随着我国环保政策的不断加码和"双碳"战略的深入推进,燃煤电厂及工业锅炉的烟气脱硝治理已成为大气污染防治的重点领域。选择性催化还原(SCR)和选择性非催化还原(SNCR)作为主流的脱硝技术,其装备性能直接影响氮氧化物(NOx)的减排效果。在工程实践中,脱硝系统的运行效能不仅取决于设计与安装质量,更需要通过全面的检测评估来保障设备长期稳定运行。本文将系统解析燃煤烟气脱硝技术装备检测的关键环节。
一、催化剂性能检测
作为SCR脱硝核心组件,催化剂的活性直接决定脱硝效率。检测项目包括:1) 活性组分含量测定,采用XRF检测钛、钨、钒等元素的配比;2) 比表面积测试,通过BET法评估催化剂微观结构;3) 抗压强度检测,模拟实际工况下的机械耐久性;4) SO2/SO3转化率测试,控制副产物生成。现场检测时还需结合运行时间,建立催化剂寿命预测模型。
二、氨逃逸监测与调控
氨逃逸率是脱硝系统的重要考核指标,超标将导致空预器堵塞等次生问题。检测采用激光光谱法实时监测,重点在反应器出口设置多点采样。根据《火电厂烟气脱硝技术导则》要求,逃逸氨浓度应控制在2.5ppm以下。检测中需同步分析喷氨格栅的流量均匀性,优化AIG调节阀开度,确保氨氮摩尔比(NSR)稳定在0.8-1.05之间。
三、系统阻力特性测试
脱硝装置运行压差直接影响引风机电耗,检测项目包括:1) 空塔阻力测试,验证设计压降参数;2) 催化剂层压损监测,每层压差应≤300Pa;3) 烟道流场模拟,采用CFD技术优化导流板布置。实际检测中常发现因积灰导致的异常压升,需结合声波吹灰器效果评估,建立压差-清灰周期关联曲线。
四、温度场均匀性检测
SCR系统对反应温度窗口有严格要求(300-420℃),检测重点包括:1) 反应器截面温度分布,使用网格法布置热电偶;2) 烟气温度梯度变化,控制纵向波动≤15℃/m;3) 省煤器旁路调节性能测试。实践中发现,低负荷工况下的温度跌落会引发催化剂中毒,需检测混合加热装置的响应特性。
五、综合性能评估体系
完整的检测体系应包含:1) 脱硝效率连续监测,确保≥85%的设计值;2) 氨耗量统计,核算运行经济性;3) 副产物分析,检测硫酸氢铵生成量;4) CEMS数据比对,验证在线监测准确性。通过建立包含12项关键指标的评估矩阵,可实现脱硝系统的全生命周期管理。
当前行业检测技术正向智能化方向发展,激光诱导击穿光谱(LIBS)等新型检测手段逐步应用,大数据平台实现检测数据的实时分析与预警。未来随着《燃煤烟气脱硝装备检测规范》等标准的完善,检测工作将更趋标准化和体系化,为打赢蓝天保卫战提供坚实的技术支撑。
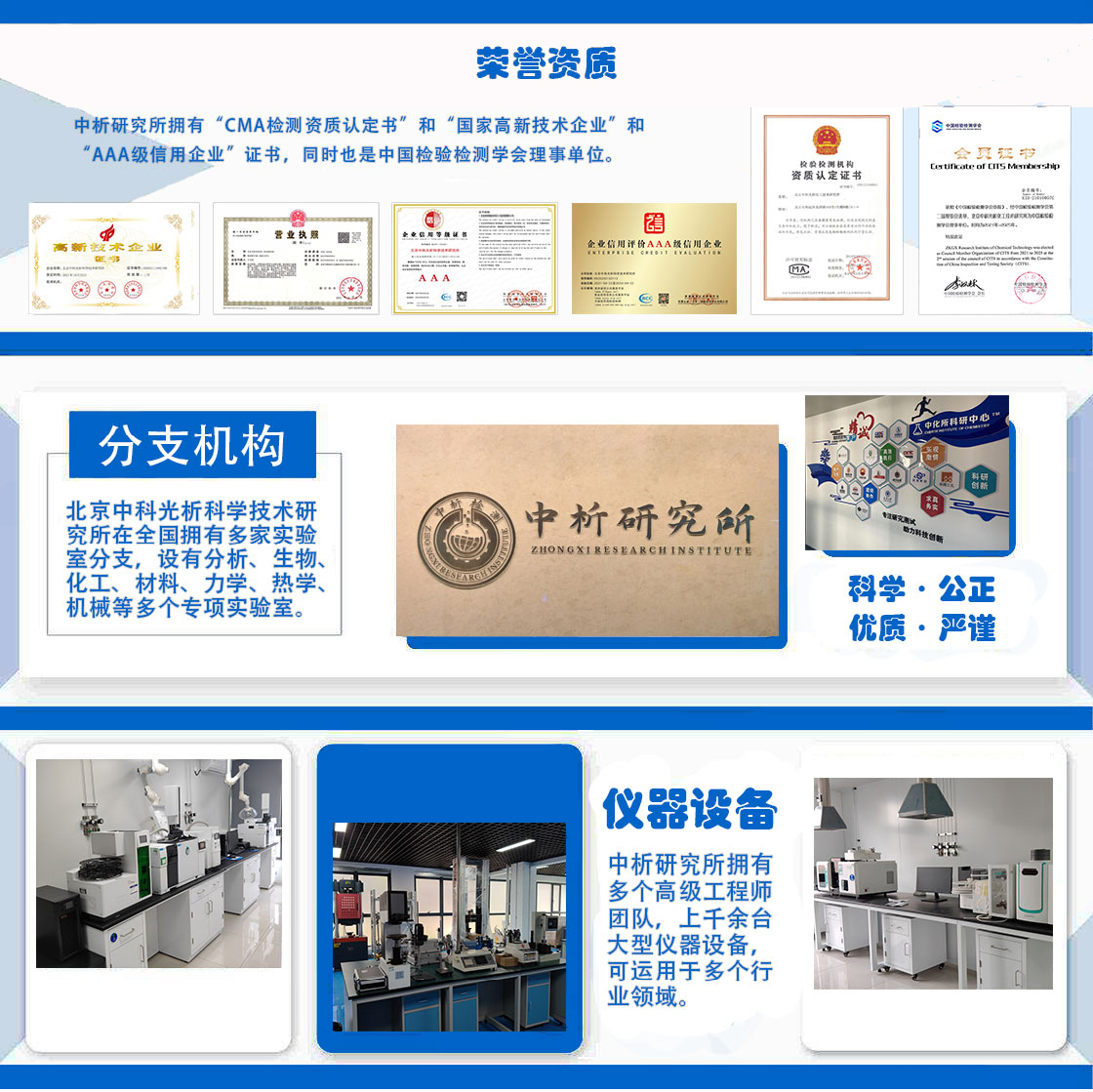
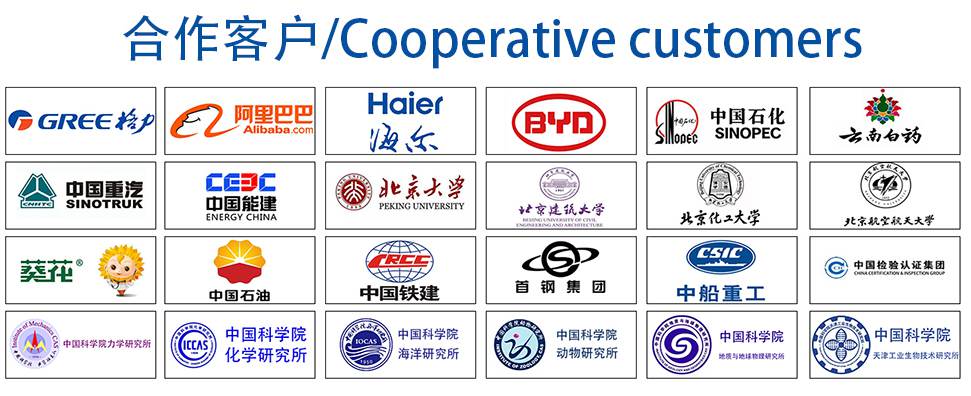