钢结构焊接件检测的重要性与核心内容
钢结构焊接件作为现代建筑、桥梁、工业设备等领域的关键承力构件,其质量直接影响整体结构的安全性和使用寿命。焊接过程中可能出现的裂纹、气孔、未熔合等缺陷,若未及时检出,将导致构件强度下降甚至引发灾难性事故。因此,系统化的焊接件检测是保障工程质量的必要环节,涉及外观检查、无损检测、力学性能测试等多维度评估,需严格遵循国家标准(如GB 50661)及行业规范。
检测项目一:外观质量检测
通过目视或放大镜检查焊缝表面成型质量,包括焊缝宽度、余高、错边量等尺寸参数。重点排查咬边、焊瘤、表面气孔等可见缺陷,使用焊缝检验尺、卡规等工具进行量化测量,确保符合设计图纸要求的公差范围。同时检查焊渣清除情况及母材热影响区外观状态。
检测项目二:无损检测(NDT)
采用超声波探伤(UT)、射线检测(RT)、磁粉检测(MT)和渗透检测(PT)等技术:
- 超声波探伤:利用高频声波探测内部缺陷的深度和尺寸,适用于厚板对接焊缝
- 射线检测:通过X/γ射线成像发现体积型缺陷,对气孔、夹渣敏感
- 磁粉检测:用于铁磁性材料表面及近表面裂纹检测
- 渗透检测:识别开放性表面缺陷,适用于非多孔材料
检测项目三:力学性能测试
通过取样试验验证焊接接头的承载能力:
- 拉伸试验测定抗拉强度、屈服强度
- 弯曲试验评估焊缝塑性变形能力
- 冲击试验检测低温韧性
- 硬度测试分析热影响区性能变化
检测项目四:化学成分分析
使用光谱仪对焊缝金属进行元素含量检测,验证焊材与母材的相容性。重点监测碳当量(CEV)、硫磷等有害元素含量,避免焊接冷裂纹倾向。对于耐候钢等特殊材料,还需检测铜、铬等合金元素的分布均匀性。
检测项目五:金相组织分析
通过显微镜观察焊缝及热影响区的微观组织,评估焊接热循环导致的晶粒粗化、马氏体转变等情况。配合显微硬度测试,识别可能出现的脆硬相,为工艺改进提供依据。金相制样需严格遵循GB/T 13298规范。
智能化检测技术应用
随着技术进步,相控阵超声波、数字射线成像(DR)、激光扫描等新型检测手段逐步普及。例如PAUT技术可实现多角度声束扫描,自动生成3D缺陷图像;TOFD法则能精确测定缺陷高度。结合大数据分析,可建立焊接质量预测模型,提升检测效率50%以上。
钢结构焊接件检测贯穿设计验证、过程控制、成品验收全周期,需要检测人员同时具备扎实的理论知识和高超的操作技能。通过建立完善的检测体系,可最大限度消除质量隐患,为钢结构工程的安全服役提供坚实保障。
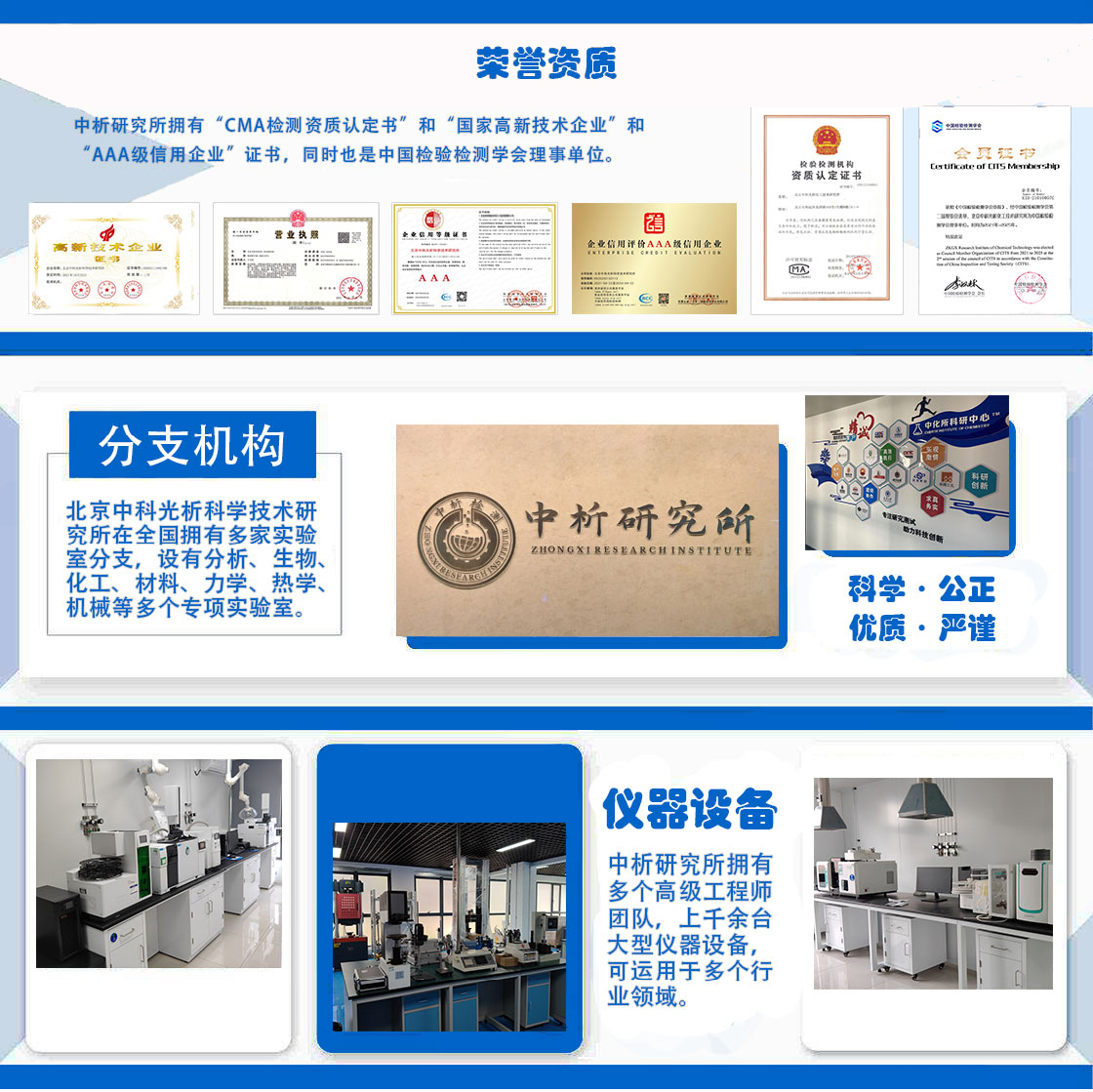
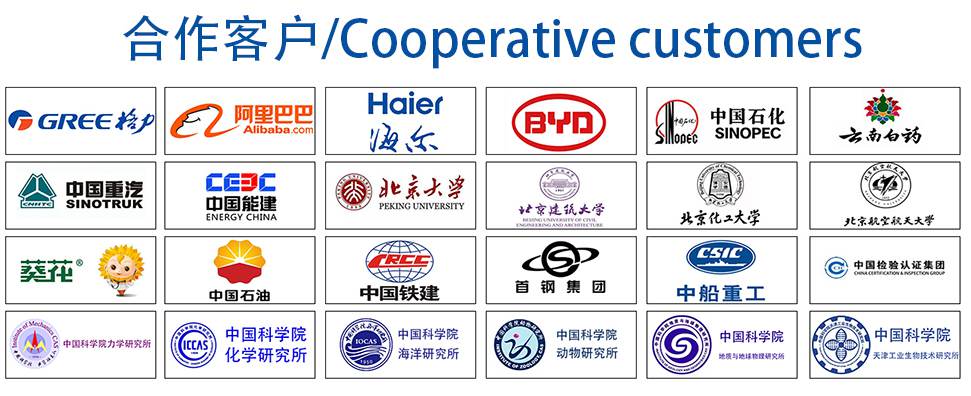