防护阀门检测的重要性与核心项目
防护阀门作为工业管道系统、压力容器及设备中的关键安全部件,承担着压力调节、介质阻断和系统保护的重要作用。其性能的可靠性直接关系到生产安全、设备寿命和环境污染风险。由于阀门长期处于高温、高压、腐蚀或磨损工况下,其密封性、耐压能力及动作灵敏度可能逐渐下降,因此定期开展科学规范的检测至关重要。通过系统性检测,可及时发现阀门潜在故障,避免因泄漏、卡阻或失效引发的安全事故,同时保障工艺流程的稳定性和经济性。
核心检测项目及方法
1. 密封性检测
密封性是阀门功能的核心指标,检测包括内漏和外漏两部分。采用气密性试验或水压试验,通过加压介质观察压力表数值变化,结合目视检查或专用检漏仪器(如超声波检漏仪)判断密封面是否存在缺陷。对于高风险工况阀门,可能需使用氦质谱检漏技术进行高精度检测。
2. 耐压强度检测
验证阀门壳体及连接部位在额定压力或超压条件下的结构完整性。通过在1.5倍设计压力下保压一定时间,观察是否出现变形、裂纹或渗漏现象。此测试需严格遵循ASME B16.34或GB/T 12224等标准要求。
3. 动作性能测试
针对自动控制阀门(如安全阀、调节阀)需验证其启闭灵敏度与重复精度。通过模拟实际工况测试开启/关闭时间、回座压力偏差及动作次数,确保其在紧急状态下能快速响应。对弹簧式安全阀还需测量整定压力与排放能力。
4. 材料腐蚀与磨损评估
使用金相显微镜、硬度计及厚度测量仪分析阀体、阀瓣等关键部件的腐蚀深度、表面裂纹及材料劣化情况。对存在冲蚀磨损的阀门,需结合介质流速与颗粒物含量进行寿命预测。
5. 功能性附件检测
检查执行机构(电动、气动或液动装置)的驱动能力与信号反馈准确性,测试电磁阀、限位开关等辅助元件的联动功能,确保阀门在自动化系统中的协调运行。
检测标准与周期建议
防护阀门的检测需严格依据行业规范,如API 598(阀门检验与试验)、TSG 21《固定式压力容器安全技术监察规程》等。常规检测周期建议为:高风险工况阀门每6-12个月检测一次;一般工况阀门不超过3年。异常工况(如频繁启闭、介质突变)后应立即进行专项检测。
通过上述系统性检测,可显著降低工业系统的运行风险,延长阀门使用寿命,同时满足安全生产法规要求。企业应建立阀门全生命周期管理档案,结合智能监测技术实现预测性维护,全面提升安全管控水平。
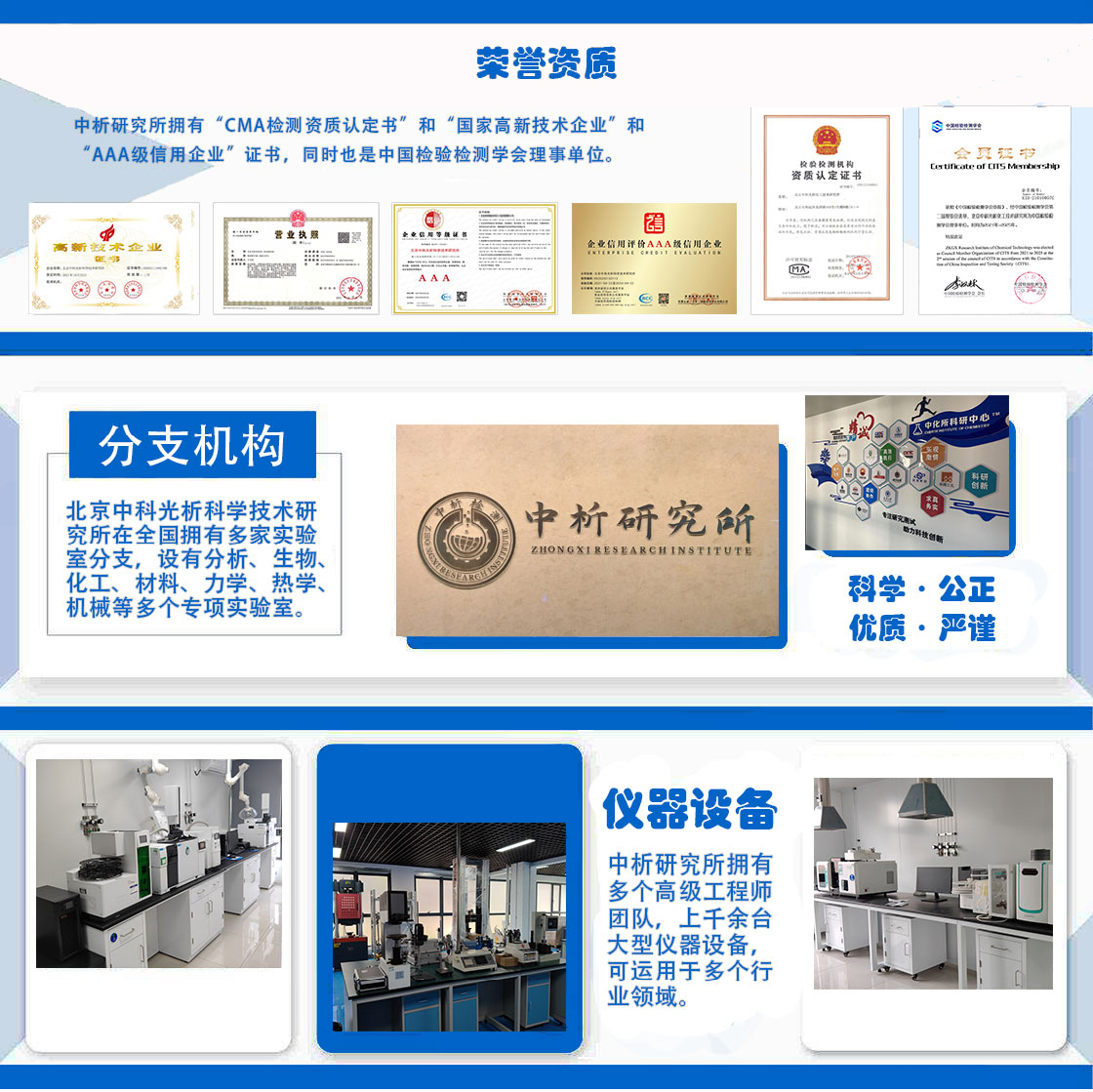
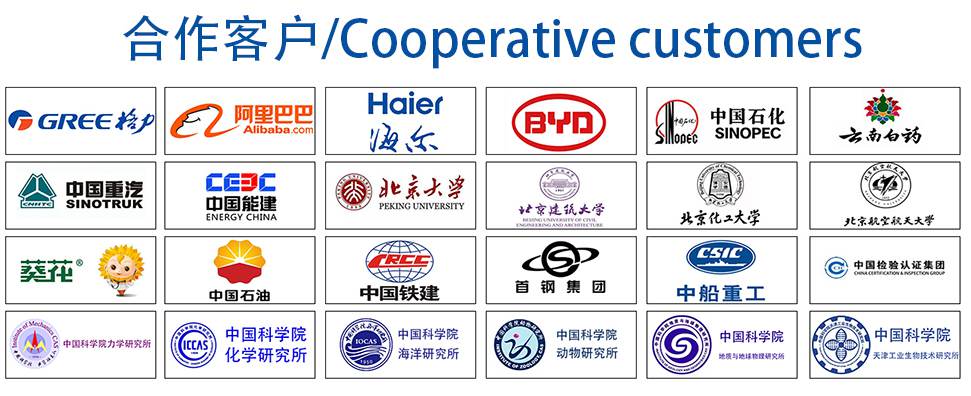