零部件检测:保障产品质量的核心环节
在现代制造业中,零部件检测是确保产品质量和性能稳定的关键环节。从汽车发动机的核心部件到航空设备的精密元件,每个零部件的质量都直接影响最终产品的安全性、可靠性和使用寿命。随着工业4.0的推进,零部件检测已发展成为融合机械工程、材料科学、光学测量和人工智能技术的综合体系,检测精度可达微米级甚至纳米级。严格的检测流程不仅能有效预防产品缺陷,更能为企业降低售后成本、提升品牌信誉度奠定坚实基础。
尺寸精度检测
作为基础检测项目,尺寸精度检测采用三坐标测量机(CMM)、激光扫描仪等高精度设备,对零部件的长度、直径、角度等几何参数进行全方位测量。特别是对于精密传动部件,尺寸偏差需控制在±0.005mm以内,确保装配时的完美配合。现代自动化检测系统可实现每分钟2000个测量点的超高速扫描,并自动生成三维偏差色谱图。
材料性能检测
通过万能材料试验机进行拉伸、压缩、弯曲试验,精确测定材料的抗拉强度(可达2000MPa)、延伸率和弹性模量。硬度检测采用洛氏、维氏、布氏等多种测试方法,涡轮叶片等特殊部件还需进行高温硬度测试(最高1200℃)。金相分析可观察材料微观结构,检测晶粒度(通常要求6-8级)、夹杂物含量等关键指标。
表面缺陷检测
综合运用工业内窥镜(分辨率达4K)、磁粉探伤(检测深度0.1-3mm)和涡流检测技术,可发现微米级裂纹、气孔等缺陷。最新AI视觉系统能自动识别划痕(>0.05mm)、凹坑等32类表面异常,检测速度较人工提升15倍。对于航空部件,需100%进行荧光渗透检测,确保无任何危险缺陷。
装配配合度检测
采用智能化装配检测平台,实时监测过盈配合的压装曲线(压力精度±1%FS),关键轴承位的装配间隙需控制在0.01-0.03mm范围。数字化扭矩测试仪可精确记录螺栓预紧力(误差<±3%),同时监测拧紧角度曲线,防止出现假扭矩现象。对于精密齿轮副,需进行啮合斑点检测,接触面积要求达到75%以上。
功能性动态测试
在模拟工况环境下进行性能验证:液压部件需承受1.5倍额定压力(最高500MPa)的脉冲测试(>100万次循环);旋转部件需通过20%-120%额定转速的振动测试,振幅需<0.05mm。最新NVH测试系统可采集2000Hz以上的异响频谱,结合大数据分析提前预测部件寿命。
检测技术创新发展趋势
随着工业物联网的普及,在线检测系统已实现100%全检覆盖,检测数据实时上传MES系统。X射线CT检测技术(分辨率达1μm)可重构零部件内部三维结构,5G技术使远程专家诊断响应时间缩短至200ms。机器学习算法通过百万级缺陷样本训练,使检测准确率提升至99.98%,推动制造业向零缺陷目标迈进。
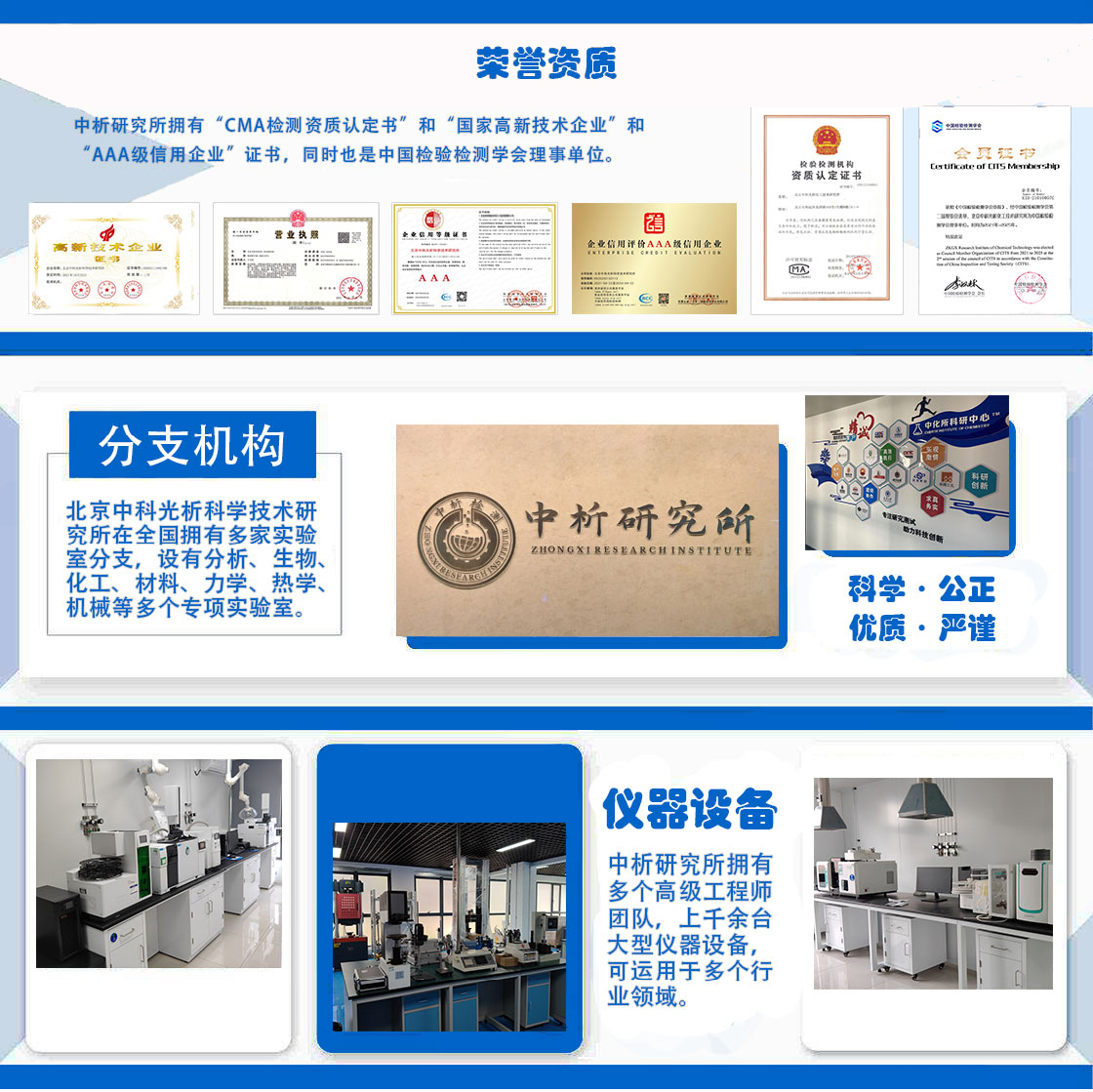
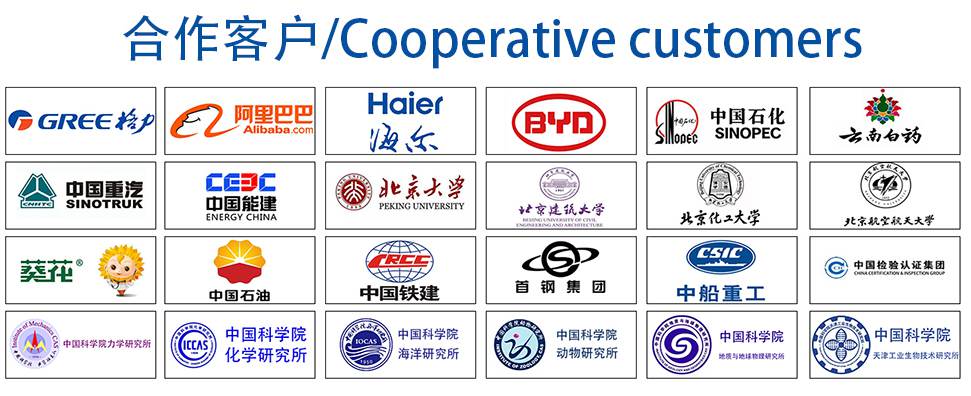