三轮汽车驱动桥检测的重要性与核心内容
作为三轮汽车动力传递的核心部件,驱动桥的可靠性直接关系到车辆的动力性能、行驶安全及使用寿命。驱动桥检测通过系统性评估其机械强度、传动效率及磨损状态,可有效预防因零部件失效导致的故障风险。对于使用频繁、载重较大的三轮汽车而言,定期开展驱动桥专项检测不仅是行业规范要求,更是延长车辆使用寿命、降低维修成本的重要保障措施。
关键检测项目详解
1. 外观与结构完整性检测
采用目视检查与测量工具结合的方式,重点核查桥壳是否有裂纹变形、油封渗漏痕迹,检查半轴套管定位销是否松动,同时测量桥体总成与车架的装配尺寸偏差,确保其在公差允许范围内。
2. 齿轮传动系统检测
使用专业间隙规测量主减速器齿轮啮合间隙,标准值通常控制在0.15-0.25mm之间。通过磁粉探伤检测齿轮表面微裂纹,借助振动分析仪评估齿轮副的传动平稳性,异常振动值需控制在ISO10816标准三级以下。
3. 轴承与润滑系统检测
使用红外测温仪监测轴承工作温度,连续运转下温度不应超过85℃。解体检查滚道磨损情况时,游隙增加值不得超过原设计值的20%。同步检测润滑油金属碎屑含量,采用光谱分析判断异常磨损金属成分。
4. 动态负载性能测试
在专用试验台上模拟不同工况,包括0-30km/h加速、20%坡道爬坡等场景,记录驱动桥扭矩传递曲线。要求最大负载下传动效率不低于92%,且无异常噪音产生,半轴断裂扭矩需达到设计值的1.5倍以上。
5. 材料疲劳强度检测
对桥壳本体取样进行金相分析,重点检测球墨铸铁件的石墨形态与基体组织。通过疲劳试验机加载交变载荷,验证桥体在10^6次循环载荷下的结构完整性,裂纹萌生周期应符合QC/T533行业标准要求。
智能化检测技术应用
新型检测体系引入三维激光扫描进行桥体形变分析,运用声发射技术实时捕捉内部损伤信号。大数据平台可比对历史检测数据,实现磨损趋势预测,使传统定期检测升级为预防性维护模式。
通过上述多维度的检测流程,能够全面掌握驱动桥技术状态,为维修决策提供精准依据。建议每行驶5000公里或半年实施一次系统检测,重点车辆应缩短至3000公里检测周期,确保三轮汽车始终处于最佳运行状态。
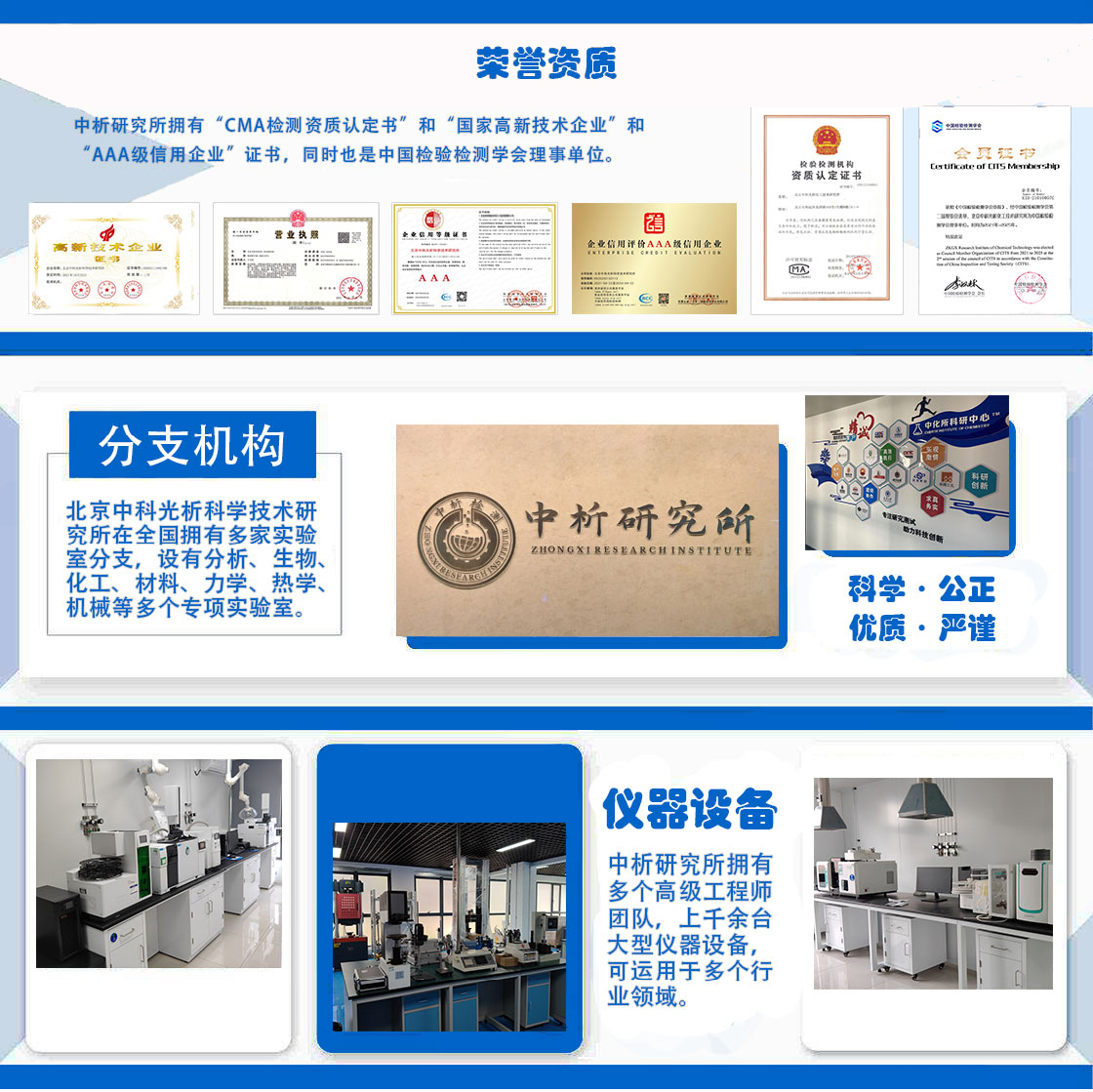
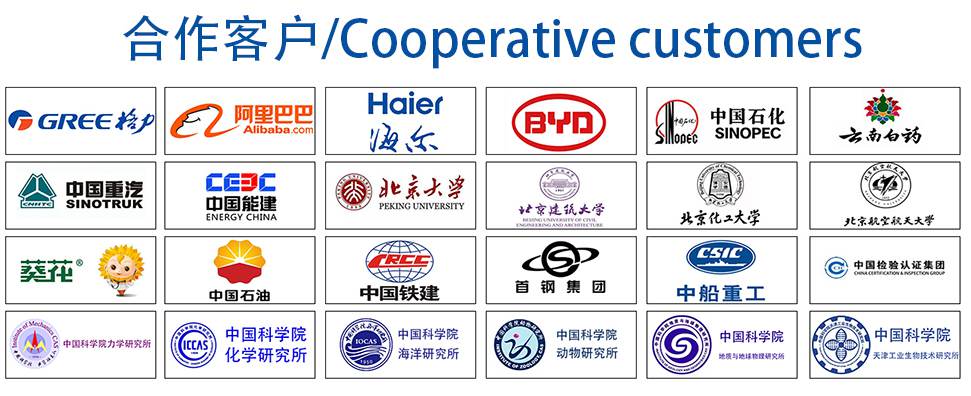