钢锤(钳工锤)检测项目及标准详解
一、外观质量检测
-
- 锤头:目视检测裂纹、折叠、毛刺、氧化皮等缺陷。
- 锤柄:检查木材(如白蜡木)是否存在虫眼、腐朽或开裂;金属/纤维手柄需检测表面涂层均匀性。
- 锤顶:不允许有崩刃或明显变形。
- 标准依据:GB/T 13487《钢锤通用技术条件》规定表面粗糙度Ra≤12.5μm。
-
- 检查发黑、镀层(如镀铬)或涂漆工艺是否完整,盐雾试验需达到48小时无锈蚀(参照ISO 9227)。
二、尺寸与几何精度检测
-
- 锤头长度、锤面直径、楔口深度等,公差范围通常为±1mm。
- 锤头与锤柄安装孔的同轴度偏差≤0.5mm。
-
- 楔形锤顶的刃口角度误差≤±2°。
- 羊角锤分叉角度需符合设计图纸(通常为45°~55°)。
三、材料与硬度测试
-
- 锤头材料:中碳钢(如45#钢)或合金钢(如40Cr),碳含量需在0.40%~0.50%范围内。
- 锤柄材料:木材含水率≤12%(GB/T 20445),玻璃纤维需符合抗拉强度≥300MPa。
-
- 锤击面硬度:HRC 48-55(洛氏硬度),确保抗冲击性。
- 锤顶硬度:HRC 35-45,避免因过硬导致崩裂。
- 测试方法:采用硬度计在锤头不同位置取3点平均值。
四、力学性能测试
-
- 使用落锤试验机进行10次连续冲击,锤头不得开裂或变形。
- 锤柄需承受2倍标称重量冲击(如1kg锤头需通过2kg冲击测试)。
-
- 锤柄与锤头连接处施加3倍额定载荷,保持1分钟无松动。
-
- 金属锤柄需承受≥50N·m的扭力测试,验证连接可靠性。
五、平衡性与使用性能检测
-
- 支点法:将锤子置于平衡支架,重心偏移量应小于锤头长度的5%。
-
- 手柄形状符合人体工学,振动衰减率≥80%(参照ISO 28927-1)。
六、其他检测项目
-
- 产品需标注材质、规格、执行标准、制造商等信息。
- 包装需通过跌落试验(1m高度自由跌落3次无损坏)。
-
- 重金属含量(如铅、铬)符合RoHS指令要求。
七、检测流程与判定标准
-
- 每批次随机抽取5~10把进行全项目检测。
-
- 关键项(如硬度、抗冲击)全部合格,次要项允许5%不合格率。
八、常见问题及改进措施
- 硬度不足:调整热处理工艺(如淬火温度提升至820℃)。
- 锤柄松动:优化楔形销安装工艺或采用环氧树脂胶加固。
- 材料缺陷:加强钢材入厂检验,增加超声波探伤环节。
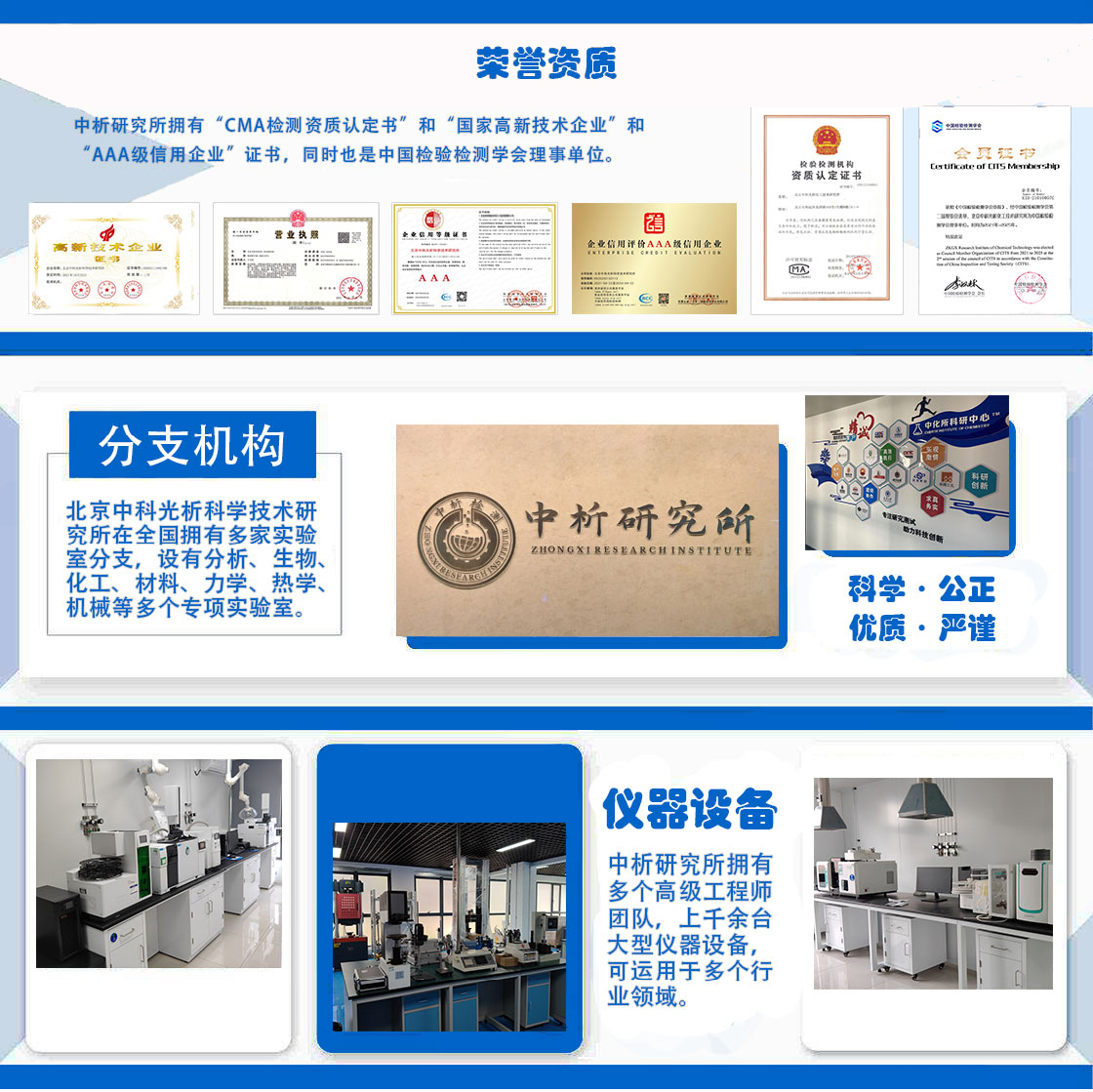
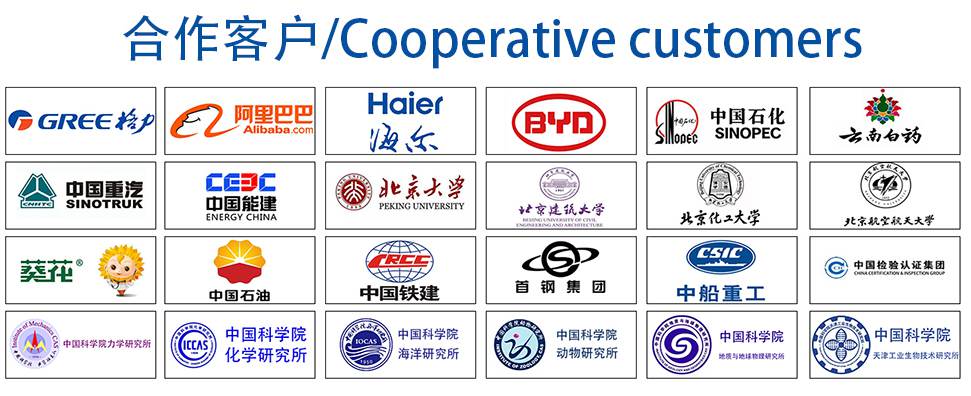
材料实验室
热门检测
251
211
187
201
193
199
206
198
204
211
200
195
192
198
193
189
203
195
204
199
推荐检测
联系电话
400-635-0567