钢质管道熔结环氧粉末外涂层检测的重要性
钢质管道作为石油、天然气、化工等领域输送介质的核心载体,其使用寿命和安全性直接关系到能源运输系统的稳定运行。熔结环氧粉末(FBE)外涂层因其优异的防腐性能、附着力及耐化学腐蚀能力,被广泛应用于管道外防腐工程。然而,涂层在施工、运输及服役过程中可能因工艺缺陷、机械损伤或环境侵蚀导致性能下降。因此,针对FBE外涂层的系统化检测是保障管道完整性、延长服役寿命的关键环节。通过科学的检测手段,可及时发现涂层缺陷,评估其防护效能,为管道的维护、修复及寿命预测提供数据支持。
检测项目及技术要求
1. 涂层厚度检测
涂层厚度是评价防腐性能的基础指标。依据标准(如ISO 21809-2、SY/T 0315),采用磁性测厚仪或超声波测厚仪对管道表面进行多点测量。检测时需覆盖焊缝、弯头等关键区域,确保厚度均匀性符合设计要求。单点最小厚度不应低于规定值的80%,平均厚度需满足标准范围(通常为300-500μm)。
2. 涂层附着力测试
通过划格法或拉拔法评估涂层与钢基体的结合强度。划格法使用专用刀具在涂层表面划出1mm×1mm方格,观察涂层剥离情况;拉拔法则采用液压或机械装置垂直施加载荷,直至涂层脱离基材。附着力等级需达到ISO 2409标准的2级及以上,或拉拔强度不低于5MPa。
3. 针孔(漏点)检测
利用电火花检漏仪对涂层进行全表面扫描,检测电压根据涂层厚度设定(通常为3-5kV/mm)。当涂层存在针孔或裂纹时,仪器将发出报警信号并记录缺陷位置。要求检测漏点密度≤3个/㎡,单个漏点直径不超过1mm。
4. 抗冲击性能测试
模拟管道运输及回填过程中的机械冲击,采用落锤试验法(如ASTM G14)。测试时设定冲击能量(如10J),观察涂层是否开裂或剥离。合格标准为冲击后无可见裂纹,且漏点检测无新增缺陷。
5. 耐化学腐蚀性检测
通过浸泡试验或盐雾试验评估涂层耐介质侵蚀能力。将试样浸入特定浓度酸、碱或盐溶液中(如10% H₂SO₄、5% NaCl),持续一定时间后检查涂层是否起泡、脱落。依据NACE TM0174标准,要求涂层在72h内无明显劣化现象。
6. 耐阴极剥离性能测试
模拟管道阴极保护条件下的涂层性能,按ASTM G8或GB/T 23257标准进行。在涂层表面预制人工缺陷,施加1.5V电压并浸泡于电解液中28天,测量剥离半径。合格标准为剥离距离≤8mm,且边缘无分层或鼓包。
7. 外观质量与均匀性检验
目视检查涂层表面是否光滑平整,无流挂、橘皮、气泡等缺陷。结合色差仪和光泽度仪,量化评价涂层颜色一致性与光泽度(通常要求光泽度≥60%)。对于补口区域,需重点检查搭接处密封性及涂层连续性。
8. 综合性能评估与报告
整合各项检测数据,结合施工工艺、环境条件等参数,采用风险矩阵法评估涂层的整体防护等级。检测报告需包含检测方法、设备参数、缺陷分布图及修复建议,为后续工程验收或运维决策提供依据。
结语
钢质管道FBE外涂层的系统性检测是保障能源运输安全的核心技术手段。通过多维度的检测项目组合,能够精准识别涂层缺陷、量化性能指标,从而降低管道腐蚀风险、延长使用寿命。未来,随着智能检测技术(如无人机巡检、AI图像识别)的普及,涂层检测将向高效化、数字化方向持续发展。
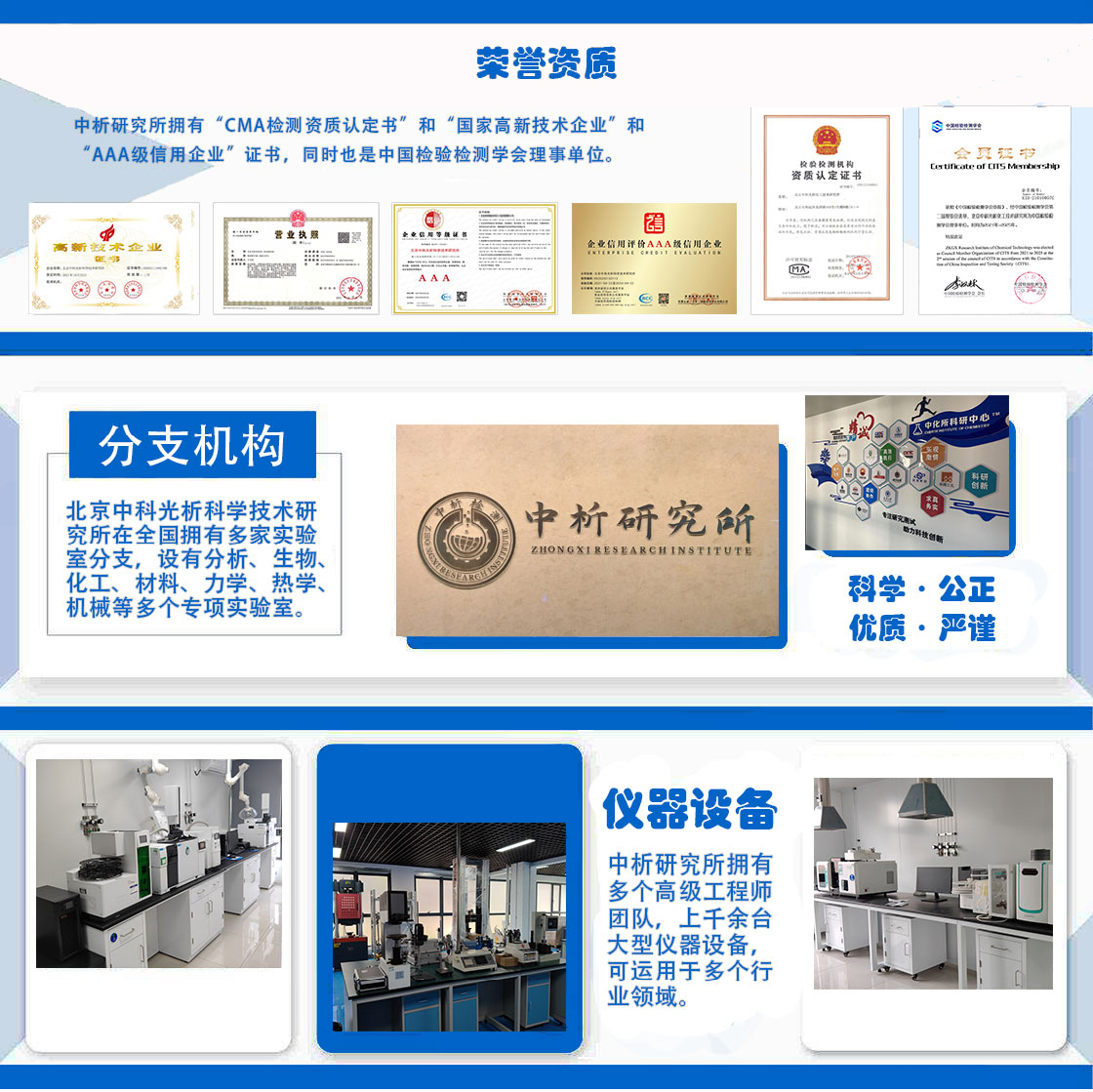
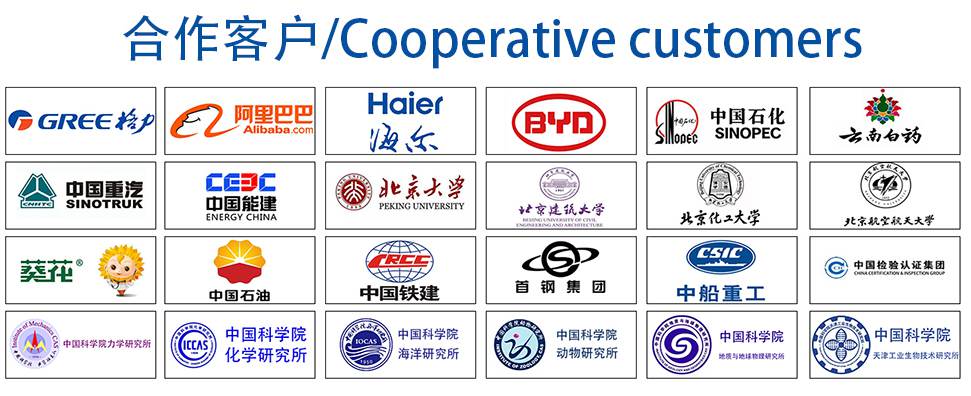