焊接接头检测的重要性与常见检测项目
焊接接头作为工程结构中承载应力的关键区域,其质量直接关系到设备的安全性、可靠性和使用寿命。随着工业制造技术的快速发展,焊接工艺被广泛应用于压力容器、管道系统、桥梁建筑及航空航天等领域。然而,焊接过程中可能产生的气孔、裂纹、未熔合等缺陷,以及热影响区的组织变化,都可能成为结构失效的隐患。因此,通过科学的检测手段对焊接接头进行全面评估,已成为现代工程质量控制中不可或缺的环节。
1. 外观检查
外观检查是焊接接头检测的首道工序,通过目视或低倍放大镜观察焊缝表面质量。主要检测焊道成形是否规整、余高是否符合标准、是否存在咬边、焊瘤、表面裂纹等明显缺陷。同时检查焊缝与母材的过渡区域是否平滑,确保无明显的错位或凹陷。根据GB/T 6417标准,需记录表面缺陷的位置、尺寸和形态,为后续深入检测提供依据。
2. 无损检测技术
无损检测(NDT)是核心检测手段,主要包括:
渗透检测(PT):利用毛细作用原理检测表面开口缺陷,适用于非多孔性材料;
磁粉检测(MT):通过磁场分布变化发现铁磁性材料表面及近表面缺陷;
射线检测(RT):采用X射线或γ射线透视焊缝内部,可清晰显示气孔、夹渣等立体缺陷;
超声波检测(UT):通过声波反射信号定位内部缺陷的深度和大小,特别适用于厚壁构件检测;
相控阵超声(PAUT):最新技术可实现多角度扫查和三维成像,显著提升检测精度。
3. 力学性能测试
通过取样试验验证接头的机械强度:
- 拉伸试验测定抗拉强度和屈服强度
- 弯曲试验评估接头塑性和结合质量
- 冲击试验检测低温环境下的韧性表现
- 硬度测试分析热影响区硬化程度
试验结果需符合ASME IX或ISO 15614等标准要求。
4. 金相分析
通过切割试样进行微观组织观察,主要分析:
- 焊缝金属的柱状晶形态
- 热影响区的晶粒尺寸变化
- 是否存在魏氏组织、马氏体脆化等异常结构
- 熔合线区域的结合完整性
金相检测可揭示焊接工艺参数是否合理,为工艺优化提供依据。
5. 其他专项检测
针对特殊工况需求可能进行:
- 化学成分光谱分析
- 耐腐蚀性能盐雾试验
- 高温蠕变性能测试
- 疲劳寿命评估
- 密封性水压/气压试验
6. 数字化检测技术发展
随着工业4.0的推进,TOFD衍射时差法、激光超声、红外热成像等新技术逐步应用。基于大数据的智能判定系统和数字孪生技术,正在实现检测数据的实时分析和寿命预测,推动焊接质量控制向智能化、精准化方向发展。
焊接接头检测需要根据材料特性、服役环境和技术规范选择检测组合方案。只有建立从原材料、焊接工艺到成品检测的全流程质量体系,才能确保焊接结构的安全运行。
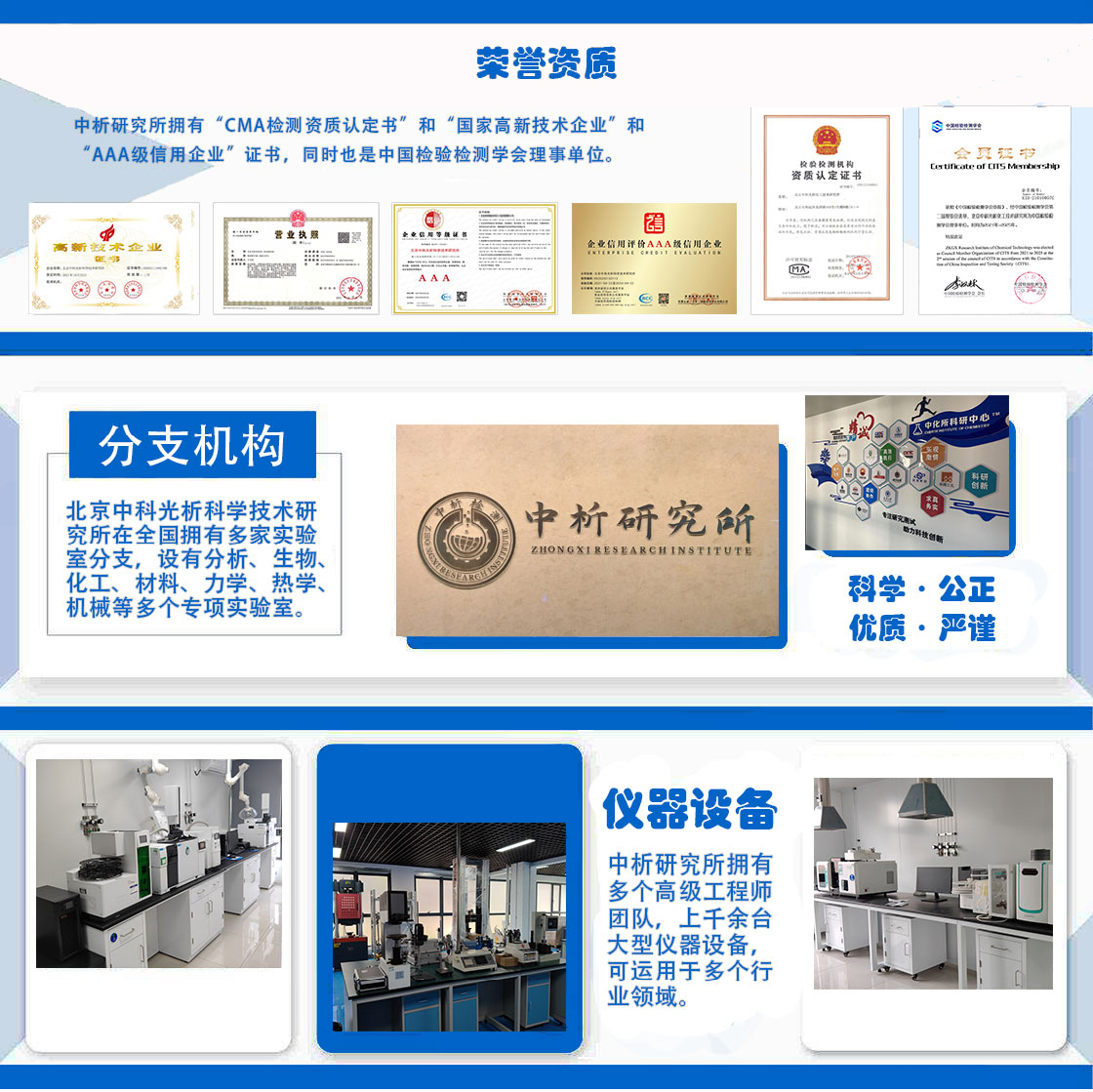
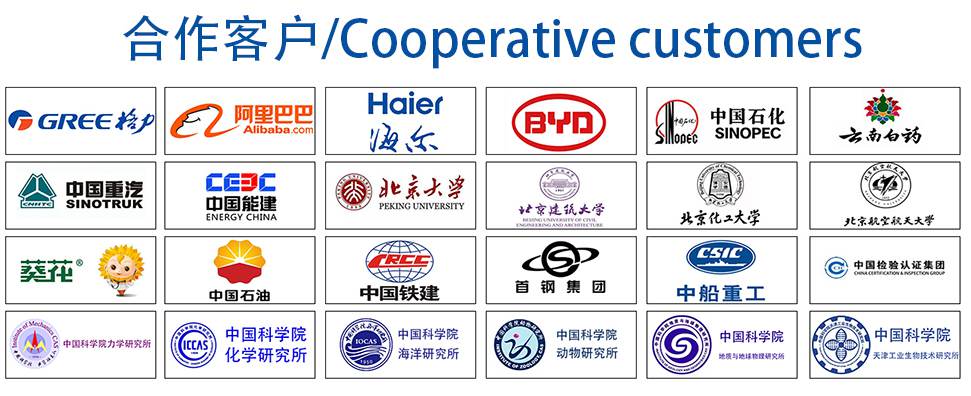