随着燃气汽车在公共交通、物流运输等领域的广泛应用,燃气系统作为车辆的核心动力单元,其安全性及稳定性直接关系到行车安全与使用成本。燃气系统检测不仅是车辆年检的强制项目,更是日常维护中预防燃气泄漏、爆燃等重大事故的关键技术手段。通过系统化的检测流程,可及时发现储气罐老化、管路磨损、阀门失效等隐患,确保燃气供给系统在高压、高温工况下的可靠运行。
一、储气装置完整性检测
重点检查CNG/LNG储气罐的出厂合格标志、压力容器定期检验报告及表面腐蚀情况。使用超声波测厚仪测量罐体壁厚,对比原始技术参数判断金属疲劳程度。同时验证安全阀、爆破片等超压保护装置的动作压力值是否符合GB 24162-2020《汽车用压缩天然气金属内胆纤维环缠绕气瓶定期检验与评定》标准要求。
二、燃气输送管路密封性检测
采用0.3MPa氮气进行保压试验,在管路各连接处喷涂检漏液,观察是否产生连续气泡。特别关注橡胶软管的老化裂纹、金属硬管的应力集中部位,使用红外热像仪检测管路温度异常区域。管路固定卡扣的间距应不大于600mm,避免车辆颠簸导致摩擦破损。
三、燃气控制阀件功能性测试
通过专用诊断设备检测电磁阀启闭响应时间,正常值应小于50ms。检查减压调节器输出压力稳定性,在怠速与急加速工况下,压力波动范围不得超过标称值的±5%。手动紧急切断阀需进行10次以上开闭测试,确保其机械传动机构灵活可靠。
四、燃气泄漏浓度监测
在发动机舱、储气罐舱等密闭空间布置甲烷检测探头,使用符合JJG 693-2011标准的可燃气体检测仪进行多点采样。泄漏浓度超过LFL(爆炸下限)的20%时应立即触发声光报警,系统自动切断燃气供应并启动强制通风装置。
五、燃气喷射系统精准度校准
使用示波器检测燃气喷嘴的开启脉宽与ECU指令的同步性,偏差不应超过0.2ms。通过燃气流量计测量各缸供气量差异,最大偏差需控制在3%以内。定期清洁燃气滤清器,确保燃气中颗粒物含量低于5μm,防止精密阀件卡滞。
六、电控系统故障诊断
连接OBD-II诊断接口读取故障代码,重点监测燃气压力传感器、氧传感器、爆震传感器等关键信号。使用万用表测量线束电阻值,排除线路虚接、短路问题。更新ECU控制软件至最新版本,优化空燃比闭环控制算法。
七、系统整体气密性验证
在完成单项检测后,需对燃气系统进行整体保压测试。将系统加压至工作压力的1.5倍,保持30分钟后压降不得超过初始值的2%。采用氦质谱检漏仪可精准定位微漏点,检测灵敏度可达1×10⁻⁷ Pa·m³/s。
八、排放污染物专项检测
使用五气分析仪测量尾气中NOx、CO、HC等排放物浓度,对比GB 18285-2018双怠速法限值。燃气发动机的λ值(过量空气系数)应稳定在0.98-1.02范围内,异常波动可能反映混合器故障或氧传感器失效。
九、安全防护装置有效性核查
验证碰撞传感器是否能在30ms内触发燃气切断阀,检查储气罐防爆隔离舱的泄压通道畅通性。车载灭火器需满足GB 4351.1-2005标准,压力指针处于绿色区域,且定期进行功能性检查。
十、定期维护周期管理
建立燃气系统检测电子档案,依据行驶里程设置三级维护周期:每5000km进行常规检漏,20000km更换过滤器组件,40000km开展全面压力测试。冬季需特别关注减压器加热装置工况,防止燃气结冰导致供气中断。
专业的燃气系统检测需由持有TSG Z8002《特种设备检验人员考核规则》认证的机构实施。建议车主在加装燃气系统时选择具有GB/T 19240《机动车用液化石油气加注口》认证的合规配件,并保留完整的检测记录作为车辆保险理赔的重要凭证。
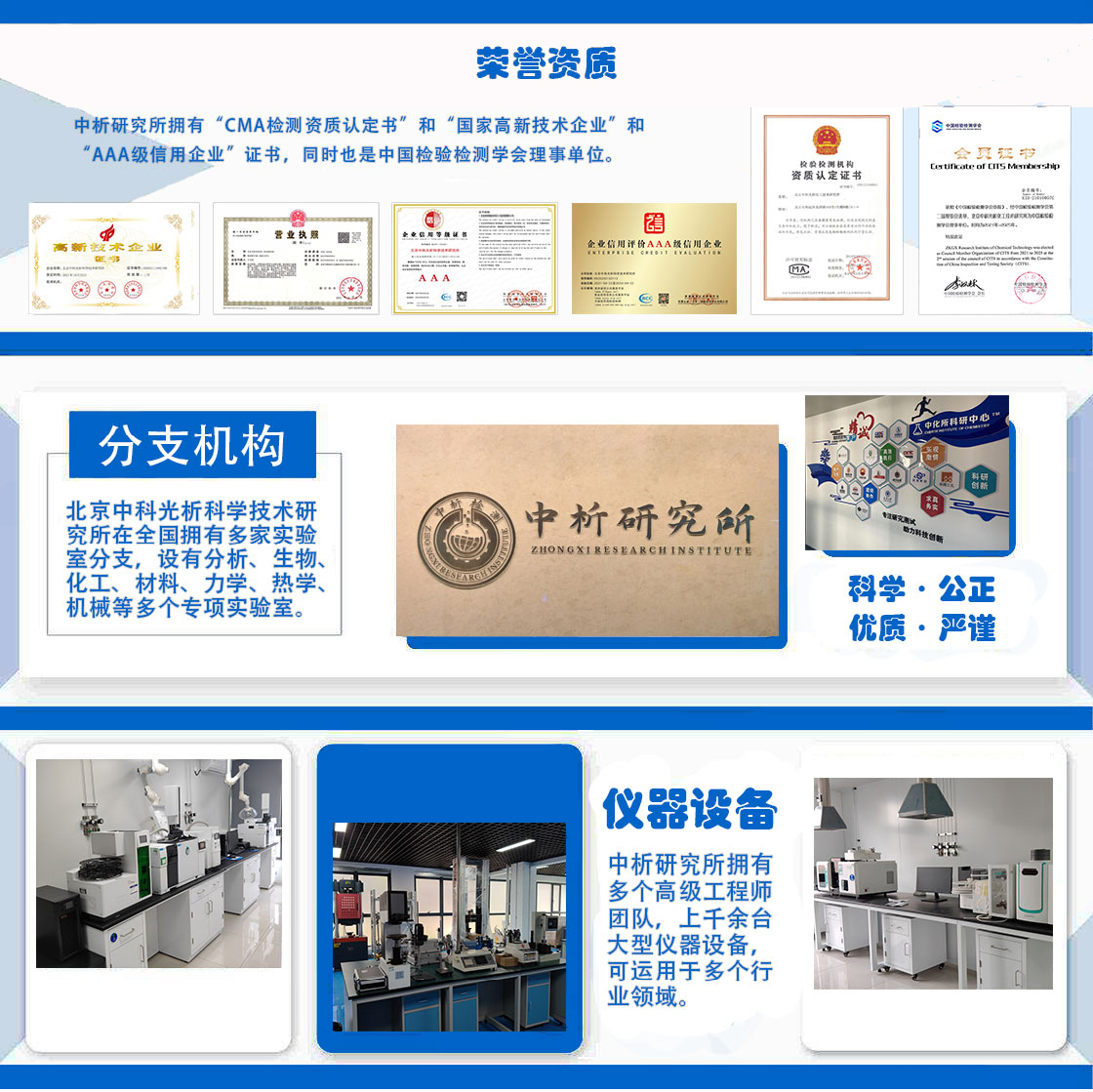
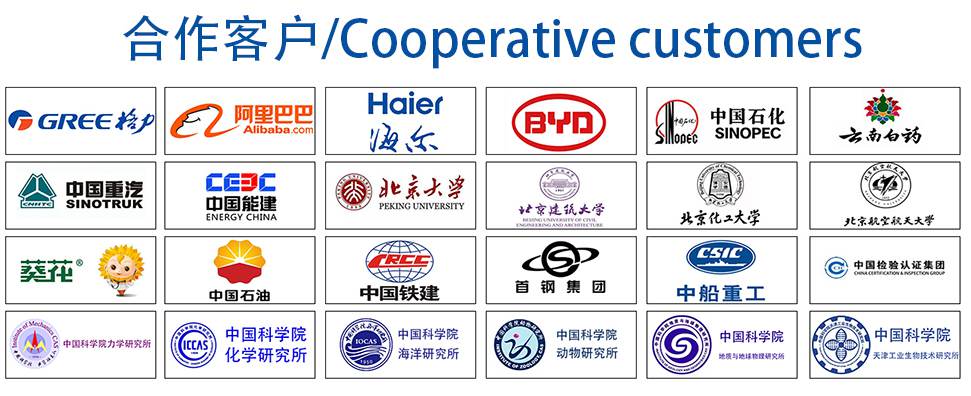