橡胶密封圈检测:确保工业密封性能的关键环节
橡胶密封圈作为工业设备、汽车制造、航空航天等领域中不可或缺的密封元件,其性能直接影响设备的安全性、使用寿命和运行效率。随着应用场景的复杂化,橡胶密封圈需在高温、高压、腐蚀性介质等极端条件下保持稳定密封。因此,建立科学的检测体系对密封圈的物理性能、化学稳定性及耐久性进行全面评估,成为保障产品质量的核心环节。从原材料选择到成品出厂,检测项目覆盖尺寸精度、力学特性、耐环境老化能力等多维度指标,确保密封圈满足ISO 3601、ASTM D2000等行业标准要求。
核心检测项目及方法解析
1. 物理性能检测
包括尺寸公差测量(内径、线径、圆度)、硬度测试(邵氏A型硬度计)、拉伸强度/断裂伸长率(万能材料试验机)、压缩永久变形率(高温压缩装置)等。其中压缩永久变形率是衡量密封圈弹性恢复能力的关键指标,直接影响长期密封效果。
2. 耐化学介质性能检测
通过浸泡法模拟橡胶在不同油类、酸碱溶液、溶剂中的体积变化率和硬度变化,评估材料的耐介质腐蚀能力。例如液压油相容性测试需参照GB/T 1690标准,检测时长通常为70小时至168小时。
3. 热老化与耐候性检测
热空气老化试验(70°C-150°C,48-168小时)用于验证高温环境下密封圈性能衰减情况,紫外线老化箱则模拟户外光照条件下的材料劣化趋势,评估龟裂、硬化等缺陷发生概率。
4. 低温性能测试
采用低温脆性试验机检测密封圈在-40°C至-70°C环境中的柔韧性,TR试验(温度回缩测试)可量化材料低温收缩后的恢复性能,避免极端寒冷工况下的密封失效。
5. 动态密封性能验证
通过旋转密封试验台模拟实际工作状态,连续监测密封圈在交变压力、转速下的泄漏量及磨损情况,并结合有限元分析优化密封结构设计。
行业标准与质量控制体系
橡胶密封圈检测需严格执行ISO 3601-1(流体动力系统密封件)、GB/T 3452.1(液压气动用O形圈)等标准。企业应建立从原料入库(橡胶门尼黏度、硫化曲线检测)到过程控制(模压硫化参数监控)、成品全检(100%气密性测试)的完整质控链,同时配合第三方实验室开展周期性型式试验,确保产品符合UL、FDA等特殊领域认证要求。
结语
随着智能制造技术的升级,橡胶密封圈检测正朝着自动化(机器视觉尺寸检测)、智能化(AI异常数据预警)方向发展。通过多维度的科学检测与持续工艺优化,可显著提升密封圈在新能源、半导体等高端产业的适配性,为工业设备安全运行提供可靠保障。
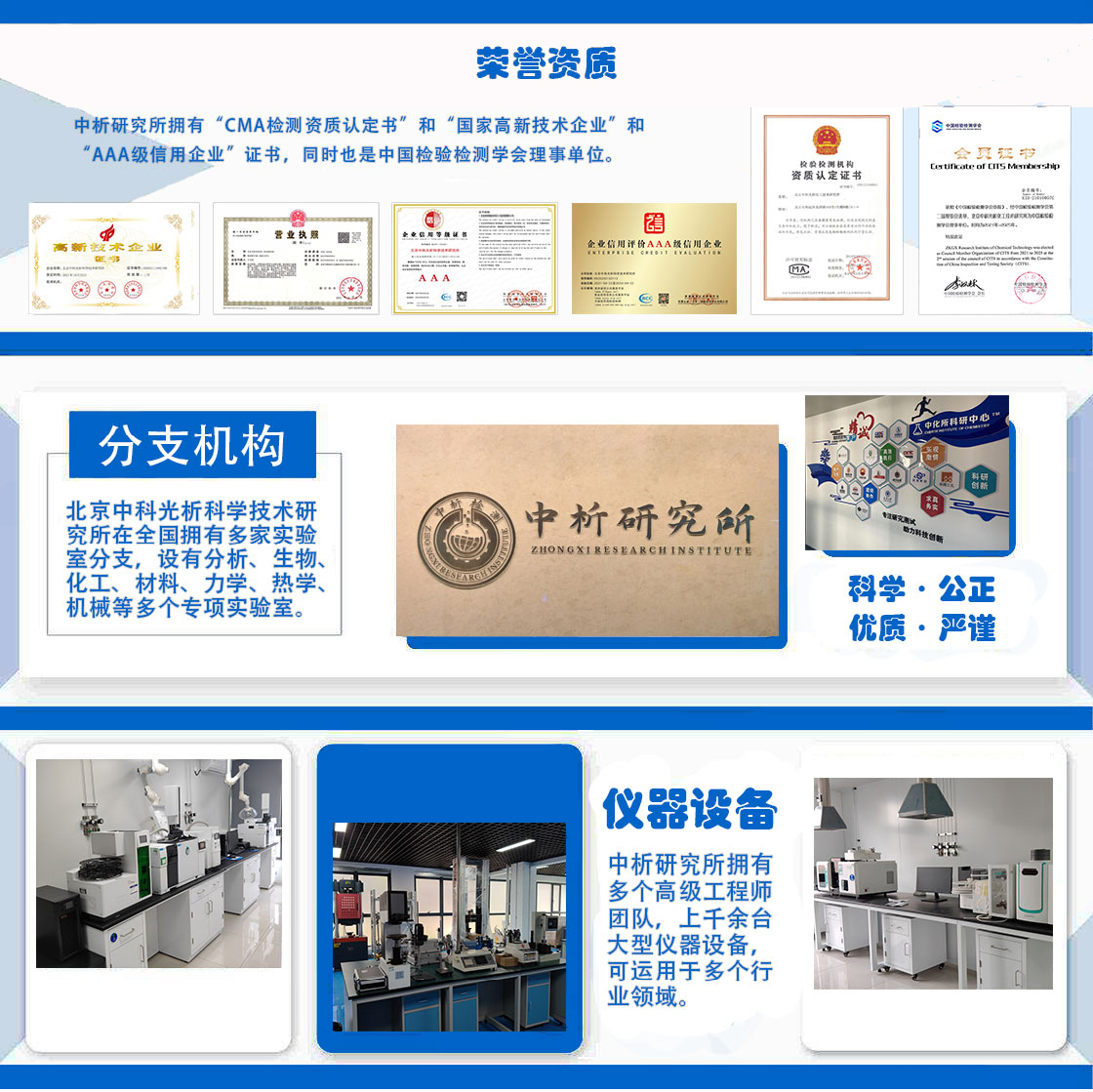
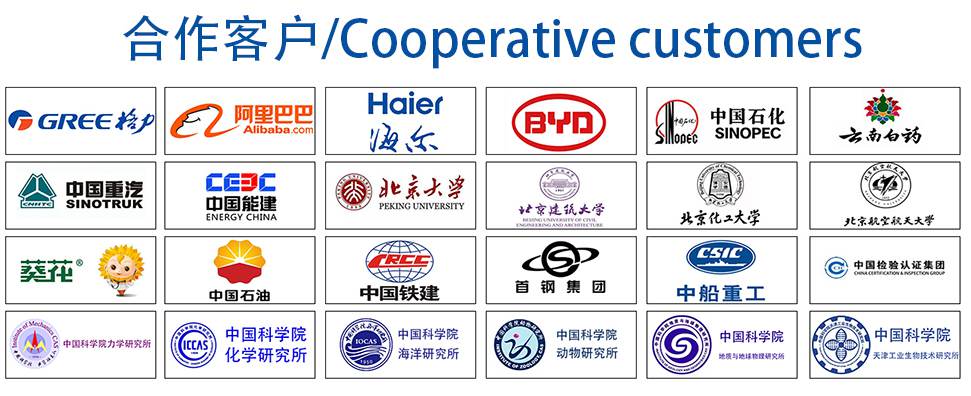