游车钻柱运动补偿器检测概述
游车钻柱运动补偿器(Heave Compensator)作为海洋钻采装备的核心组件,主要用于抵消波浪引起的平台垂荡运动对钻柱的冲击,保障钻井作业的安全性和连续性。其性能直接关系到深水钻井效率、设备寿命及人员安全。由于长期承受高压、高频振动和复杂工况,补偿器易出现机械疲劳、液压泄漏、传感器失效等问题。因此,定期开展系统性检测是预防故障、延长设备使用寿命的关键环节。检测需围绕结构完整性、动态响应、液压系统稳定性等多维度展开,并严格遵循API 16F、DNVGL-OS-E101等行业标准。
核心检测项目与技术要求
1. 结构完整性检测
通过目视检查、超声波探伤(UT)和磁粉检测(MT)评估补偿器本体、连接法兰及关键焊缝是否存在裂纹、腐蚀或变形。重点关注高压缸体壁厚变化(允许误差±0.5mm)、活塞杆表面硬度(需达到HRC55-60)以及密封槽几何精度(平面度≤0.02mm)。
2. 液压系统检测
使用压力传感器和流量计测试液压泵站输出稳定性,要求压力波动范围≤±2%额定值(通常35MPa级)。检查蓄能器预充压力是否符合设计值(氮气预充压力为系统压力的80%-90%),并对比例阀、伺服阀进行阶跃响应测试,动作延迟应小于50ms。
3. 运动补偿性能测试
在模拟波浪工况下,通过位移传感器(精度0.1mm)和加速度计(量程±5g)测量补偿器实际行程与理论值的偏差,动态补偿效率需≥85%。同时利用FEA软件分析应力集中区域,验证补偿器在极限载荷(如150%工作载荷)下的结构安全性。
专项功能验证与维护建议
4. 传感器与控制系统校准
对张力传感器、位置编码器进行静态标定与动态验证,线性误差应≤0.5%FS。利用HIL(硬件在环)测试平台验证PLC控制逻辑,确保在急停、过载等异常工况下能触发安全联锁(响应时间<200ms)。
5. 密封与防腐检测 采用氦质谱检漏法检测高压密封件泄漏率(≤1×10⁻⁶ mbar·L/s),对海洋大气腐蚀环境下的部件进行盐雾试验(按ISO 9227标准进行480小时测试),并检查牺牲阳极剩余厚度(需>原始厚度的50%)。
6. 应急制动系统测试
模拟液压动力失效工况,验证机械锁紧装置能否在3秒内完成钻柱固定,制动后钻柱位移量应≤5mm。同时测试备用电源(如超级电容模块)的持续供电能力(需维持关键传感器工作≥30分钟)。
检测周期与数据管理
建议每6个月进行常规检测,每2年开展全面拆检。检测数据需录入设备健康管理系统(PHM),建立补偿器性能退化模型,通过振动频谱分析(FFT)和油液磨粒检测实现预测性维护。对于关键参数(如缸体椭圆度、密封件压缩永久变形率)应建立动态阈值报警机制,偏差超过10%时立即启动检修程序。
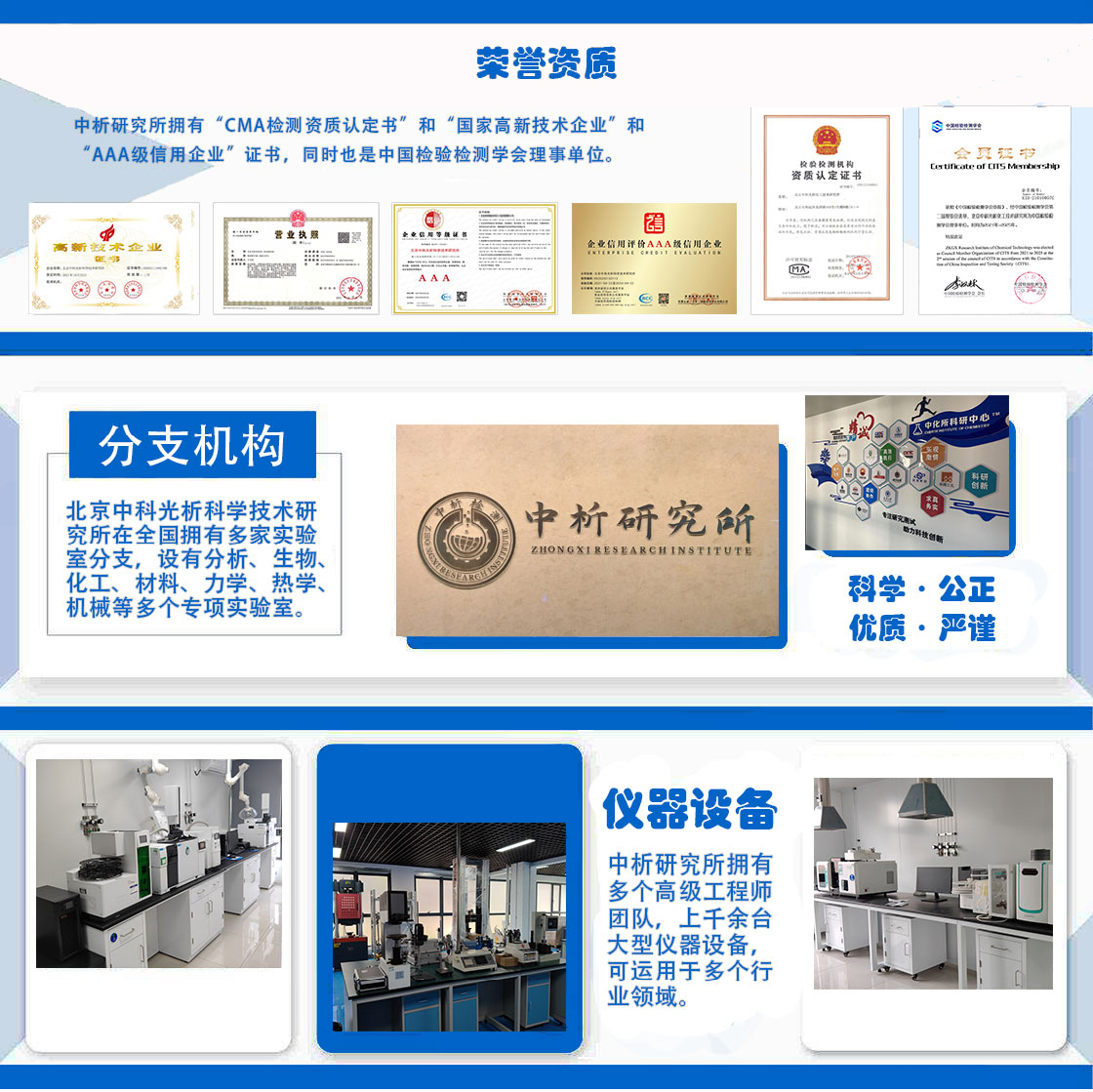
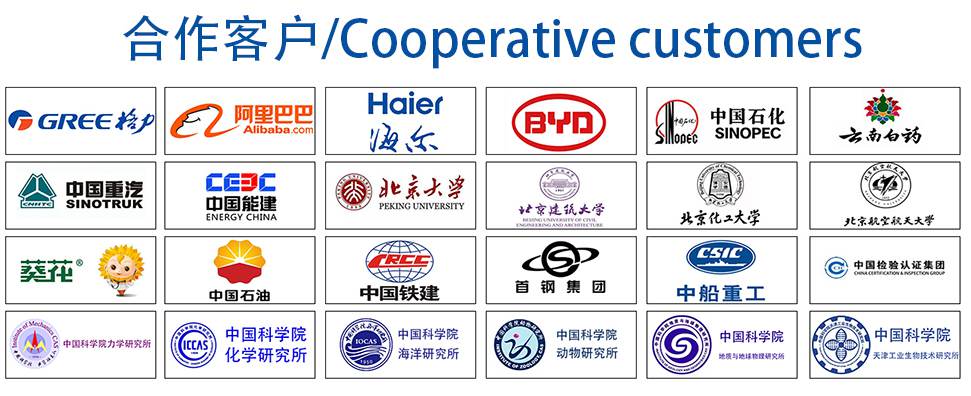