感应淬火钢件检测技术要点解析
感应淬火作为现代机械制造中广泛应用的热处理工艺,通过高频电流产生的交变磁场使钢件表面快速加热并急速冷却,可在工件表层形成高强度马氏体组织,同时保持芯部良好的韧性。这种工艺被广泛应用于齿轮、轴承、传动轴等关键零部件的强化处理。为确保淬火后工件的性能符合设计要求,必须对感应淬火钢件进行系统性质量检测。检测过程需覆盖材料力学性能、微观组织特征以及潜在缺陷等多个维度,具体检测项目需根据工件的服役条件和技术规范进行针对性设计。
关键检测项目及方法
1. 表面硬度检测
采用洛氏硬度计(HRC)或维氏硬度计(HV)对淬火层进行多点测量,要求硬度值波动范围控制在±2HRC以内。对于细长件或异形件,需使用专用夹具确保测试稳定性。检测时应避开脱碳区域,并按照ISO 6508标准进行数据校准。
2. 硬化层深度测定
通过金相法在垂直于淬火面的截面进行观测,使用4%硝酸酒精溶液腐蚀后,在500倍显微镜下测量马氏体区与基体的分界线。对于大批量检测可采用电磁法或超声波法实现无损快速测量,检测精度需达到±0.05mm。
3. 微观组织分析
借助扫描电镜(SEM)观察淬火层马氏体形态及碳化物分布,评估晶粒细化程度。通过能谱分析(EDS)检测表面元素偏析情况,确保无过热导致的晶界氧化现象。残余奥氏体含量需控制在5%-15%范围内。
4. 残余应力检测
使用X射线衍射法测量表面残余压应力分布,典型值应达到800-1200MPa。对于深层淬火件,需结合逐层电解抛光法建立三维应力场模型。过高的残余应力可能引发应力腐蚀开裂风险。
5. 裂纹及缺陷检测
采用磁粉探伤(MT)或渗透探伤(PT)检测表面微裂纹,灵敏度需达到0.5mm级。对于重要承力件,推荐使用涡流检测(ET)或超声相控阵技术(PAUT)进行全体积扫描,可发现深度2mm以上的内部缺陷。
检测结果判定标准
所有检测数据需对照ASTM A255、GB/T 5617等行业标准进行判定。其中硬化层深度偏差不得超过图纸要求的±10%,过渡区梯度应平缓无明显突变。检测报告需包含微观组织照片、硬度分布曲线及缺陷定位图谱等关键证据链。
通过建立完整的检测流程和质量控制体系,可有效避免淬火变形、软点、淬裂等质量问题的发生。建议在工艺验证阶段增加热像仪监控淬火温度场分布,并结合大数据分析优化感应器参数,从源头提升产品质量稳定性。
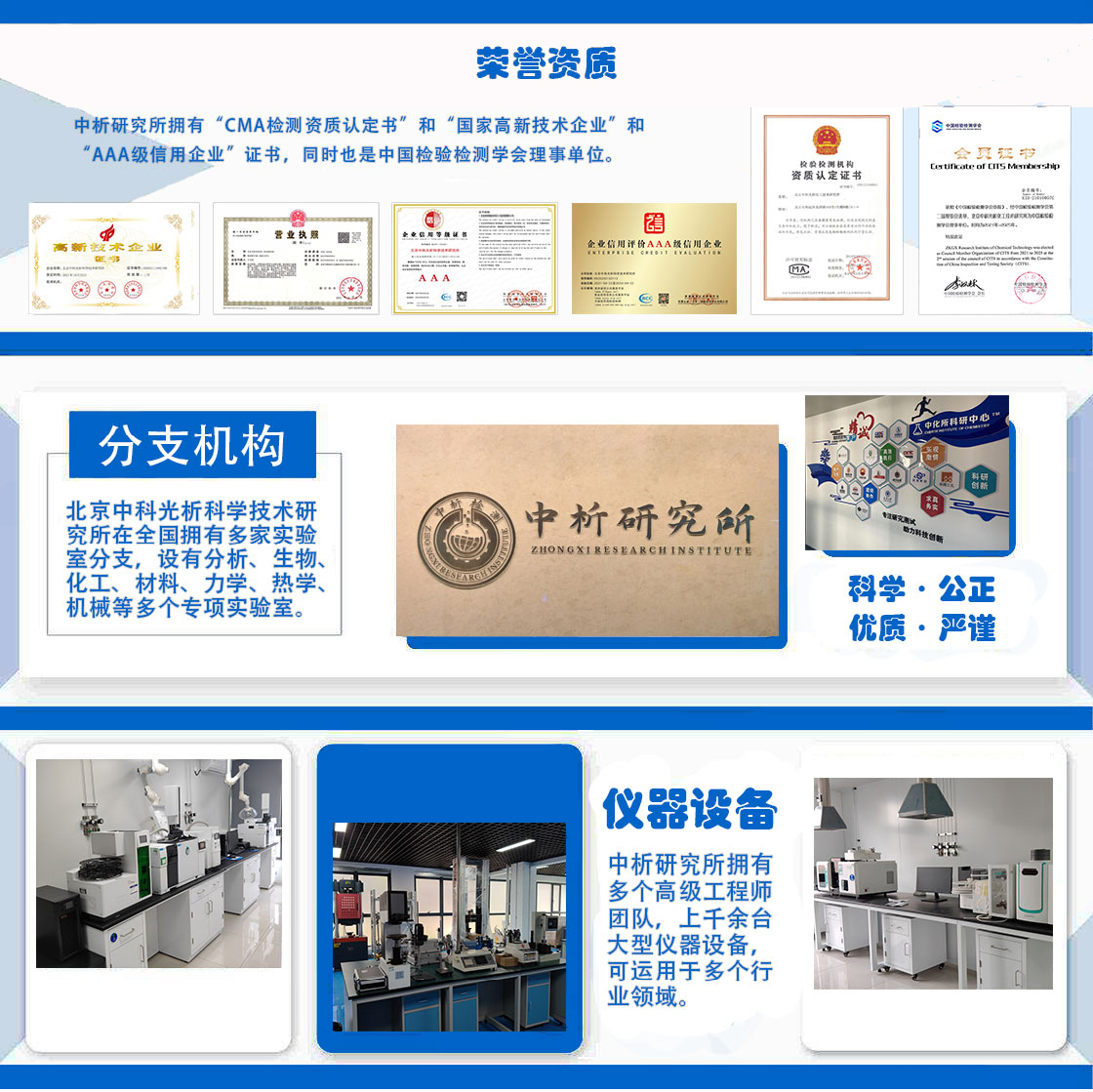
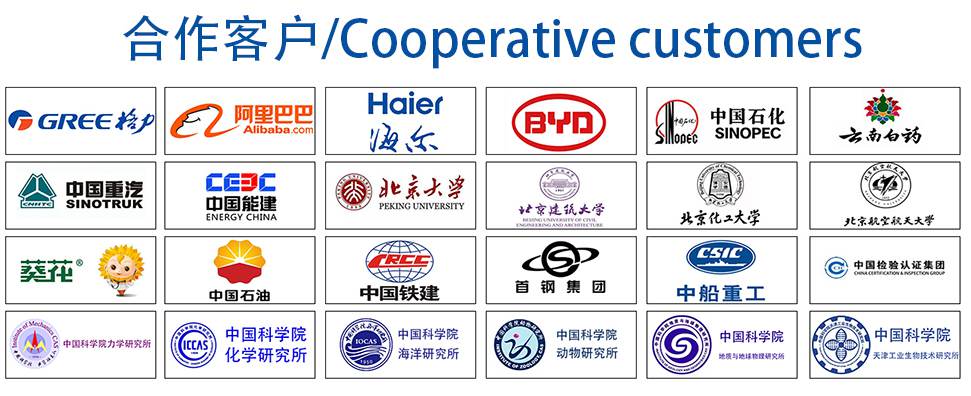