冰箱用高清洁度铜管检测的关键项目与技术要求
在冰箱制冷系统生产中,铜管作为核心传热组件,其清洁度直接关系到制冷效率、系统寿命及安全性。随着消费者对家电品质要求的提升,高清洁度铜管的检测已成为冰箱制造企业的核心质控环节。铜管表面残留的油脂、氧化物或颗粒污染物可能导致制冷剂泄漏、压缩机磨损甚至系统堵塞,因此需通过系统化的检测项目确保铜管满足严苛的清洁度标准。
核心检测项目与实施方法
1. 表面污染物检测
采用目视检查与仪器分析相结合的方式,通过高倍显微镜观察内壁划痕及附着物分布,配合能谱仪(EDS)鉴定污染物成分(如碳氢化合物、硫化物等)。部分企业引入工业内窥镜对弯曲部位进行360°全方位检测,确保隐蔽区域无残留。
2. 清洁度等级验证
依据ISO 16232标准,通过液压冲洗法收集铜管内部颗粒物,使用精密天平称重后按长度换算单位面积残留量。高端实验室配置激光粒度分析仪,可精确统计0.5-200μm区间颗粒数量分布,满足汽车级VDA19标准的延伸要求。
专项性能测试体系
3. 气密性验证测试
采用氦质谱检漏法将铜管加压至2.5倍工作压力(通常达5MPa以上),通过分子级检测识别微小泄漏点。同时开展热循环试验,模拟-30℃至120℃极端温度交替变化,验证铜管抗疲劳性能。
4. 耐腐蚀性能评估
执行GB/T 10125盐雾试验,将样品置于5%NaCl溶液形成的盐雾环境中连续测试240小时。齐全的电化学工作站可实时监测腐蚀电流密度,结合金相分析判断晶间腐蚀倾向,确保10年使用寿命要求。
全流程质量管控方案
现代化检测体系涵盖从原材料到成品的全过程:
- 原料端:光谱分析仪确保C1220铜材纯度≥99.9%,铅、铋等杂质含量≤0.001%
- 制程端:在线涡流探伤仪实现0.1mm级缺陷实时监测
- 出货端:建立批次追溯数据库,每根铜管附带包含128项参数的电子质量档案
通过构建多维度的检测矩阵,冰箱制造商可将铜管清洁度不良率控制在≤5ppm,为提升整机能效等级(可达新国标1级)提供关键保障。随着AI视觉检测与物联网技术的深度应用,铜管检测正朝着智能化、高精度方向持续升级。
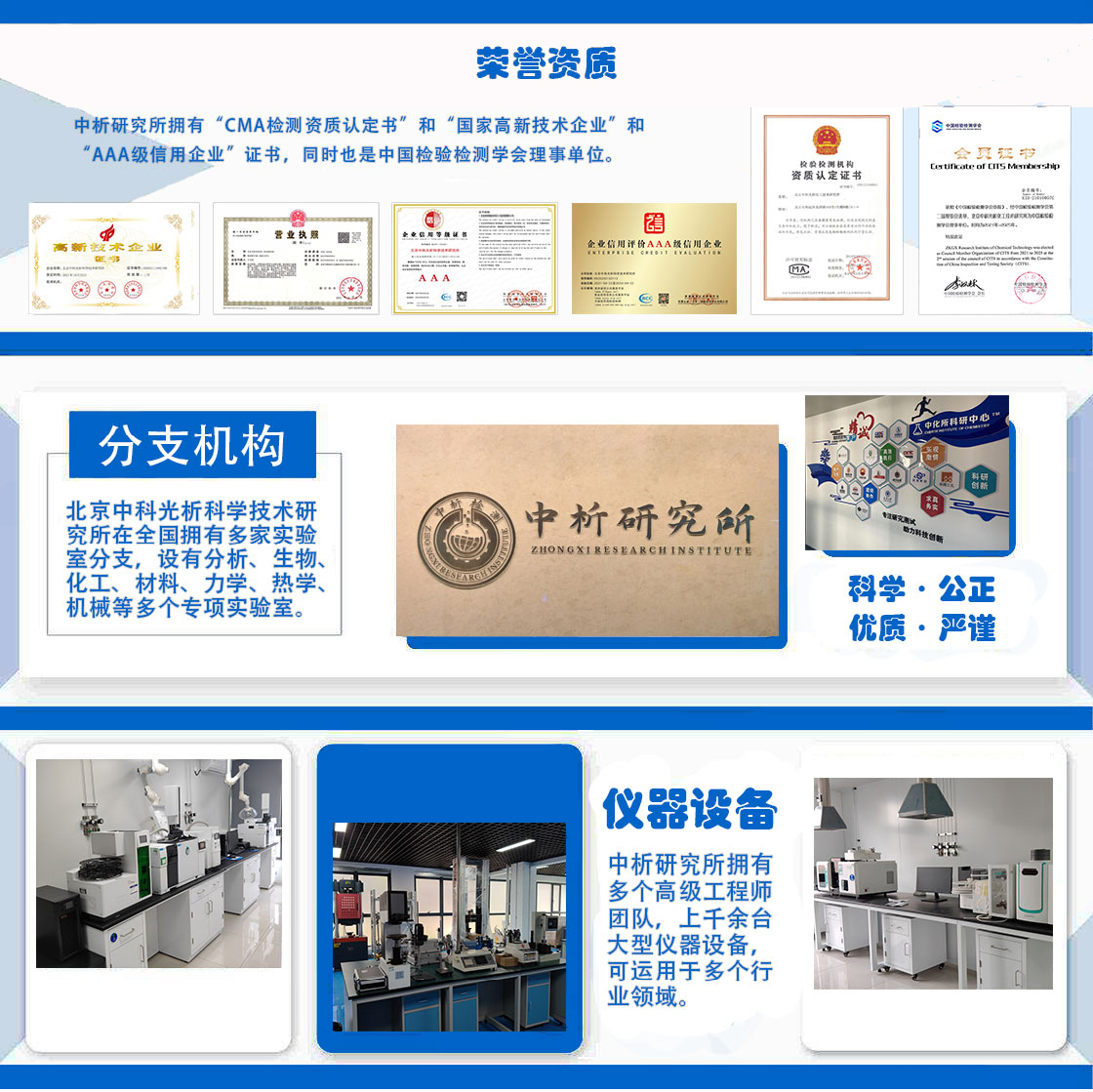
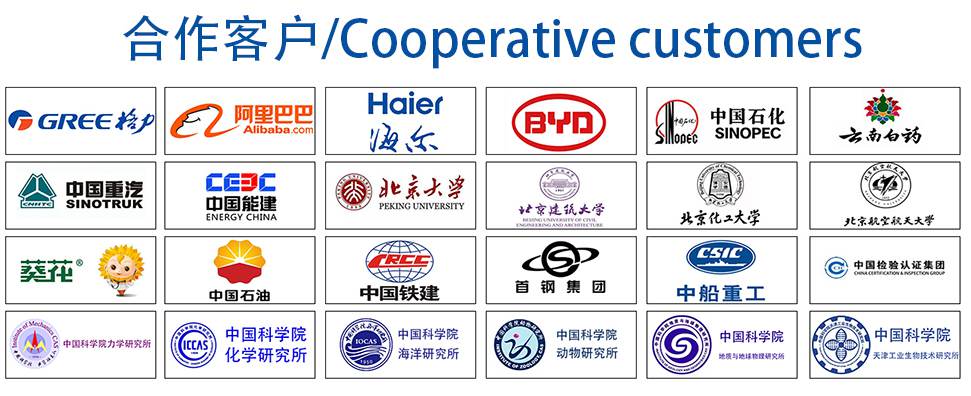