分纸机检测:关键项目与操作要点解析
分纸机作为造纸、印刷、包装行业的核心设备,其运行精度和稳定性直接关系生产效率和产品质量。随着工业自动化水平提升,分纸机的检测工作已成为设备维护中不可忽视的环节。通过对分纸机系统的全面检测,可有效预防设备故障、延长使用寿命并保障操作安全。检测过程中需重点关注机械传动、控制系统、安全装置等核心模块,结合动态测试与静态检查,形成完整的设备健康评估体系。
一、分纸精度检测
分纸精度是分纸机性能的核心指标,需通过专业仪器测量实际分切尺寸与设定值的偏差。检测时需包含纵向分切精度(±0.1mm内为合格)和横向对齐度(偏差不超过0.3mm)。测试应覆盖全幅宽范围,特别关注设备两端的切割一致性。对于带有视觉定位系统的机型,还需校准图像传感器的识别精度和响应速度。
二、传动系统振动检测
使用振动分析仪对主驱动轴、齿轮箱、轴承等关键部位进行多点检测。正常运行时各测点的振动速度应≤4.5mm/s,加速度值不超过7m/s²。需特别注意高频振动(>1000Hz)可能预示轴承缺陷,低频振动(<200Hz)则可能反映联轴器对中问题。检测时应分别在空载、半载、满载三种工况下采集数据。
三、刀片组件状态检测
包括上刀与底刀的配合间隙(建议0.03-0.05mm)、刀刃磨损量(单边磨损>0.2mm需更换)、刀轴径向跳动(≤0.02mm)。使用激光对刀仪检测刀片平行度,全幅宽范围内误差应控制在0.05mm以内。同时需检查液压或气动加压系统的压力稳定性,波动幅度不应超过设定值的±5%。
四、安全防护装置测试
完整的安全检测应包含:急停按钮响应时间(≤0.5秒)、光电保护装置的探测灵敏度(最小检测物直径≤40mm)、机械式防护罩的连锁功能验证。对双通道安全控制系统需进行冗余测试,模拟单通道故障时系统能否维持有效保护。此外还需检查各安全标识的完整性和可见性。
五、电气控制系统检测
使用万用表、示波器等工具检测PLC各模块工作电压(波动范围±10%)、I/O信号响应时间(<50ms)。重点检查变频器输出波形畸变率(<5%)、电机绝缘电阻(≥5MΩ)。对触摸屏操作界面进行功能验证,测试参数设置、报警记录、配方存储等功能的稳定性。
六、润滑系统效能评估
检测自动润滑装置的油路通畅性、注油量精度(误差±10%内)和周期设定合理性。使用油质分析仪检测导轨油黏度(40℃时46-68cSt)、金属颗粒含量(>15μm颗粒数≤2000/mL)。对采用集中润滑的系统,需验证各润滑点压力均衡性(压差<0.2MPa)。
专业的检测周期建议每季度执行基础项目检测,年度进行深度检测。检测数据应建立电子档案,通过趋势分析预判设备状态。企业可结合生产强度适当调整检测频率,但关键安全项目必须保证每月查验。规范的检测流程不仅能降低设备故障率,还能提升分切产品的合格率3-5个百分点,是现代化生产管理的重要实践。
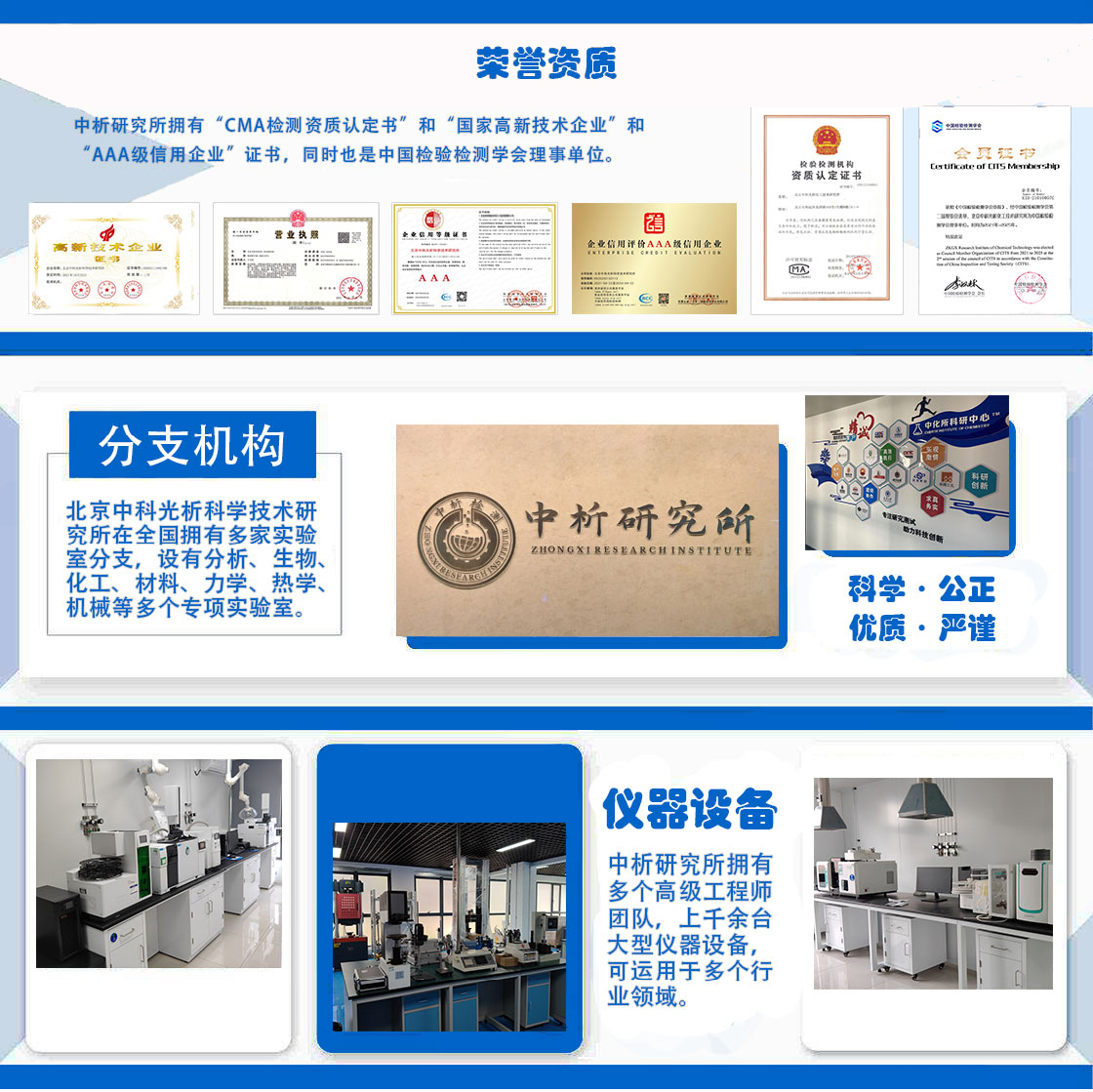
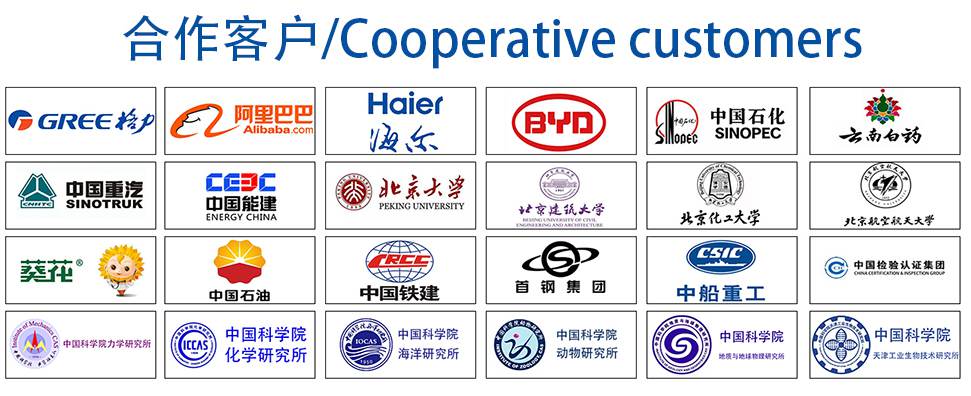