产品批次不合格、物料浪费或生产线停机等问题。
核心检测项目及方法
1. 灌装精度检测
通过称重法或体积测量法,验证灌装量的实际值与设定值的偏差是否在允许范围内(通常误差需≤±1%)。需在不同灌装速度下进行多次抽样测试,确保设备动态稳定性。
2. 密封性测试
采用压力衰减法或真空检漏法,检测灌装阀、管道及容器的密封性能,防止液体渗漏或外界污染。测试压力需依据设备设计参数设定,例如常压灌装机需模拟实际工况压力条件。
3. 材质安全性验证
对与液体直接接触的部件(如灌装头、输送管道)进行材质成分分析,确保符合食品级或药品级标准(如FDA、EC1935/2004)。重点检测重金属迁移量、塑化剂残留及耐腐蚀性。
4. 清洁度与卫生指标
通过微生物采样和ATP生物荧光检测,评估设备清洁后的残留物指标,避免交叉污染。需检查CIP(在线清洗系统)的覆盖率和清洗效果,特别是灌装嘴等复杂结构部位。
5. 控制系统稳定性测试
模拟异常工况(如供料中断、气压波动),检测PLC逻辑控制的响应速度和故障处理能力。需验证光电传感器、流量计等元件的信号准确性,以及触摸屏参数设置的可靠性。
6. 生产效率与能耗评估
记录单位时间灌装瓶数、空运转能耗及故障率,计算设备综合效率(OEE)。通过优化检测可发现机械结构磨损、传动系统效率下降等问题。
行业特殊检测要求
针对药品或高附加值液体产品,需增加环境适应性检测(如温湿度变化对灌装精度的影响)和批次追溯功能验证。部分出口设备还需通过CE认证中的机械指令(2006/42/EC)及低电压指令检测。
检测周期与实施建议
建议企业结合生产强度制定三级检测制度:日常点检(每班次)、预防性检测(每月)及全面校准(每年)。引入激光测距仪、高精度流量计等专业工具,并建立检测数据数字化管理平台,实现质量趋势预测与分析。
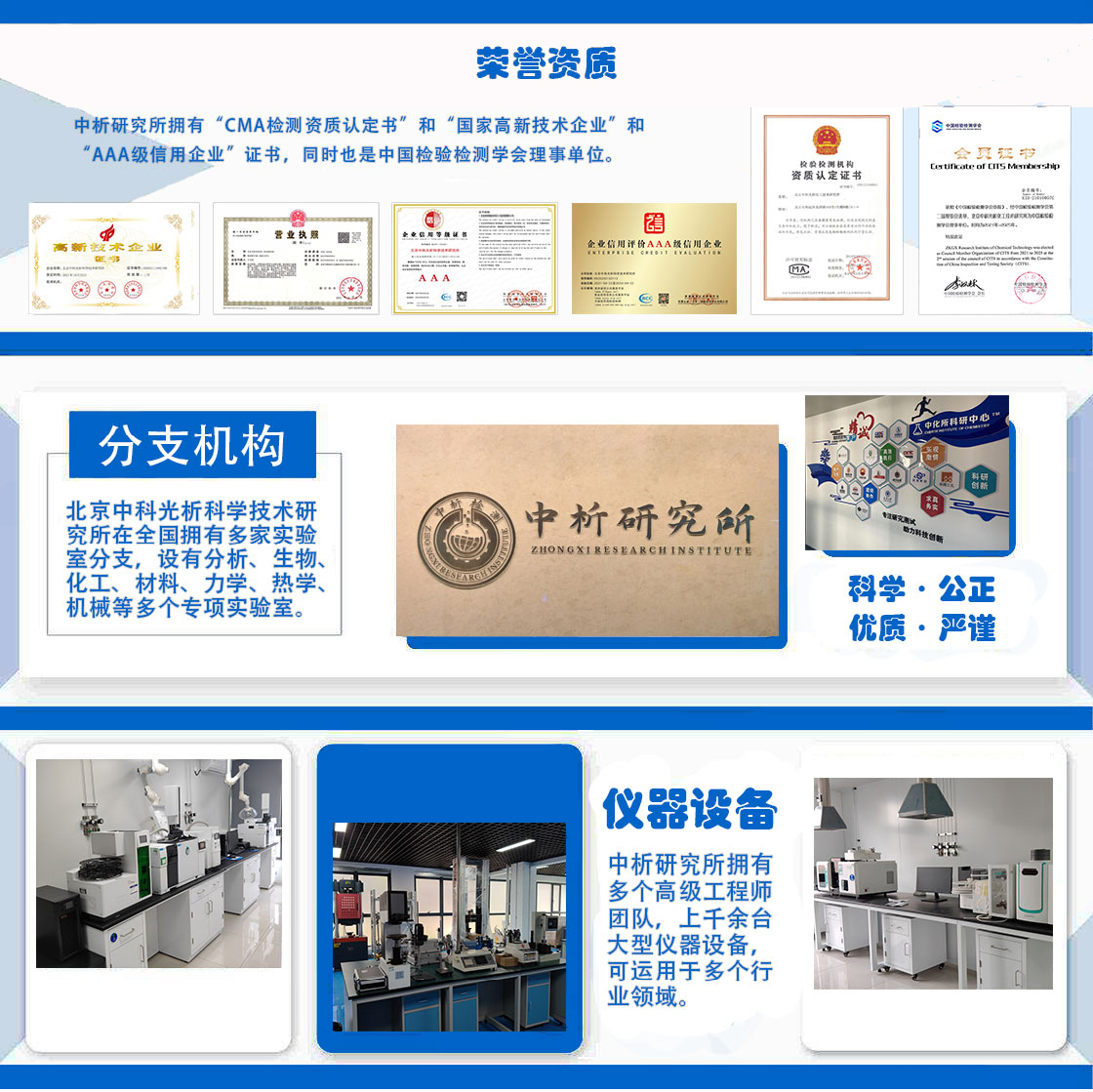
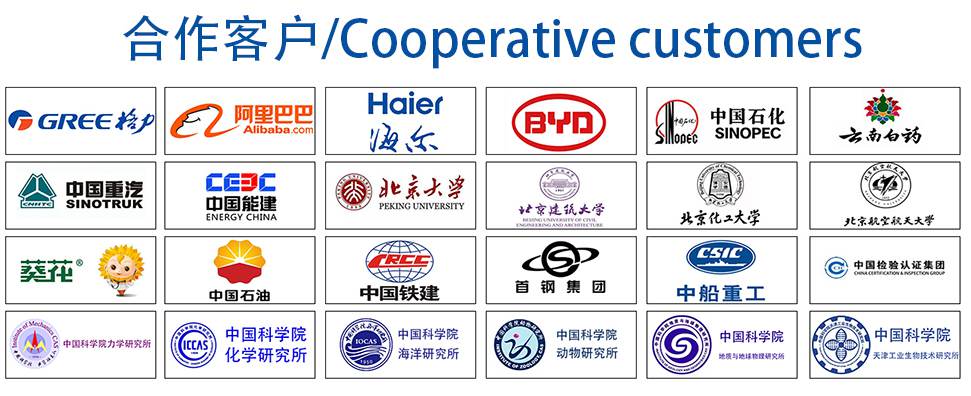