制动钳检测:保障行车安全的核心环节
作为汽车制动系统的核心执行部件,制动钳的检测直接关系到车辆的制动效能与行车安全。在高速行驶、紧急制动等极端工况下,制动钳需要承受超过2000N的夹紧力和600℃以上的瞬间高温,其工作状态直接影响刹车片与制动盘的接触质量。根据国际汽车工程师协会(SAE)统计数据显示,因制动钳失效引发的交通事故占制动系统故障事故的37%,其中75%可通过规范检测提前预防。现代制动钳检测已形成涵盖机械性能、材料特性、装配质量等多维度的完整检测体系,通过精密仪器与标准化流程的结合,确保每个制动钳组件达到毫米级精度和百万次耐久性要求。
外观完整性检测
采用3D视觉扫描系统对制动钳壳体进行100%全检,检测项目包括:表面划痕深度(≤0.05mm)、铸造气孔直径(≤φ1.5mm)、涂层均匀度(色差ΔE≤1.5)。特别关注活塞腔体内壁的加工纹路(Ra0.8-1.6μm),异常纹路可能导致密封件异常磨损。
尺寸精度检测
使用三坐标测量仪(精度0.001mm)对关键尺寸进行检测:安装孔距公差±0.02mm,活塞直径配合间隙0.1-0.3mm,导向销平行度≤0.05mm/100mm。重点控制钳体对称度误差,确保制动力均匀分布。
材质成分分析
通过光谱分析仪验证材料成分:壳体铝合金需满足EN AC-46200标准(Si含量11-13%,Cu≤0.1%),导向销采用40Cr钢(Cr含量0.8-1.1%)。金相检测确认材料热处理状态,确保布氏硬度达到HB90-110。
液压密封性测试
在20MPa测试压力下保压3分钟,泄漏量应<0.5ml/min。动态测试模拟ABS工作状态(压力波动频率15Hz),检测密封圈在10万次循环后的残余变形量(≤0.15mm)。
机械性能试验
使用伺服液压试验机进行:静刚度≥5000N/mm,疲劳寿命≥2×10^6次(载荷幅值±8kN)。异常工况测试包括150℃高温夹持力衰减(≤15%)和-40℃低温回位测试(残余拖滞力<5N)。
装配质量检测
重点检测:防尘罩安装到位率(100%目视确认),消音片贴合间隙(≤0.1mm),螺栓拧紧扭矩控制(M10螺栓35±3N·m)。使用声发射技术检测异常装配应力。
温度场分布测试
红外热成像仪记录连续制动工况(100km/h-0,10次循环)的温度分布,要求:摩擦片区域≤600℃,液压油路区域≤120℃,相邻部件温差梯度<150℃/cm。
动态响应特性检测
在制动模拟试验台上测试:空行程时间≤0.15s,全制动力建立时间≤0.3s。检测压力-位移曲线的线性度(R²≥0.98),异常波动值不超过设定值的5%。
防腐性能评估
进行480小时中性盐雾试验,表面腐蚀面积率≤5%。涂层附着力测试(划格法)达到0级标准,电泳膜厚检测(20-30μm)合格率需100%。
综合性能匹配测试
在整车台架上模拟不同工况:30%坡度驻车保持力衰减≤3%,涉水制动效能恢复时间<2分钟。匹配测试需确保制动力矩波动系数≤8%,避免制动抖动。
通过上述系统的检测流程,现代制动钳的故障率已从传统工艺的0.3%降至0.02%以下。建议每行驶5万公里或2年进行专业检测,关键指标劣化超过初始值15%时应及时更换。智能检测系统的应用使检测效率提升40%,检测数据自动上传云端实现全生命周期管理,为智能网联汽车时代的安全出行提供可靠保障。
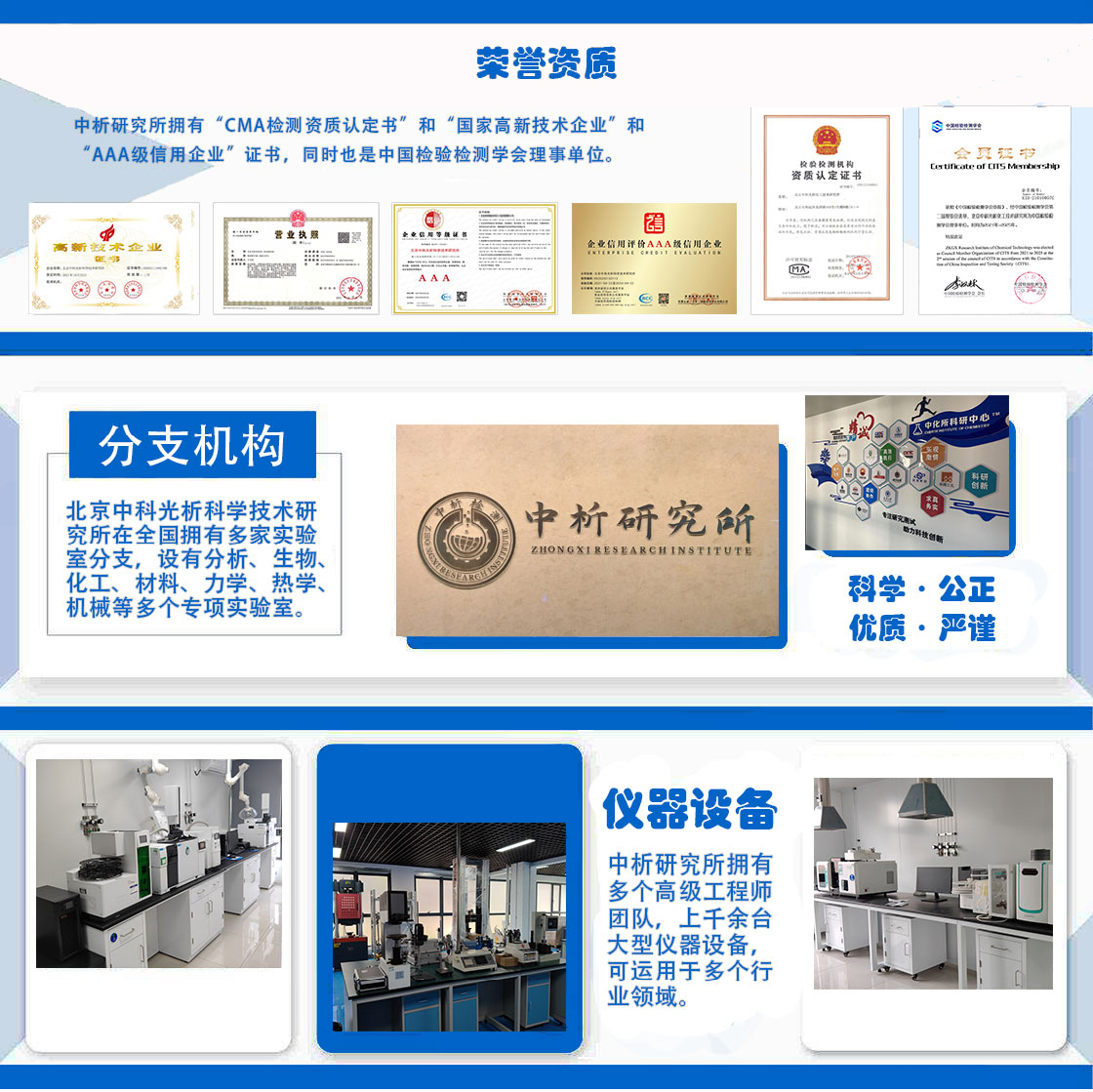
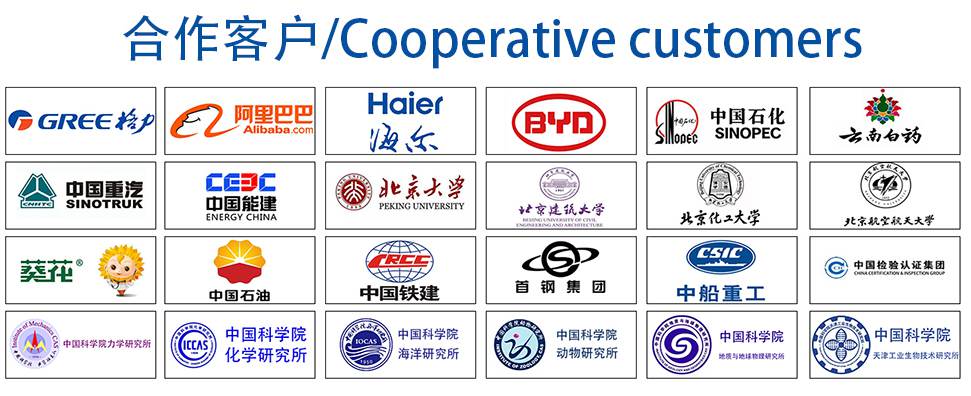