管线钢与压力容器钢检测的重要性
管线钢和压力容器钢作为工业领域的核心材料,广泛用于石油天然气输送、化工设备、核电站等关键场景。其性能直接影响设备的安全性、使用寿命及运行效率。随着能源需求增长和工程环境复杂化,对这两种钢材的检测要求日益严格。通过科学系统的检测手段,可有效评估材料的化学成分、力学性能、耐腐蚀性及缺陷情况,确保其符合API 5L、ASME SA-516、GB/T 713等行业标准,防范因材料失效引发的安全事故。
核心检测项目与技术要求
1. 化学成分分析
采用光谱仪(OES)、X射线荧光光谱仪(XRF)等设备检测C、Mn、Si、P、S等主元素含量,重点控制有害元素(如S、P)以提升抗氢致开裂能力。对于低温用钢需检测Ni、Mo等微合金元素,管线钢需关注Cu+Ni+Cr的耐腐蚀组合配比。
2. 力学性能测试
• 拉伸试验:测定屈服强度(YS)、抗拉强度(TS)、延伸率(EL),管线钢需满足DWTT(落锤撕裂试验)要求
• 冲击试验:-20℃/-40℃低温夏比冲击测试,评估材料韧性
• 硬度测试:布氏/维氏硬度检测防止氢脆风险
3. 无损检测技术
• 超声波检测(UT):识别内部分层、夹杂等缺陷,管线钢焊缝检测精度需达Φ2mm当量
• 射线检测(RT):用于压力容器对接焊缝质量评估
• 磁粉检测(MT)与渗透检测(PT):检测表面及近表面裂纹
4. 金相组织分析
通过显微观察评估晶粒度(ASTM E112)、带状组织、非金属夹杂物级别(ISO 4967),管线钢需控制贝氏体相变比例,压力容器钢需避免魏氏组织出现。
5. 腐蚀性能验证
• HIC/SSCC试验:模拟湿H2S环境检验抗氢致开裂能力
• 盐雾试验:评估表面涂层耐候性
• 高温高压腐蚀试验:压力容器钢需通过NACE TM0177标准测试
6. 几何尺寸与表面质量
采用激光测距仪、三维扫描仪检测钢板厚度公差(±0.1mm)、直线度(≤1.5mm/m),表面缺陷深度不得超过厚度5%。
特殊环境下的附加检测
针对北极管线、深海平台等极端工况,需增加:
• -60℃超低温冲击试验
• 厚板Z向性能测试(断面收缩率≥35%)
• CTOD试验(裂纹尖端张开位移)评估止裂特性
检测标准与认证体系
检测过程需严格遵循API SPEC 5L/ASME Section VIII/GB 150.4等标准,通过ISO/IEC 17025认证实验室出具 /CMA检测报告。对于出口材料需同步满足PED 2014/68/EU、EN 10219等国际规范要求。
结语
随着智能化检测技术的发展,数字射线成像(DR)、相控阵超声波(PAUT)等新技术正逐步应用于管线钢和压力容器钢的检测领域。建立从原材料到成品的全生命周期质量监控体系,是保障能源装备安全运行的关键。企业应选择具备专业资质和工程经验的检测机构,通过数据化管理系统实现检测结果的可追溯性。
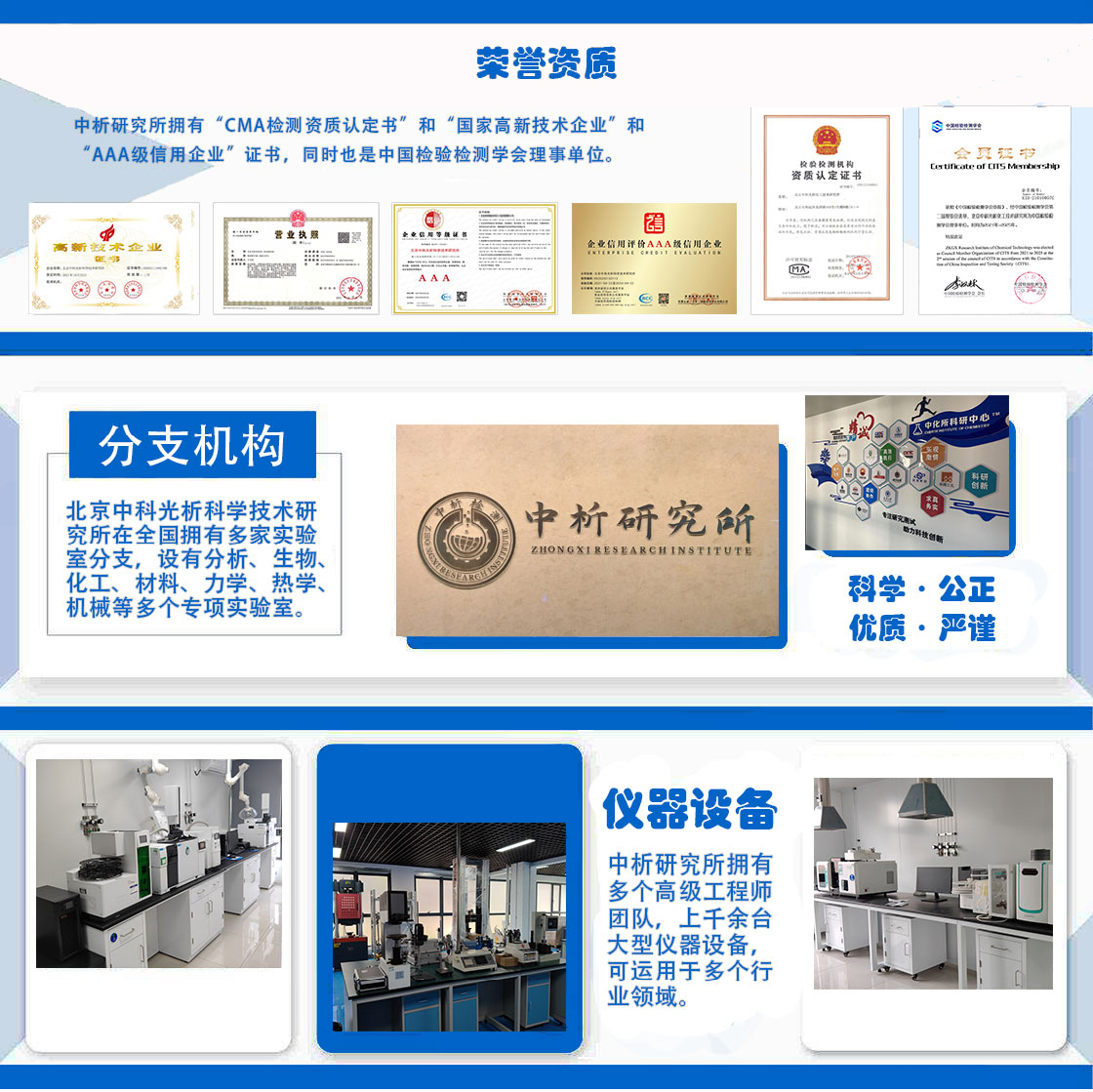
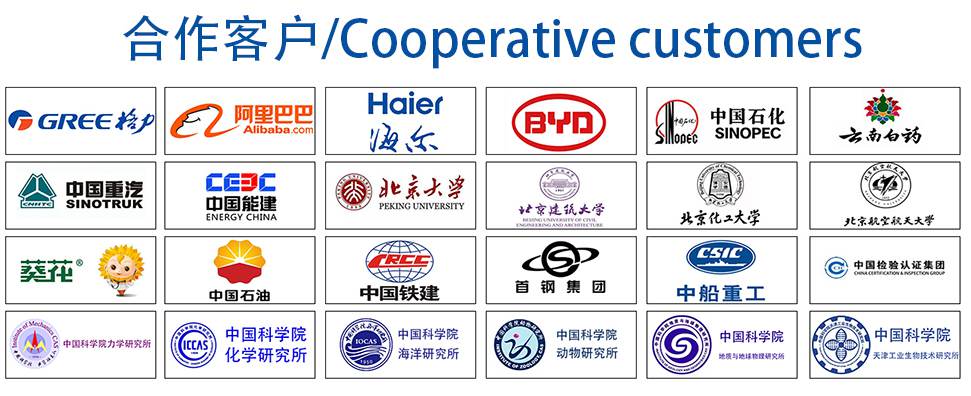