热交换器检测的重要性与核心项目解析
热交换器作为工业生产、能源转换和暖通系统中的核心设备,其性能直接影响设备能效、运行安全及维护成本。长期运行中,换热管腐蚀、结垢、密封失效等问题会导致传热效率下降,甚至引发泄漏事故。因此,针对热交换器的定期检测已成为石化、电力、制冷等行业的强制性规范要求。根据GB 151-2014《热交换器》标准,检测需覆盖结构完整性、材料性能、运行参数三大维度,并通过专业方法评估其剩余寿命与安全风险。
核心检测项目及技术要点
1. 泄漏与密封性检测
采用氦质谱检漏法(精度达1×10⁻⁹ Pa·m³/s)或气泡法对管板接头、壳体焊缝进行密封性验证。对于板式换热器,需通过0.8-1.25倍设计压力的水压试验,保压30分钟无压降视为合格。
2. 壁厚与腐蚀状态评估
使用超声波测厚仪(分辨率±0.01mm)对换热管、壳体进行网格化厚度测量,比对初始数据计算腐蚀速率。对高风险区域辅以渗透检测(PT)或射线检测(RT),发现裂纹深度超过壁厚10%需立即停用。
3. 结垢与堵塞分析
通过内窥镜检查管束内壁结垢情况,采用XRF光谱仪分析垢样成分(CaCO₃、Fe₂O₃等)。当污垢系数超过设计值15%时,需启动化学清洗或机械通管程序。
4. 传热性能测试
基于对数平均温差法(LMTD)计算实际传热系数,对比设计值评估效率衰减。对于管壳式换热器,压降增加20%或效率下降10%即触发效能预警。
5. 振动与应力检测
采用动态应变仪监测流体诱导振动(FIV)频率,评估管束固有频率与激励频率的匹配度。通过有限元分析(FEA)预测高应力集中区域,预防疲劳失效。
智能化检测技术发展趋势
随着工业物联网(IIoT)技术的应用,无线声发射传感器可实时监测微泄漏信号,AI算法能通过热成像图谱自动识别异常温度场分布。数字化孪生模型结合历史检测数据,可精准预测换热器剩余使用寿命(RUL),推动检测模式从定期维护向预测性维护转型。
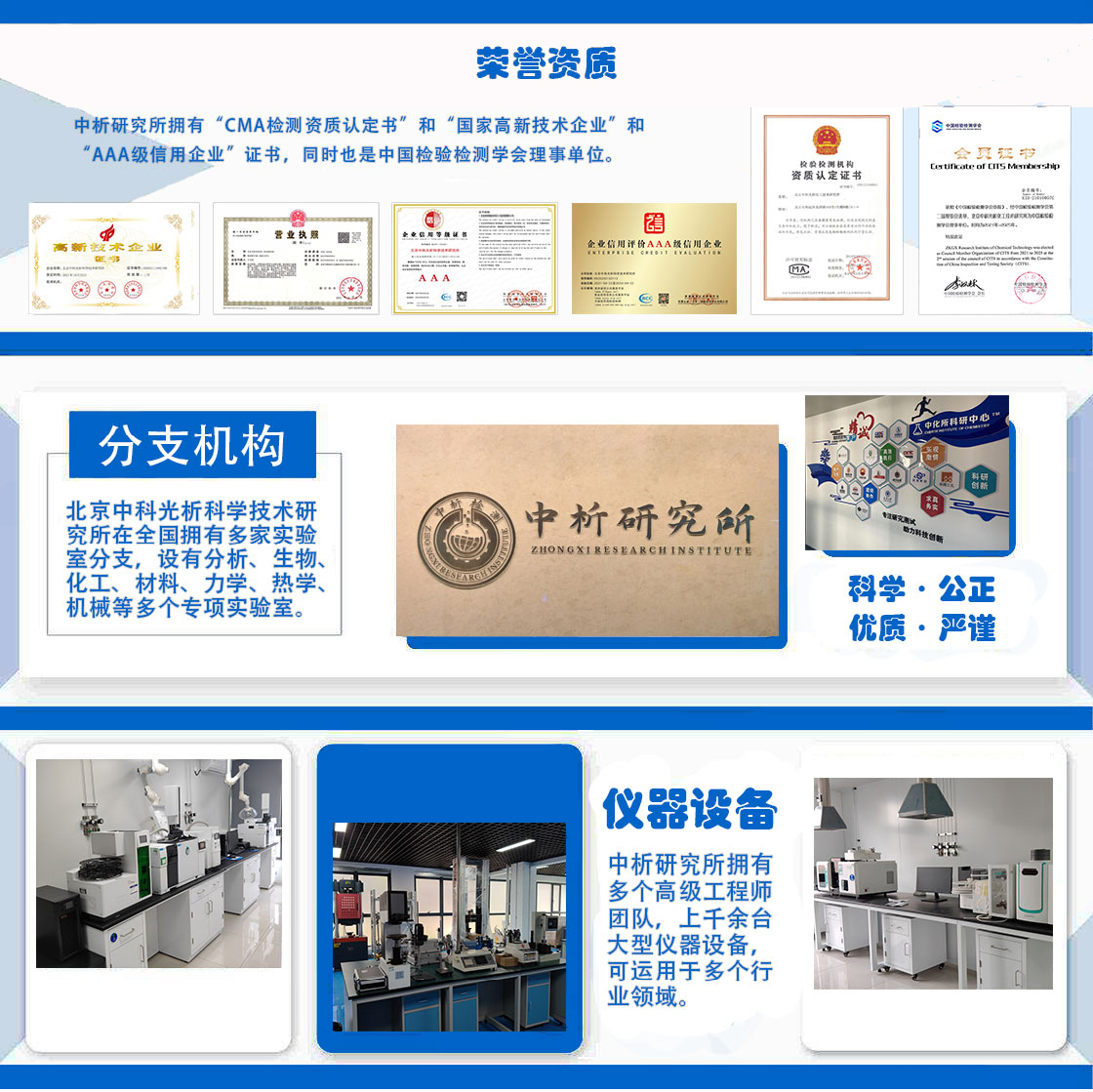
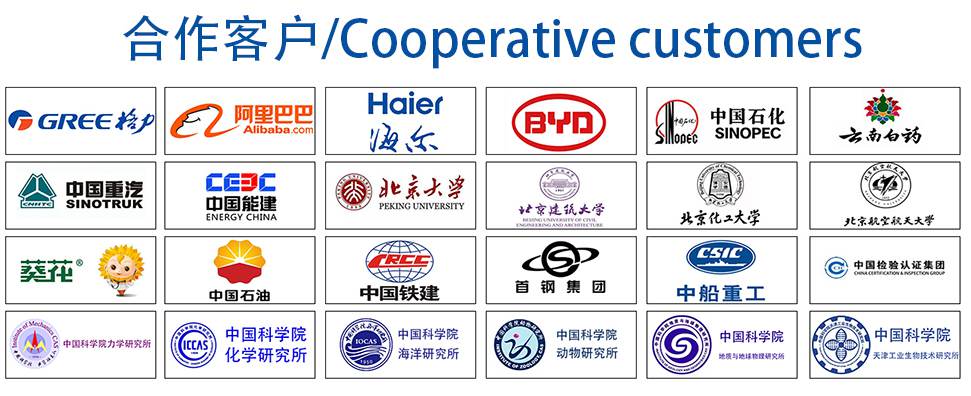