工业机器人检测项目解析:关键技术与应用价值
随着智能制造时代的加速到来,工业机器人已广泛应用于汽车制造、3C电子、食品加工等领域。作为现代工厂的"核心劳动力",机器人系统运行的精度、稳定性和安全性直接关系到生产效率和产品质量。据国际机器人联合会(IFR)数据显示,2022年工业机器人安装量突破51.7万台,但仍有23%的企业因机器人性能问题导致产线停摆。这凸显了工业机器人检测作为质量保障体系的重要性,通过系统化检测可有效预防设备故障,延长使用寿命,降低维护成本达40%以上。
核心检测维度与技术方案
现代工业机器人检测体系包含五大关键模块:
1. 运动精度检测
采用激光跟踪仪配合六维力传感器,对重复定位精度进行μm级测量。依据ISO 9283标准,在负载状态下检测TCP(工具中心点)的空间轨迹偏差。某汽车焊装线实测显示,经过校准的机器人焊接轨迹误差从±0.15mm降至±0.03mm。
2. 动态性能测试
通过多普勒振动分析仪和高速摄像系统,捕捉机械臂在最大加速度下的振动频谱。某SCARA机器人经谐波减速器振动检测,发现200Hz异常谐波,及时更换减速器齿轮避免批量质量事故。
3. 安全功能验证
基于IEC 61508安全标准,对急停响应时间、碰撞检测灵敏度进行测试。某协作机器人通过三维力觉传感器阵列验证,在接触力超过150N时可在0.1秒内完成急停。
4. 环境适应性检测
在温湿度综合试验箱中模拟-20℃至60℃极限工况,检测密封件的耐候性能。某食品行业码垛机器人经72小时盐雾测试后,腕部轴承防护等级从IP54提升至IP67。
5. 通信与软件测试
使用PROFINET/EtherCAT协议分析仪,验证控制系统的实时响应性能。某半导体搬运机器人经总线周期测试,将通讯抖动从±15μs优化至±2μs,提升晶圆传输合格率3个百分点。
检测技术演进与行业实践
当前检测技术正朝着智能化方向发展,基于数字孪生的预测性维护系统已开始应用。某家电企业通过部署振动传感器网络,结合机器学习算法,提前48小时预警减速器故障,减少停机损失280万元/年。第三方检测机构的数据显示,经过系统检测的工业机器人平均无故障时间(MTBF)可达6万小时,较未检测设备提升65%。
随着工业4.0的深入实施,机器人检测已从单一设备检测发展为整线智能诊断。建议企业在选择检测服务时,优先考虑具备CMA/ 资质的机构,并建立全生命周期检测档案,为智能制造转型提供可靠的技术保障。
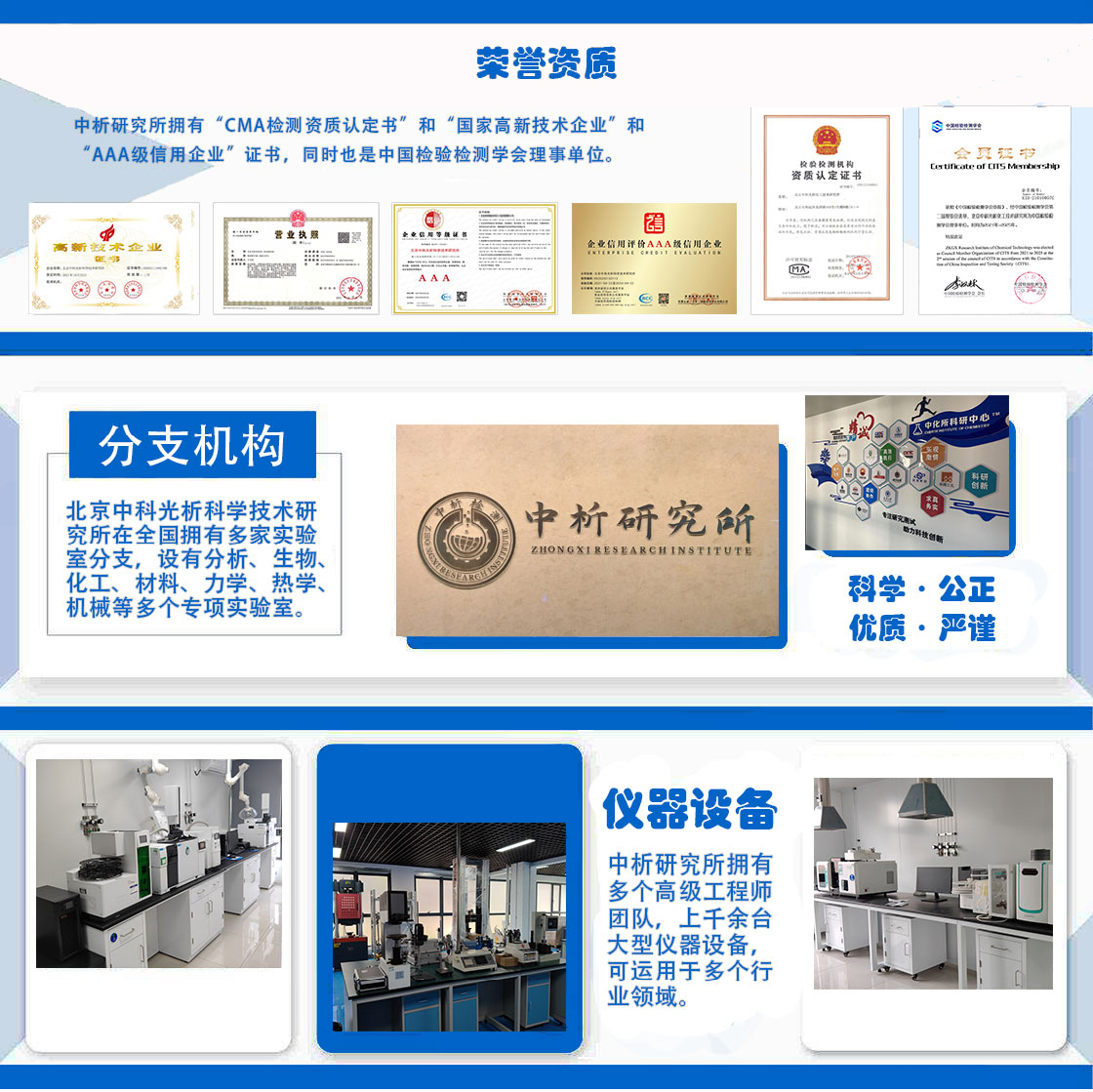
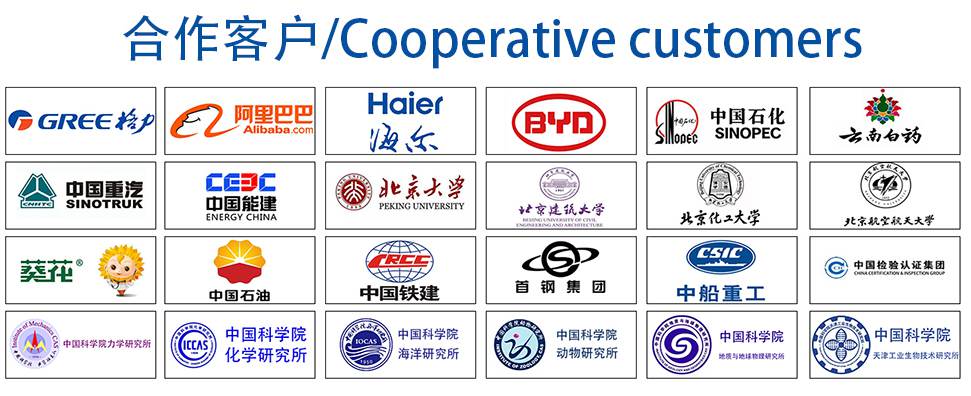