汽车电子零部件检测的重要性与核心项目
随着汽车智能化、电动化的发展,电子零部件在整车中的占比已超过40%,其性能直接影响车辆的安全性、可靠性和用户体验。汽车电子零部件检测是通过科学手段验证产品是否符合设计要求、行业标准及法规的关键环节。由于车辆需应对复杂的使用环境(如极端温度、振动、电磁干扰等),检测不仅覆盖功能验证,还需模拟实际工况下的耐久性、抗干扰能力及故障响应机制,确保从芯片、传感器到控制系统的全链条质量可控。
核心检测项目分类
1. 环境可靠性检测
模拟车辆在高温、低温、湿热、盐雾、振动等极端环境下的长期运行状态,验证零部件耐受能力。例如: - **温度循环测试**:-40℃至125℃快速切换,检测材料膨胀/收缩导致的连接失效; - **机械振动测试**:模拟路面冲击,分析焊点断裂、元件脱落风险; - **防尘防水测试**:依据IP等级标准评估密封性(如IP67)。
2. 电磁兼容性(EMC)检测
确保电子部件在电磁干扰下正常工作,同时不对外产生超标辐射: - **辐射发射测试**:检测零部件是否超出CISPR 25等标准的电磁辐射限值; - **抗干扰测试**:通过ISO 11452系列验证对雷达、手机信号等外部干扰的抵抗能力; - **静电放电(ESD)测试**:评估人体接触或工具操作时的静电防护性能。
3. 功能安全与失效分析
基于ISO 26262标准,对刹车控制单元(ECU)、电池管理系统(BMS)等安全关键部件进行: - **故障注入测试**:人为模拟短路、信号失真等场景,验证系统冗余设计; - **失效模式影响分析(FMEA)**:量化风险等级并制定缓解措施; - **软件逻辑验证**:通过MIL/SIL/HIL测试链确保代码在异常条件下的响应符合预期。
4. 电气性能检测
覆盖电压波动、电流负载、信号完整性等核心参数,例如: - **电源瞬态测试**:模拟车辆启动/熄火时的电压瞬变(如LV124); - **CAN/LIN总线通信测试**:校验数据传输速率、错误帧处理机制; - **功耗分析**:优化新能源车低功耗模式的电能管理效率。
5. 耐久性与寿命预测
通过加速寿命试验(ALT)推算零部件使用寿命,包括: - **高低温交变老化测试**; - **插拔寿命测试**(如充电接口万次插拔验证); - **材料疲劳分析**:利用有限元仿真(FEA)预判金属/塑料件的磨损趋势。
检测技术发展趋势
随着自动驾驶和车联网技术的普及,检测领域正融入AI算法、数字孪生等创新手段。例如,通过机器学习分析测试数据中的异常模式,或构建虚拟模型提前预测硬件与软件的兼容性问题。未来,检测体系将更注重跨系统协同验证,以应对电子电气架构从分布式向域集中式的转型挑战。
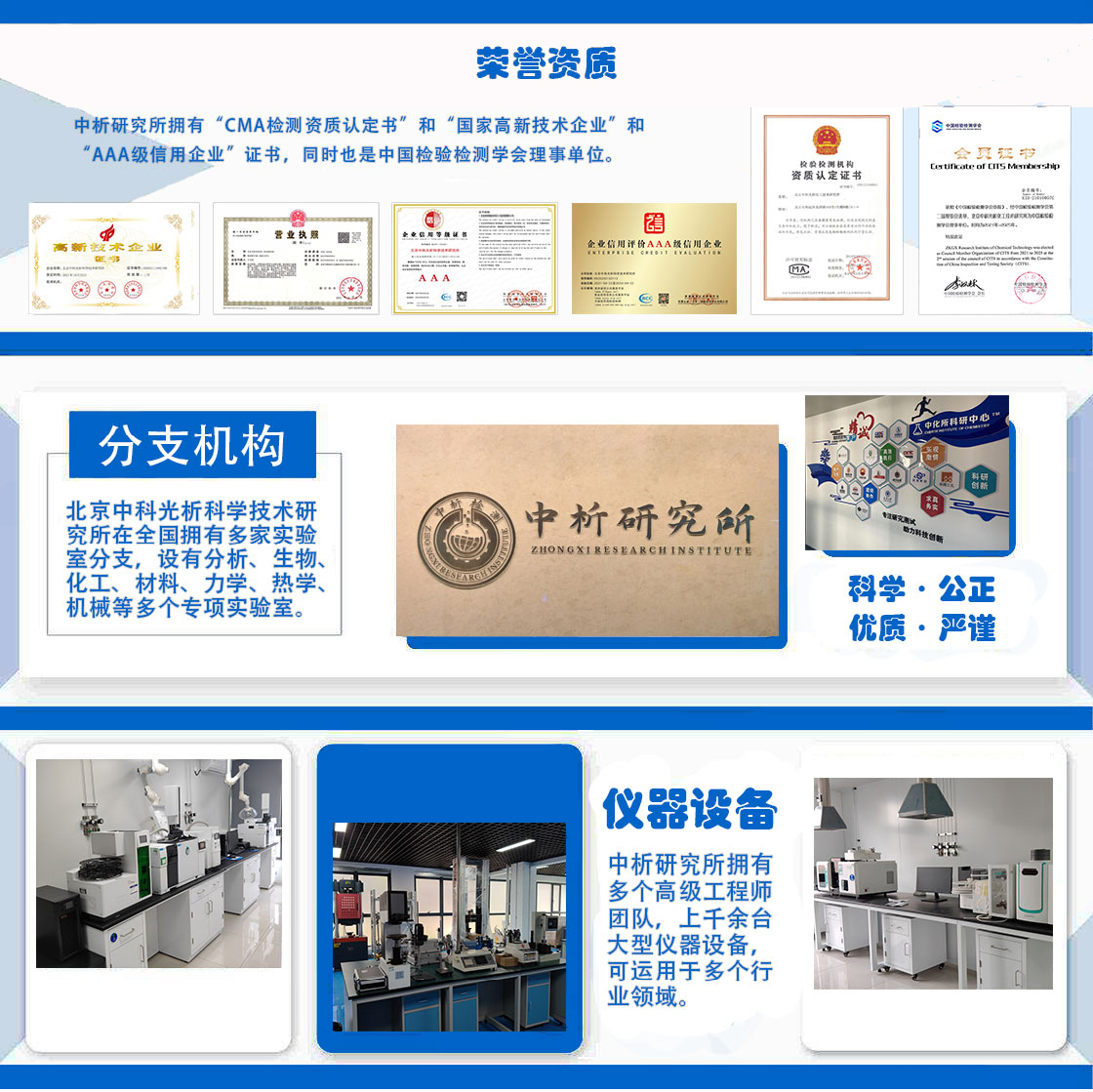
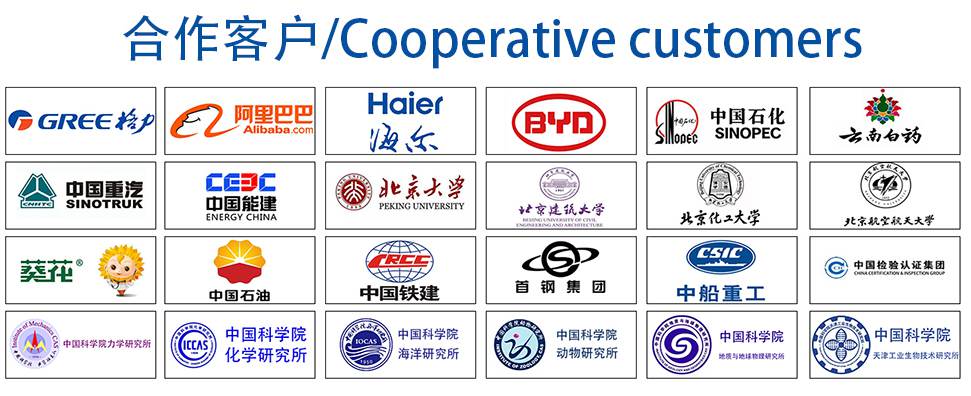