作为摩托车传动系统的核心部件,链条与链轮的配合状态直接影响着动力传输效率和行车安全性。在长期使用过程中,链条拉伸、链轮齿形磨损以及润滑不良等问题可能导致传动异响、动力损耗甚至突发性断裂事故。专业检测显示,30%的摩托车故障与链条系统维护不当直接相关,定期进行系统性检测可有效延长传动系统寿命2-3倍。本文将重点解析链条链轮检测的六大关键项目与技术标准。
一、外观完整性检测
使用10倍放大镜对链条进行360°目视检查,着重观察链片是否存在裂纹、变形,滚子表面是否出现剥落或异常磨损。链轮检测需测量至少8个对称齿形的齿高与齿宽,任何单齿磨损量超过原尺寸15%即判定失效。特别注意检查链轮固定螺栓的防松标记是否错位,这往往是早期松动的预警信号。
二、链条拉伸量检测
采用专用链条规或游标卡尺测量20节链条的标准节距,新链条允许误差±1.5mm,当累计伸长量超过标准值3%时必须更换。经验表明,常见428规格链条在行驶8000公里后平均伸长量达2.8mm,超过临界值会导致跳齿风险提升60%以上。
三、链轮啮合状态测试
通过蓝色接触印痕法检测齿面接触区域,合格品应呈现均匀分布的矩形接触斑,面积占比不低于齿面的75%。使用数显扭力扳手测量转动阻力矩,前链轮标准值为0.8-1.2N·m,后链轮1.5-2.0N·m。异常阻力波动往往预示齿形磨损或链条滚子卡滞。
四、润滑效能评估
采用荧光检漏剂检测润滑油膜连续性,良好润滑状态下应形成完整油膜覆盖。使用油品粘度计测量链条油100℃运动粘度,推荐值在120-150cSt之间。特别注意检查链轮齿根处的油泥沉积情况,超过0.3mm厚度的积碳会显著加剧磨损速率。
五、运行轨迹偏差检测
安装激光对中仪测量前后链轮平面度偏差,行业标准要求不超过0.5mm/m。使用百分表检测链轮径向跳动,前链轮允许值≤0.3mm,后链轮≤0.5mm。实际案例显示,每增加0.1mm跳动量会导致链条摆动幅度扩大15%,加速链节疲劳。
六、动态振动频谱分析
通过加速度传感器采集传动系统振动信号,重点监测200-500Hz频段的异常峰值。正常工况下振动加速度应≤4m/s²,当特定倍频分量超过基准值200%时,提示存在链节卡死或链轮偏心故障。建议每5000公里进行预防性振动检测。
专业检测机构统计数据显示,严格执行上述检测流程可使传动系统维护成本降低40%,同时将非计划停驶率控制在5%以下。建议雨季或恶劣路况行驶后增加检查频次,使用符合JIS D9417标准的检测工具,并建立完整的部件磨损档案以指导预防性更换决策。
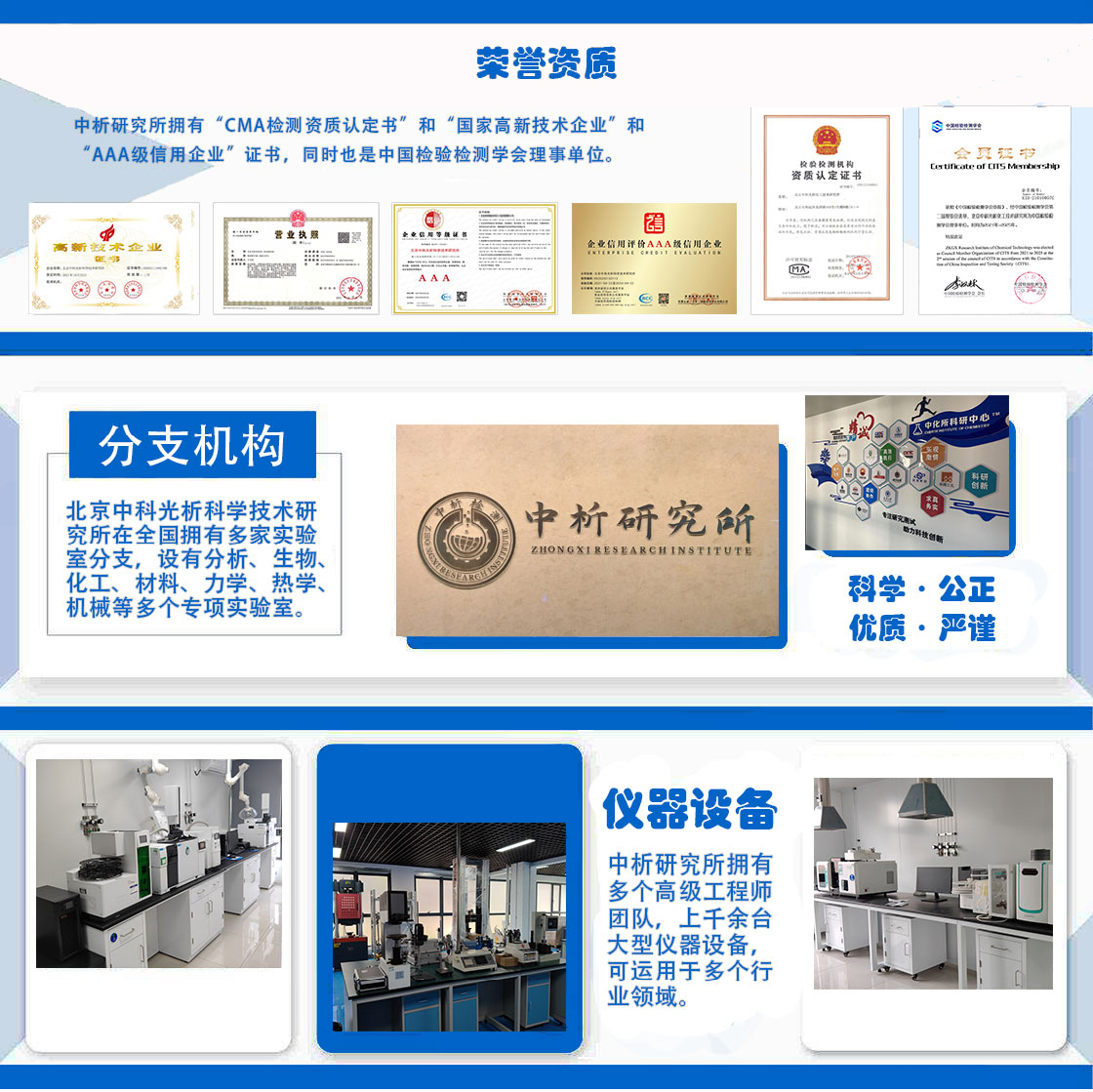
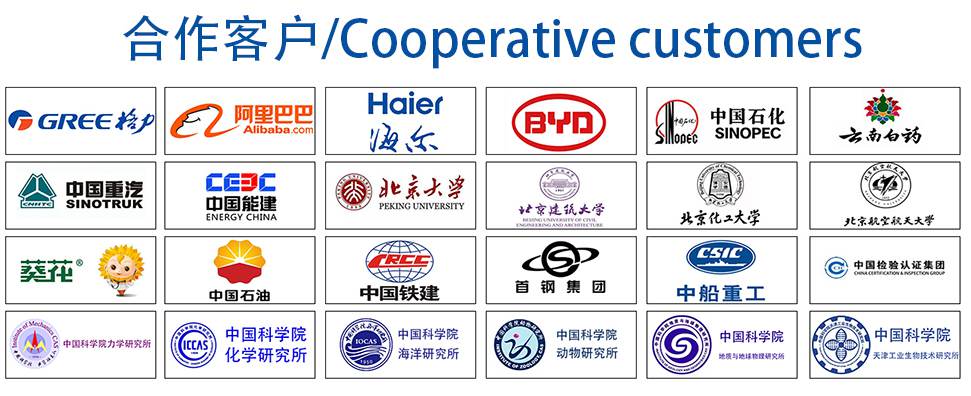