紧固件检测的重要性与核心内容
紧固件作为机械装配中不可或缺的基础元件,包括螺栓、螺母、螺钉、垫片等,其质量直接影响设备安全性和使用寿命。据统计,约30%的机械故障与紧固件失效相关。因此,紧固件检测成为制造业质量控制的关键环节,涵盖原材料、加工工艺、成品性能的全流程验证。通过科学检测,可有效预防松动、断裂、腐蚀等问题,保障航空航天、汽车制造、建筑工程等领域的安全运行。
核心检测项目解析
1. 外观与尺寸检测
通过目视或光学仪器检查表面缺陷(裂纹、毛刺、划痕等),使用卡尺、螺纹规、投影仪测量关键尺寸(直径、长度、螺距、螺纹角度)。符合GB/T 90.1-2015等标准要求,确保装配兼容性。
2. 力学性能检测
包含拉伸试验(屈服强度、抗拉强度)、硬度测试(洛氏/维氏硬度)、抗剪切强度试验等。例如按ISO 898-1标准,8.8级螺栓需达到800MPa以上的抗拉强度。测试设备包括万能试验机、冲击试验机。
3. 耐腐蚀性能检测
采用盐雾试验(ASTM B117)模拟海洋环境,或湿热试验评估镀层(镀锌、达克罗)保护效果。高腐蚀环境下使用的紧固件需达到720小时无红锈的盐雾测试标准。
4. 化学成分分析
使用光谱仪对材料进行元素检测,验证碳钢、不锈钢或钛合金的组分是否符合SAE J429、ASTM A193等规范,例如304不锈钢需含18%-20%铬、8%-10.5%镍。
5. 扭矩与预紧力测试
通过扭矩试验机模拟实际装配工况,测定摩擦系数和预紧力衰减率,验证防松性能。按VDI 2230标准,需确保紧固件在振动环境下保持80%以上的初始预紧力。
6. 无损检测(NDT)
采用磁粉探伤(表面裂纹)、超声波探伤(内部缺陷)、X射线检测(铸造件气孔)等技术,适用于高安全性要求的核电、高铁等领域紧固件。
检测标准体系与技术创新
国内外主要依据ISO、ASTM、DIN、GB等标准体系,智能化检测设备(如AI视觉分选系统、在线扭矩监控装置)的应用显著提升了检测效率和精度。未来趋势将向自动化、大数据质量追溯方向深度发展。
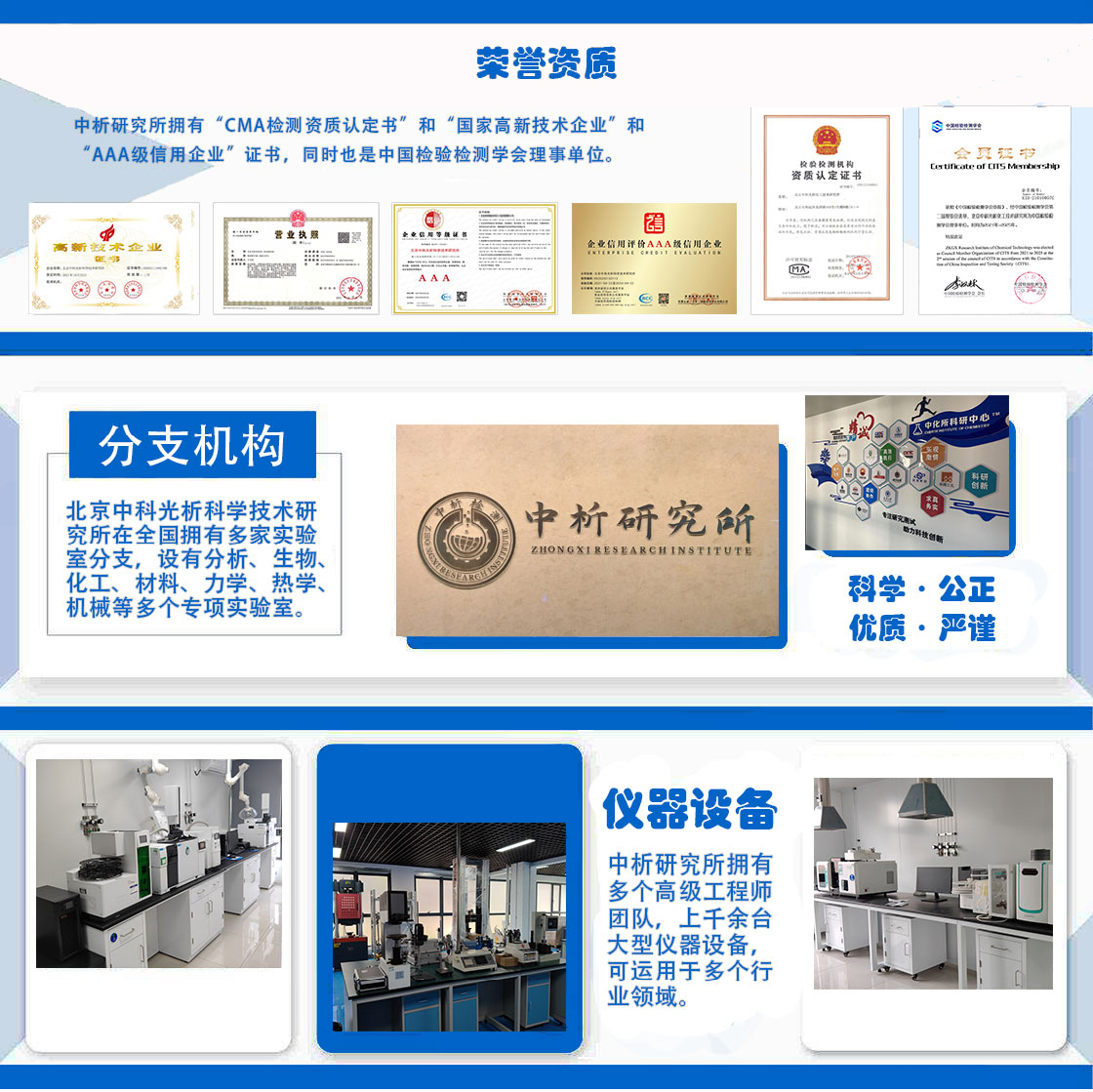
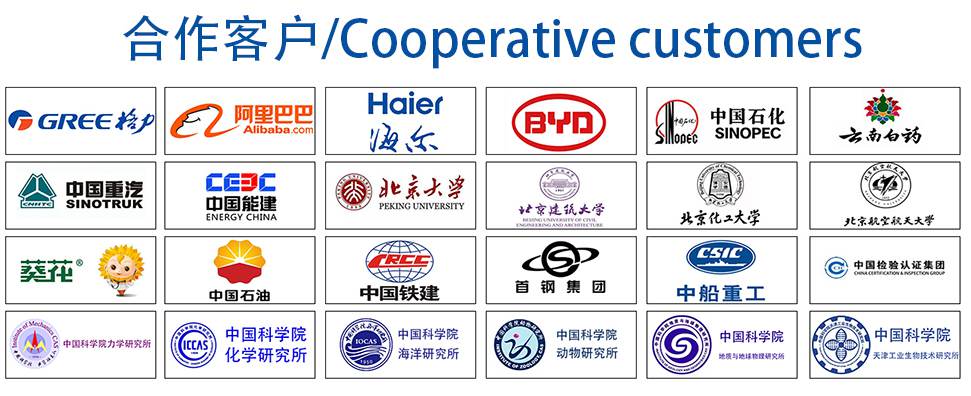