塑料件制品检测:全面把控产品质量的关键环节
在工业制造领域,塑料件制品凭借其轻量化、耐腐蚀、易成型等特性,已广泛应用于汽车、电子、医疗及日用品等行业。然而,塑料制品的性能稳定性直接影响产品使用寿命与安全性,因此建立科学规范的检测体系至关重要。塑料件制品检测通过系统性测试与数据分析,可精准评估材料性能、工艺质量及环境适应性,为产品研发、生产管控和品质验收提供关键依据。
核心检测项目分类解析
1. 物理性能检测
包含拉伸强度、弯曲强度、冲击强度测试(如悬臂梁/简支梁冲击试验)、硬度(邵氏/洛氏硬度)、熔融指数(MFI)等指标检测。其中熔融指数测试可反映材料加工流动性,直接影响注塑成型工艺参数设定。
2. 化学性能检测
通过傅里叶红外光谱(FTIR)进行材料成分鉴定,气相色谱-质谱联用(GC-MS)分析可塑剂、阻燃剂等添加剂含量,同时需进行RoHS指令要求的铅、镉、汞等重金属检测,以及REACH法规中SVHC高度关注物质的筛查。
3. 环境适应性测试
包括高低温循环试验(-40℃至120℃)、湿热老化测试(85℃/85%RH)、UV紫外线加速老化试验、盐雾腐蚀测试等,模拟产品在极端环境下的性能衰减情况。医疗类塑料件还需进行生物相容性评估。
4. 尺寸与形位公差检测
采用三坐标测量仪(CMM)进行三维尺寸扫描,结合投影仪进行轮廓比对,重点控制关键配合面的平面度、圆度及位置度公差。对于透明/半透明件,需额外进行光学畸变检测。
新兴检测技术发展趋势
随着行业需求升级,检测技术正向智能化、在线化发展。工业CT无损检测可实现内部结构缺陷可视化分析,激光扫描技术配合AI算法可进行0.005mm级微尺寸自动判定。此外,针对可降解塑料的堆肥化测试、碳足迹评估等绿色检测项目正成为行业新焦点。
通过建立覆盖全生命周期的检测体系,企业不仅可规避质量风险,更能通过检测数据反哺工艺优化,最终实现产品可靠性提升与综合成本控制的双重目标。
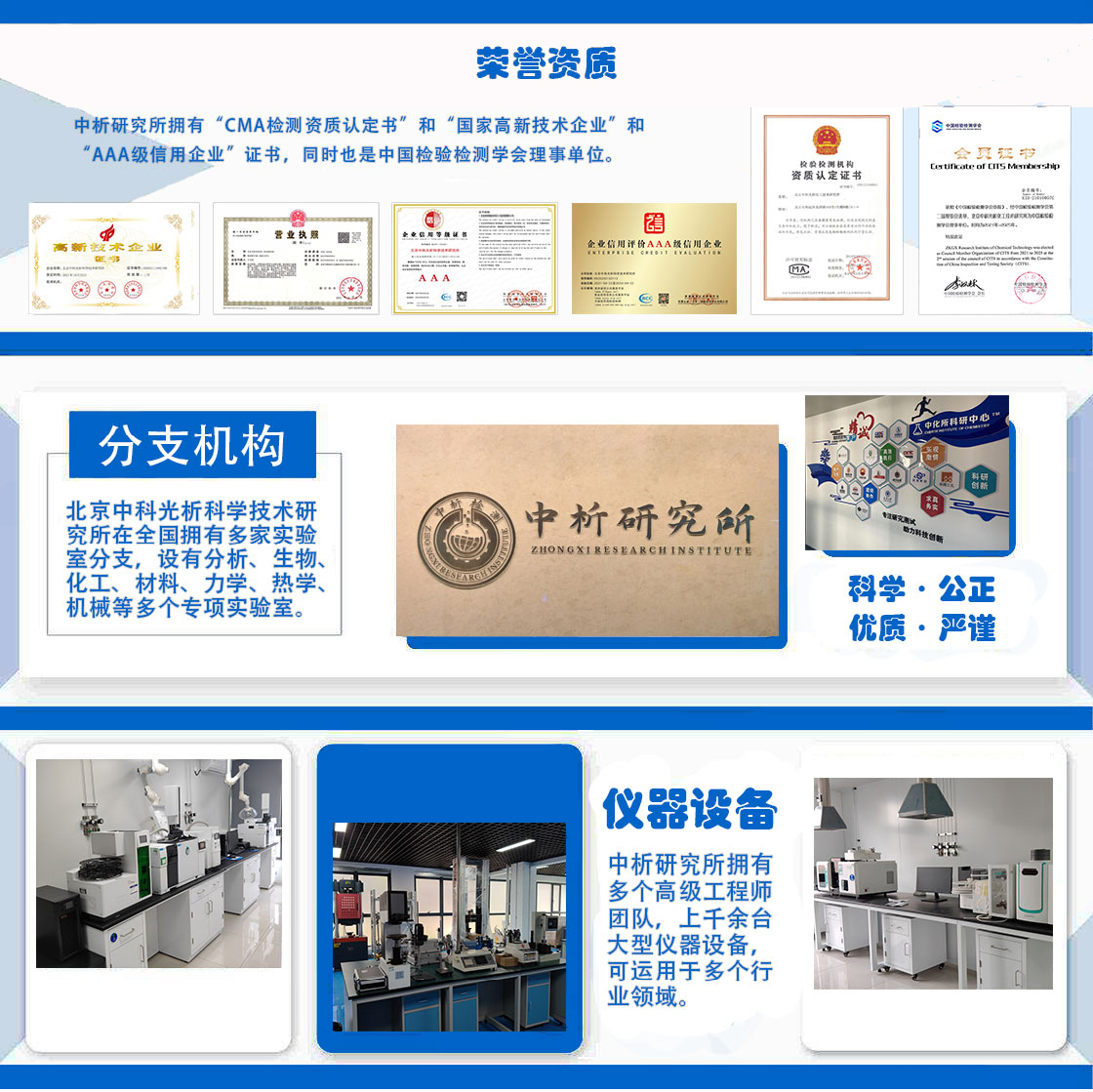
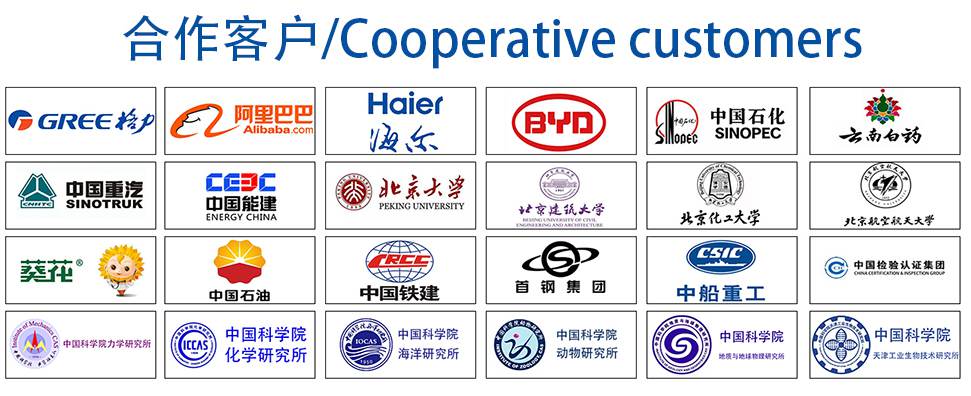