埋地钢质管道液体环氧外防腐层检测的重要性
埋地钢质管道作为石油、天然气、水务等工业领域的重要运输载体,长期处于土壤、地下水、微生物及化学介质的复杂腐蚀环境中。液体环氧外防腐层作为管道的第一道防护屏障,其完整性直接关系到管道的使用寿命和运行安全。然而,由于施工工艺、材料老化、机械损伤或环境侵蚀等因素,防腐层可能出现厚度不足、针孔、剥离或开裂等缺陷。因此,定期开展防腐层检测是评估管道健康状况、预防泄漏事故、延长服役周期的关键措施。通过科学检测,能够精准定位隐患区域,为维修决策提供数据支撑,从而降低运营风险和经济损失。
主要检测项目及方法
1. 防腐层外观与厚度检测
外观检查是基础项目,通过目视或辅助工具观察防腐层表面是否平整、有无气泡、流挂、裂纹等缺陷。厚度检测通常采用磁性测厚仪或超声波测厚仪,依据标准(如GB/T 4956)多点测量,确保涂层厚度符合设计要求(一般≥400μm)。局部过薄或超厚区域需标记并分析原因。
2. 针孔与连续性检测
利用电火花检测仪(高压直流或低频交流)对防腐层进行全覆盖扫描。当探刷经过针孔或破损点时,仪器会通过电弧击穿空气产生报警信号。检测电压根据涂层厚度设定(通常1-5kV),遵循标准如SY/T 0063,确保微小缺陷(直径≥0.5mm)的有效检出。
3. 附着力测试
通过拉拔法或划格法评估涂层与钢基体的结合强度。拉拔法使用专用胶粘剂将测试头固定在涂层表面,通过拉力机测量剥离强度(标准要求≥5MPa);划格法则用刀具划出网格,观察涂层脱落情况。附着力不足可能导致涂层剥离,加速局部腐蚀。
4. 阴极剥离试验
模拟管道阴极保护条件下防腐层的抗剥离性能。在试样表面钻孔并施加规定电位(如-1.5V vs CSE),持续28天后测量剥离半径(标准如GB/T 23257要求≤15mm)。此试验可验证涂层在长期阴极极化环境中的稳定性。
5. 耐化学性与老化评价
通过实验室加速老化试验(如盐雾试验、湿热循环)或现场取样分析,检测涂层耐酸碱、耐盐雾及抗紫外线能力。傅里叶红外光谱(FTIR)可分析涂层分子结构变化,评估老化程度。此外,现场开挖段的柔韧性测试(弯曲试验)也能反映涂层抗变形能力。
6. 综合性能评估与数据管理
结合上述检测结果,采用风险矩阵法对防腐层进行分级评估(如低、中、高风险)。利用GIS系统或数字化平台整合检测数据,建立防腐层健康档案,为后续维护计划提供依据。重点缺陷区域需结合管道定位坐标制定修复优先级,实现精准维保。
检测技术的发展趋势
随着技术进步,新型检测手段如脉冲涡流检测(PEC)、分布式光纤传感技术逐渐应用于防腐层监测。无人机搭载高清摄像头与热成像仪可快速完成长距离管道的宏观缺陷筛查,而人工智能算法则能对海量检测数据实现自动分析与预警,推动防腐层检测向智能化、高效化方向发展。
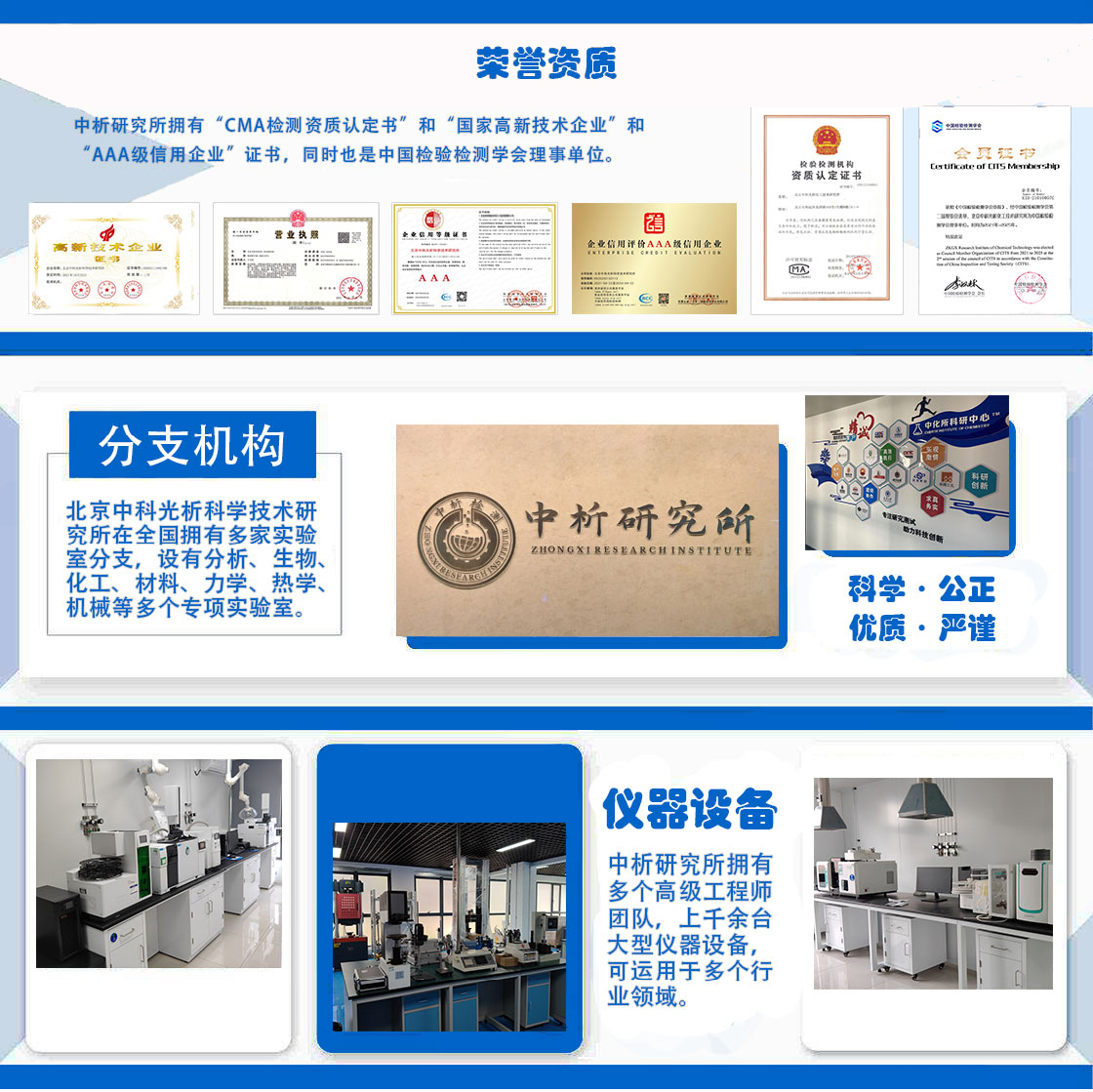
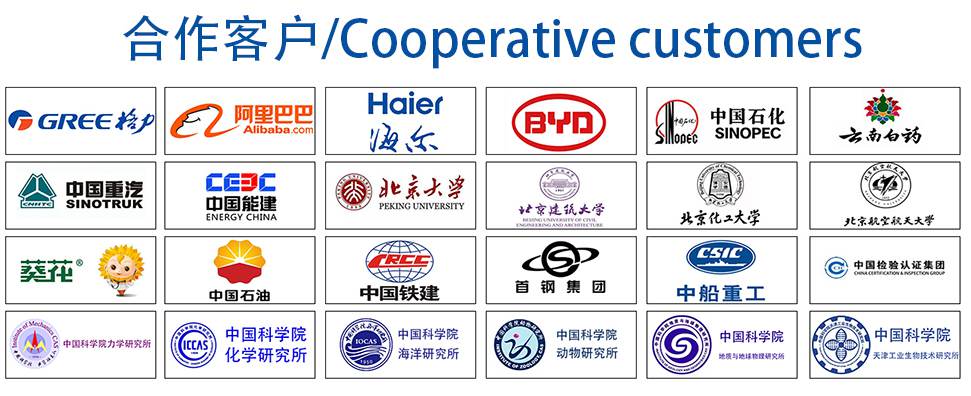