纯电动乘用车用减速器检测的重要性
随着新能源汽车市场的快速发展,纯电动乘用车用减速器作为动力总成的核心部件,承担着将电机高转速转化为车轮驱动扭矩的关键任务。其性能直接影响到整车的动力输出效率、NVH表现及续航里程。由于电动驱动系统具有高转速、大扭矩的工况特性,减速器的结构强度、传动精度和耐久性要求显著高于传统燃油车,因此建立完善的减速器检测体系已成为保障车辆安全性与可靠性的重要技术支撑。
核心检测项目分类与技术要求
1. 传动效率测试
通过专业测功机台架模拟实际工况,精确测量输入/输出轴的扭矩、转速参数,计算各速比下的传动效率值。要求系统效率≥96%(额定工况),瞬时峰值效率需达98%以上。测试需覆盖-40℃至120℃的极端温度环境,验证润滑油温升对传动效率的影响规律。
2. NVH性能检测
采用精密声学测试系统对减速器进行全转速域扫频测试,重点关注齿轮啮合阶次噪声和轴承异响。要求1米处声压级≤72dB(A),振动加速度值控制在0.8m/s²以内。通过模态分析优化箱体结构刚度,消除2000-4000Hz高频啸叫问题。
3. 耐久性试验
执行加速寿命试验,包括:
- 交变负载试验:模拟急加速/能量回收工况,完成10^7次转矩循环
- 高速耐久:维持输入转速8000rpm连续运转1000小时
- 超扭矩试验:施加150%额定扭矩持续30分钟
试验后齿面接触斑需保持≥85%,轴承游隙变化量≤0.02mm。
4. 温升特性测试
构建热管理系统测试平台,监测持续大负荷工况下的油液温升曲线。要求油温稳定值≤110℃,各轴承位温差≤15℃。通过CFD仿真优化散热筋布局,确保冷却流量≥8L/min时的热平衡能力。
5. 密封性能验证
采用氦质谱检漏法检测箱体密封性,泄漏率需<5×10^-7 mbar·L/s。进行1000小时盐雾试验后,观察结合面无腐蚀渗透。动态密封测试模拟涉水工况,验证1m水深浸泡30分钟后的密封有效性。
智能化检测技术发展趋势
当前行业正推进基于数字孪生的虚拟标定技术,通过建立减速器多物理场耦合模型,实现80%以上检测项目的前期虚拟验证。同时应用AI缺陷识别系统,对微观点蚀、剥落等故障的检出率提升至99.2%。在线监测模块可实时采集运行数据,构建寿命预测模型,推动检测体系向预防性维护方向演进。
通过建立涵盖性能、可靠性、环境适应性等维度的系统化检测方案,可显著提升纯电动减速器的品质一致性。未来随着800V高压平台和碳化硅电驱系统的普及,检测标准将进一步提高转速耐受(至20000rpm级)和绝缘性能要求,持续推动新能源汽车核心零部件的技术升级。
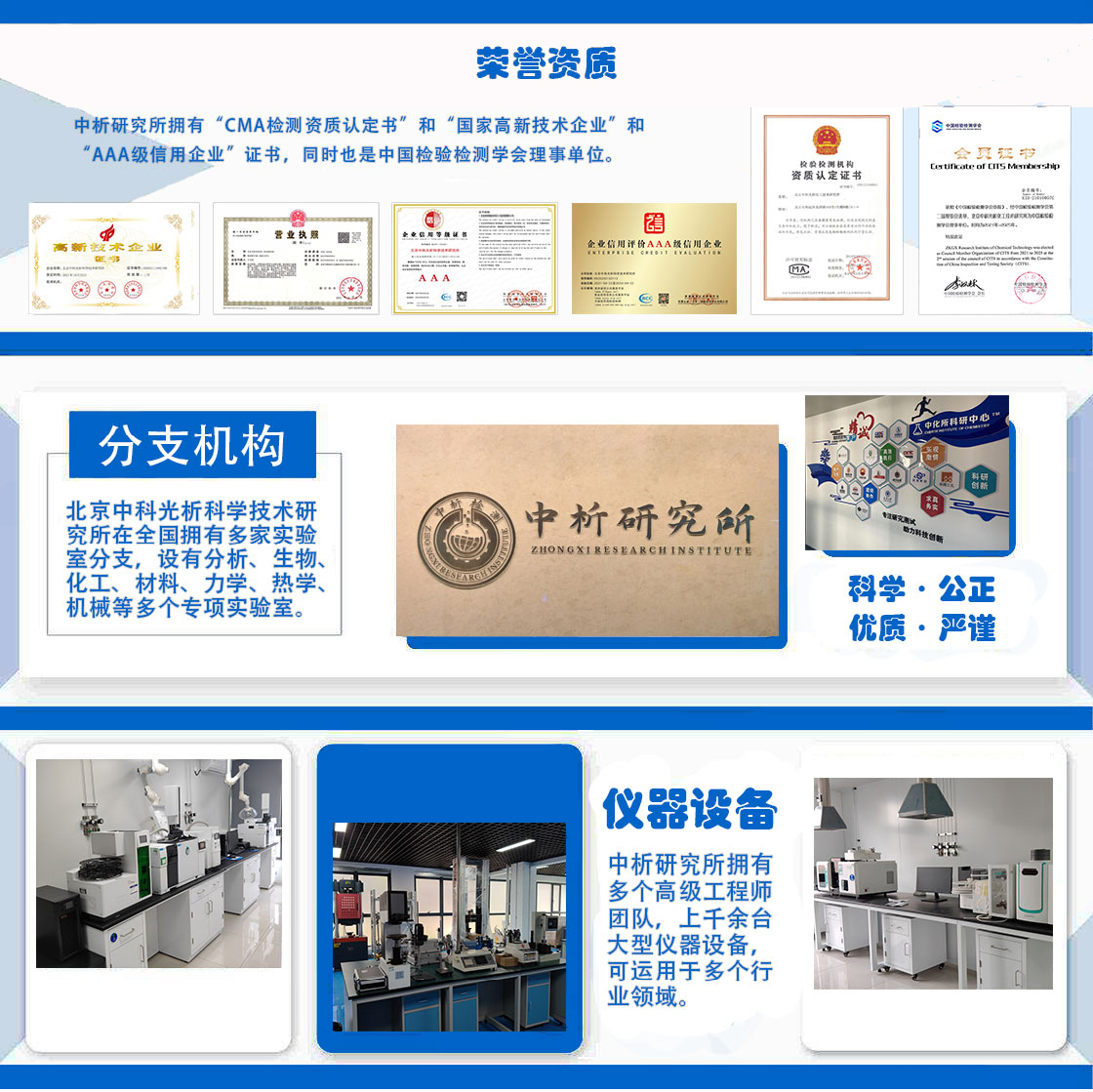
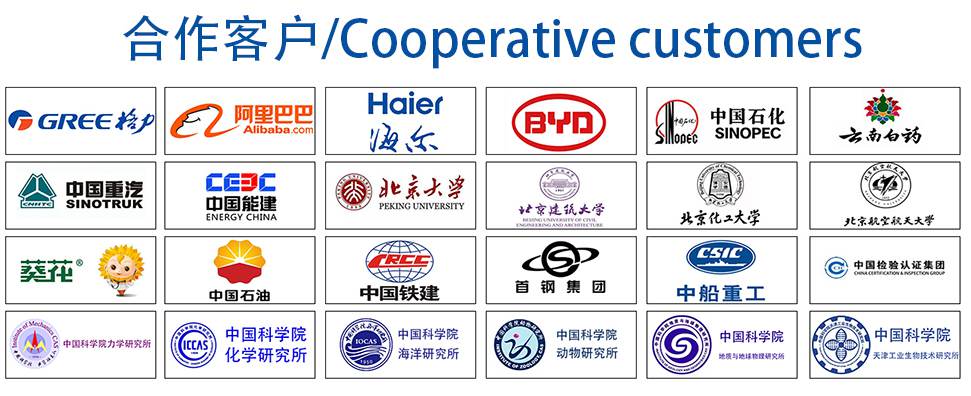