焊接结构用铸钢件检测的重要性与核心内容
焊接结构用铸钢件广泛应用于重型机械、桥梁、船舶、压力容器等领域,其性能直接影响整体结构的安全性和使用寿命。由于铸钢件在铸造过程中易产生气孔、缩松、夹杂等缺陷,且在焊接时可能引发热裂纹、应力集中等问题,因此需要通过系统化的检测手段确保材料的力学性能、化学成分及焊接质量符合标准要求。检测过程需参照国际或行业标准(如ASTM、ISO、GB/T等),涵盖原材料检验、加工过程监控及最终成品验收三个阶段,旨在全面评估铸钢件的可靠性。
关键检测项目及方法
1. 化学成分分析
通过光谱分析或化学滴定法测定铸钢件中碳(C)、硅(Si)、锰(Mn)、硫(S)、磷(P)等元素的含量,确保符合材料牌号要求。例如,硫、磷含量过高会显著降低材料的韧性和焊接性能。
2. 力学性能测试
包括拉伸试验(测定抗拉强度、屈服强度、延伸率)、冲击试验(评估低温韧性)及硬度测试。试样需取自铸钢件本体或单独浇注的试块,并按照标准进行加工与测试。
3. 无损检测(NDT)
• 超声波检测(UT):用于发现内部裂纹、缩孔等缺陷; • 射线检测(RT):通过X射线或γ射线检查焊缝及热影响区的气孔、未熔合缺陷; • 磁粉检测(MT)和渗透检测(PT):检测表面及近表面裂纹。
4. 金相检验
通过显微镜观察铸钢件的显微组织(如珠光体、铁素体分布)、晶粒度及非金属夹杂物等级,评估铸造工艺和热处理效果,同时检查焊接区域的熔合线状态。
5. 尺寸与形位公差检测
使用三坐标测量仪、卡尺等工具验证铸钢件的几何尺寸、表面平整度及装配接口精度,避免因尺寸偏差导致焊接结构失配。
6. 焊接质量专项评估
包括焊缝外观检查(余高、咬边)、焊接工艺评定(WPS/PQR)及焊后热处理验证。重点检测焊接热影响区的硬度变化,防止冷裂纹产生。
检测结果的应用与风险控制
检测数据需形成完整报告,作为质量验收依据。对于不合格项(如超标缺陷),需进行返修或报废处理,并分析原因以优化铸造或焊接工艺。通过系统性检测,可显著降低因材料缺陷引发的结构失效风险,保障焊接结构在复杂工况下的长期稳定运行。
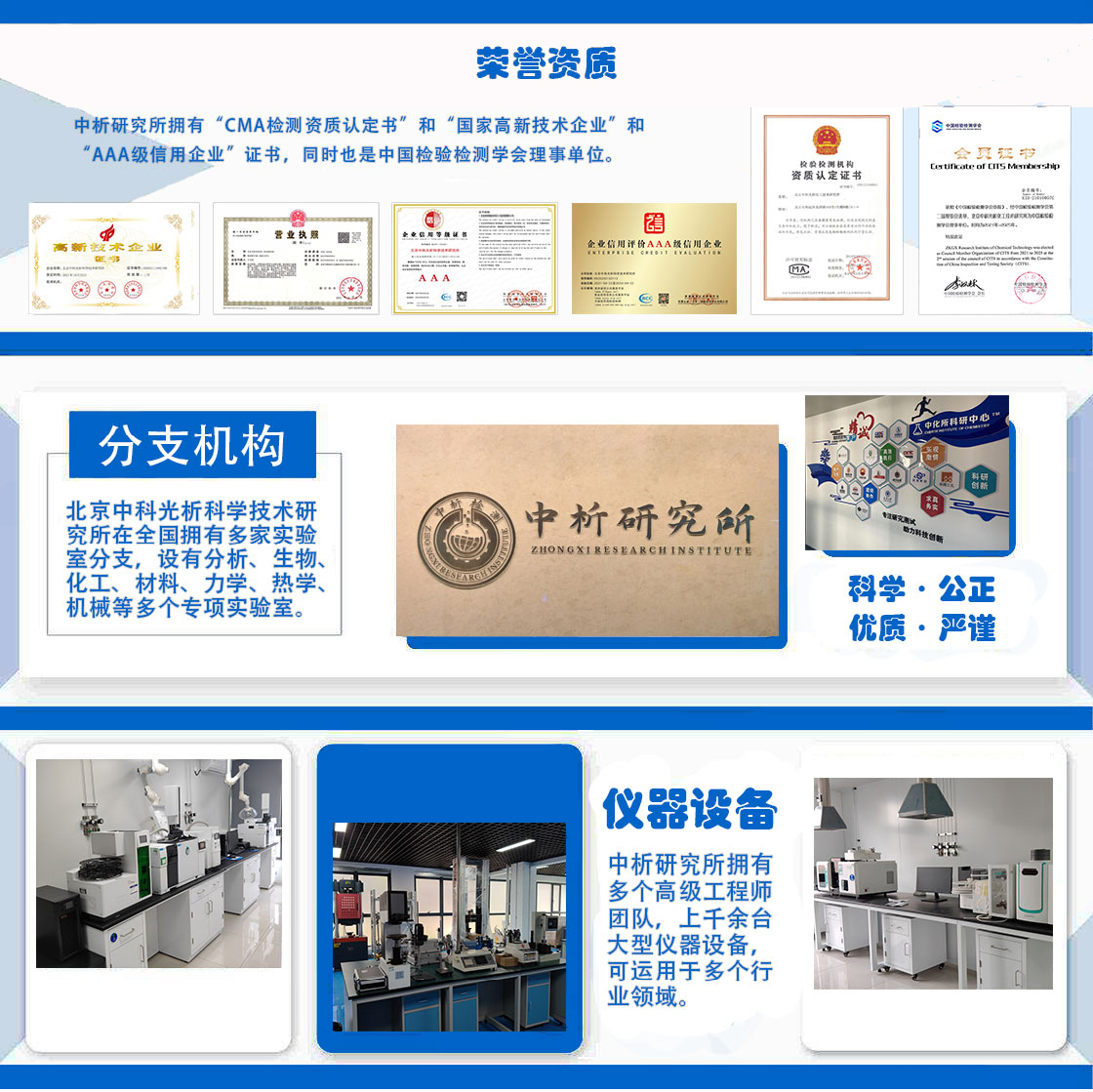
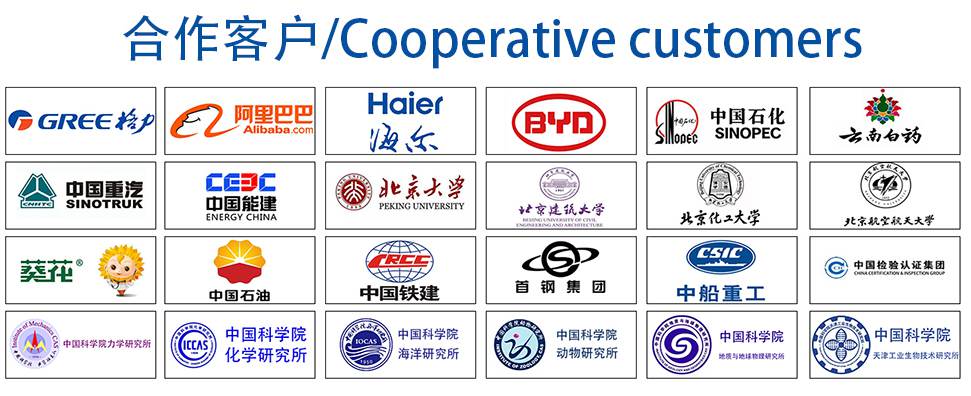