钛检测的重要性与应用领域
钛及其合金因其高强度、耐腐蚀、生物兼容性等特性,在航空航天、医疗器械、化工设备及新能源领域广泛应用。随着工业需求的精细化发展,对钛材料的质量管控要求日益严格。钛检测是通过科学手段对材料成分、力学性能、微观结构及表面特性进行全面分析的过程,其核心目标是确保材料符合设计规范、工艺标准及安全服役要求。通过系统化检测,可有效避免因材料缺陷导致的设备失效风险,同时为生产工艺优化提供数据支持。
钛检测的核心项目与方法
1. 化学成分分析
通过X射线荧光光谱(XRF)、电感耦合等离子体质谱(ICP-MS)等精密仪器,检测钛材中主元素(Ti)含量及Al、V、Fe等合金元素的配比,确保符合GB/T 3620.1-2016等标准。氧、氮、氢等杂质元素需采用惰性气体熔融法(O/N/H分析仪)进行ppm级检测。
2. 力学性能检测
使用万能试验机进行拉伸试验(测定抗拉强度、屈服强度、延伸率)、硬度测试(布氏/洛氏硬度计)及冲击试验(夏比冲击试验机)。航空级钛合金需增加高温持久强度测试(800℃下持续载荷试验)。
3. 微观结构分析
采用金相显微镜观察α相、β相分布形态,通过扫描电镜(SEM)分析晶粒尺寸及夹杂物分布,配合电子背散射衍射(EBSD)技术检测晶体取向。医用钛植入物需额外进行孔隙率及表面粗糙度检测。
4. 耐腐蚀性能测试
根据ASTM G48标准开展点蚀临界温度试验,使用电化学工作站进行极化曲线测试。海洋工程用钛材需进行盐雾试验(ASTM B117),模拟5% NaCl溶液环境下的耐蚀表现。
5. 无损检测技术
采用超声波探伤(UT)检测内部裂纹,涡流检测(ET)识别表面缺陷,工业CT扫描实现三维缺陷重构。航天紧固件需进行渗透探伤(PT)确保无微裂纹。
检测标准与质量控制体系
国际通用标准包括ASTM B348(钛加工材)、ISO 5832-2(外科植入物),国内执行GB/T 5193(海绵钛)等系列标准。实验室需通过ISO/IEC 17025认证,建立从原料到成品的全流程检测数据库,实现批次可追溯管理。
结语
钛检测体系是保障高端装备可靠性的重要技术支撑,随着增材制造等新工艺的发展,针对3D打印钛合金的层间结合强度检测、残余应力分析等新兴项目正成为行业研究热点。未来检测技术将向智能化、在线化方向演进,为钛材料的创新应用提供更精准的质量保障。
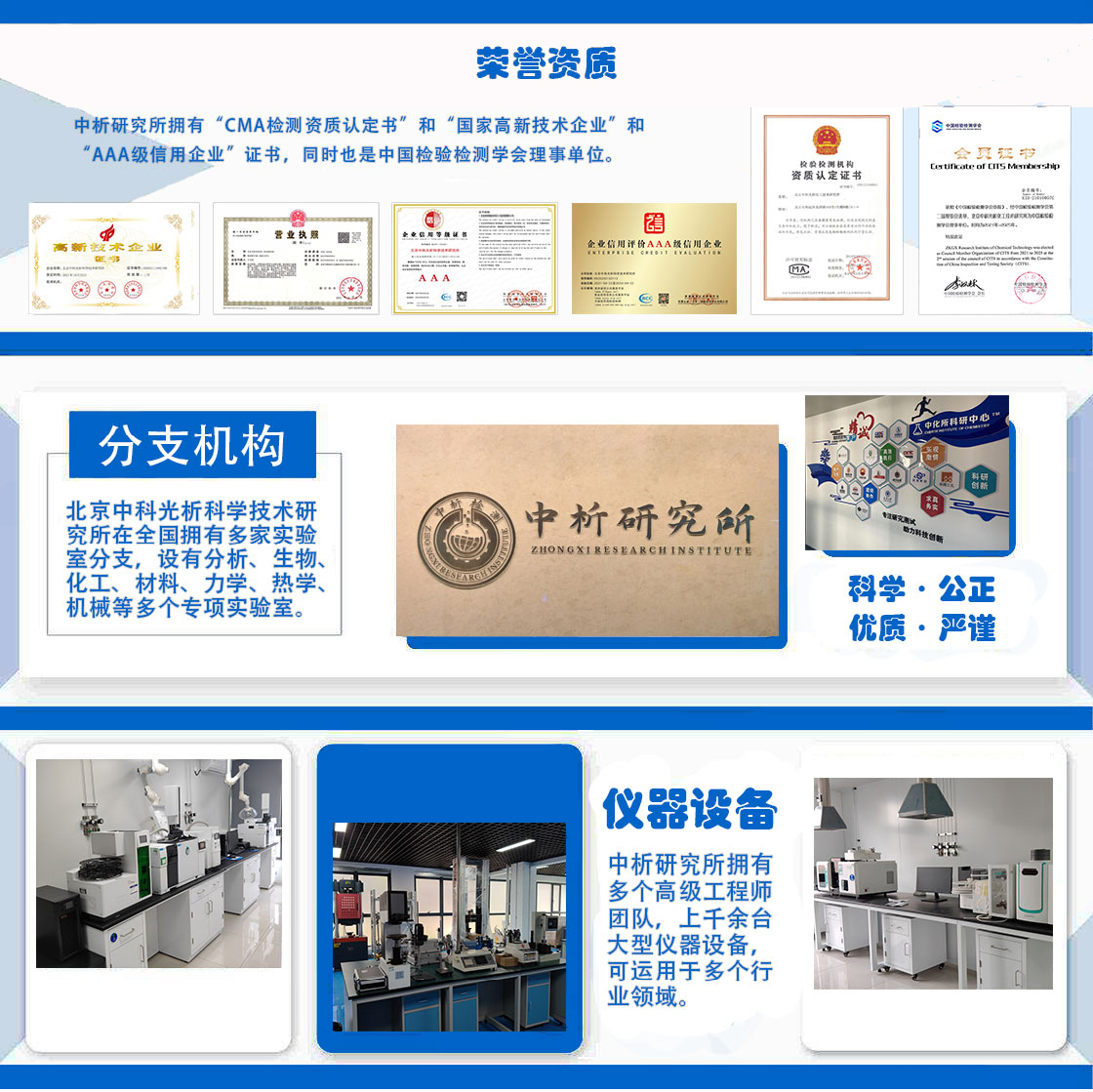
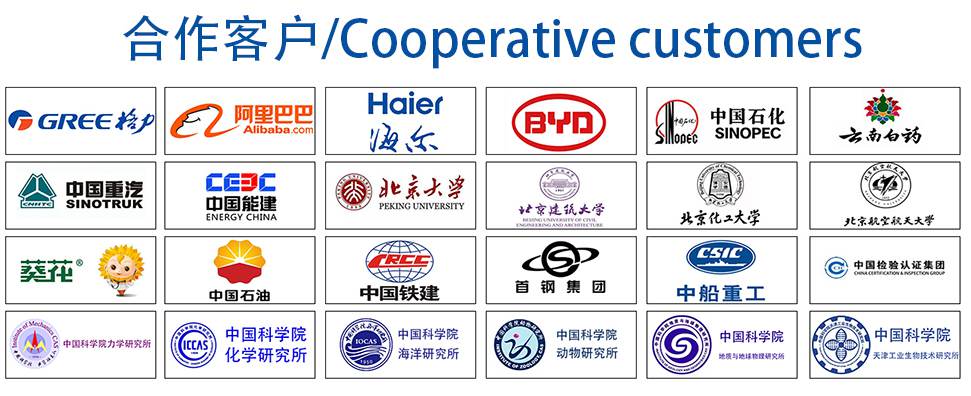