抗酸、碱液性能检测的重要性与核心内容
抗酸、碱液性能检测是评估材料或产品在酸、碱化学环境中耐受能力的关键测试项目,尤其广泛应用于化工设备、管道、防护材料、涂料、塑料及金属制品等领域。随着工业技术的发展,材料在极端化学环境下的稳定性需求日益提高,此类检测不仅能够验证产品的使用寿命和安全性,还能为优化生产工艺提供数据支持。在检测过程中,需严格遵循国家标准(如GB/T 1763-2022)或行业规范,通过模拟实际工况下的酸碱腐蚀条件,综合评估材料的抗渗透性、耐蚀性与机械性能变化。
检测项目与关键指标
抗酸、碱液性能检测主要包括以下核心项目:
1. 静态浸泡试验:将试样浸泡于不同浓度(如10% HCl、30% NaOH等)的酸、碱溶液中,记录一定时间(如24小时、7天)后的质量变化、表面腐蚀情况及力学性能损失。此项目用于模拟长期接触酸碱介质的环境。
2. 动态冲刷试验:通过循环流动的酸、碱液对材料表面进行冲刷,评估其在高流速环境下的耐磨损与化学腐蚀复合作用下的性能,适用于管道、阀门等流体传输设备。
3. 耐温变性能测试:结合温度变化(如从25℃升至80℃),观察材料在热酸、热碱环境下的膨胀、龟裂或分层现象,验证其在高温工况下的稳定性。
4. 微观结构分析:使用扫描电镜(SEM)、能谱仪(EDS)等设备分析腐蚀后材料的微观形貌及元素分布,揭示腐蚀机理及防护涂层的失效原因。
检测标准与判定依据
检测依据通常包括国际标准(ISO 2812-4)、国家标准(GB/T 11547)及行业技术规范。以金属材料为例,判定标准可能包括:质量损失率≤1.5%(酸液)、≤2.0%(碱液);表面无起泡、剥落或明显变色;抗拉强度损失率小于15%等。非金属材料(如橡胶密封件)则需额外关注硬度变化(邵氏A型±5°以内)和体积膨胀率(≤10%)。
实际应用与案例分析
在化工储罐内衬材料的选型中,某EPDM橡胶通过抗98%硫酸(40℃×720h)测试后,质量损失仅0.8%,远优于氯丁橡胶的3.2%,成功应用于强酸存储场景。此类检测数据可显著降低设备维护成本,避免因材料失效导致的泄露事故。
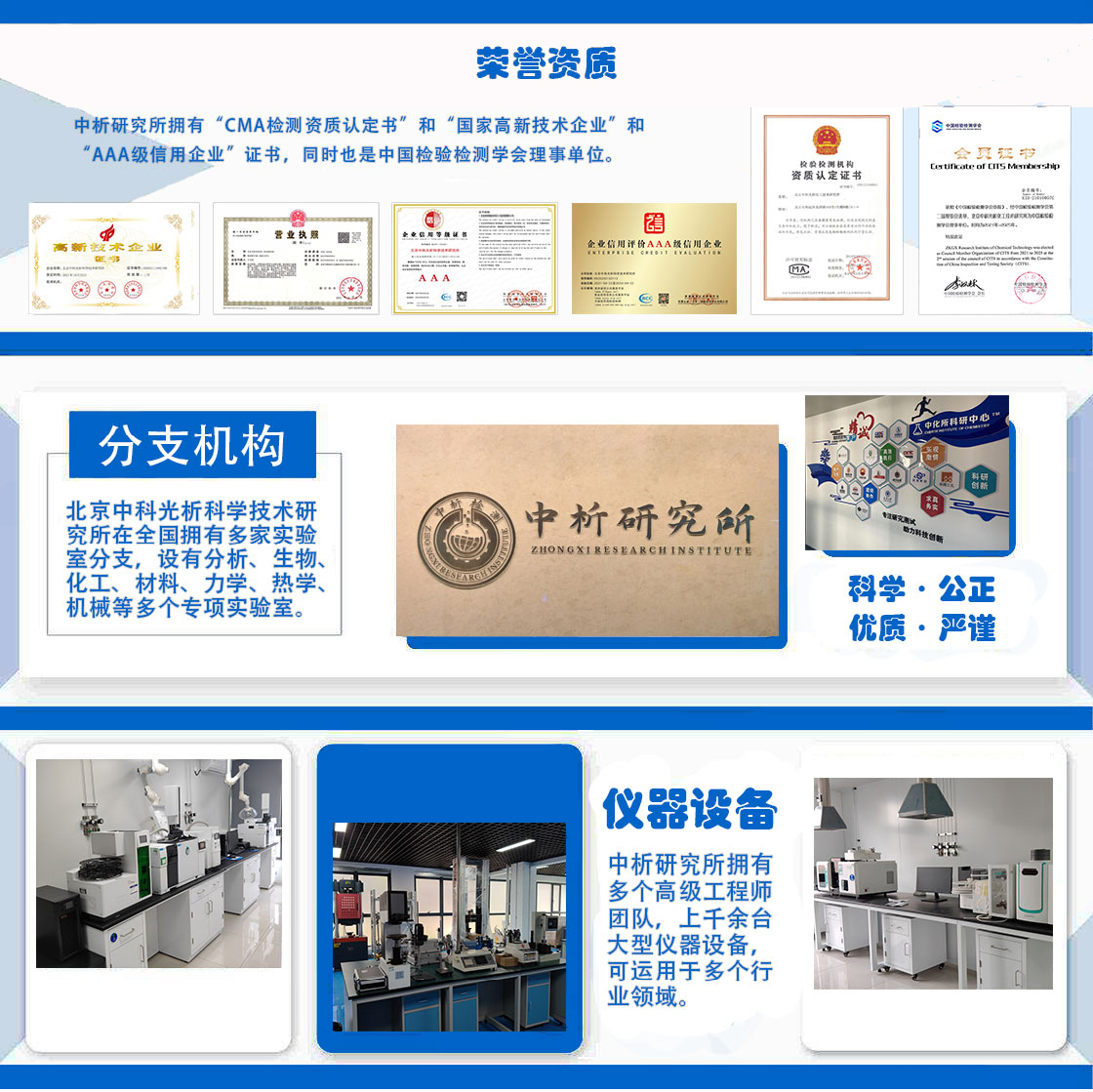
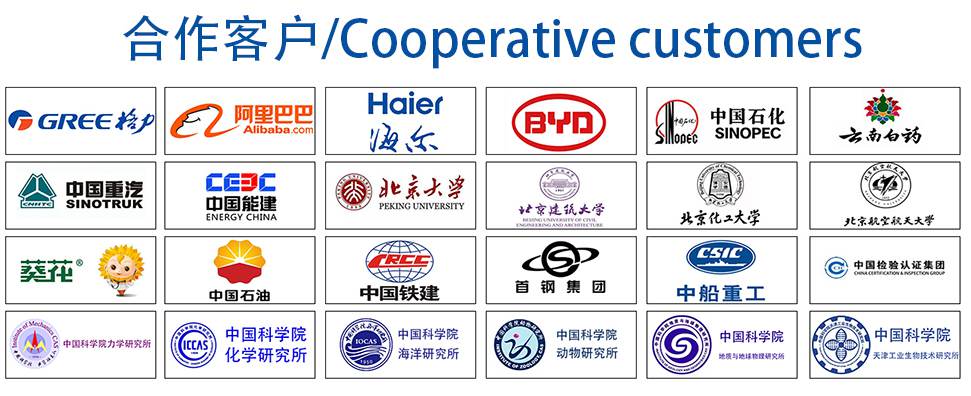