# 粉末的松装密度检测
## 行业背景与核心价值
随着粉末冶金、增材制造及新能源材料行业的快速发展,粉末物性参数的精准检测成为工艺优化的核心环节。据中国粉末冶金协会2024年数据显示,粉末冶金市场规模已突破380亿美元,其中材料性能一致性问题的质量投诉占比达12%。松装密度作为表征粉末流动性与填充特性的关键指标,直接影响3D打印成形精度、药粉压片均匀度及锂电池电极涂布质量。通过建立标准化的松装密度检测体系,企业可降低原料浪费率15%以上(国家新材料测试评价中心,2024),同时为新型复合粉末材料的研发提供数据支撑,推动行业向高精度、低能耗方向转型。
## 技术原理与测量方法
### 粉末松装密度的定义与计算模型
松装密度指粉末在无外力作用下自然填充单位体积的质量,计算公式为ρ= m/V(ρ为密度,m为粉末质量,V为填充体积)。根据ASTM B212标准,测试需在恒温恒湿环境中进行,通过标准漏斗将粉末自由落入25mL量杯,刮平后称重。为提升“粉末流动性评估体系”的准确性,部分高端设备集成激光扫描技术,实时监测填充过程的堆叠形态,修正边缘效应带来的误差。
### 标准化检测流程与质量控制
检测流程分为样品预处理、装置校准、填充操作及数据复核四阶段。以金属3D打印用钛合金粉末为例,需先经60目筛网过筛去除团聚颗粒,随后使用震动频率20Hz的自动填充装置减少人为干扰。据ISO 3923-1:2018要求,平行试验次数不得低于5次,相对标准偏差(RSD)需控制在2%以内。实验室须定期使用NIST标准物质进行设备溯源,确保“增材制造工艺优化”数据的可靠性。
## 行业应用与典型案例
### 制药行业的质量控制革新
在固体制剂生产中,药粉松装密度偏差超过5%会导致压片机模具磨损率上升30%。华北某药企引入全自动松装密度仪后,结合“粉末-模具匹配度分析算法”,将片剂重量差异从±7%优化至±3%,年节约原料成本超800万元。该案例凸显松装密度检测在制药过程控制中的经济价值。
### 新能源电池材料性能提升
针对锂电池正极材料磷酸铁锂的涂布工艺,宁德时代通过建立松装密度与振实密度的关联模型(R²=0.92),实现了电极孔隙率的精准调控。据测算,密度检测数据指导下的电极良品率提升9个百分点,电池循环寿命增加200次以上(《储能材料学报》2024年第3期)。
## 质量保障体系构建
### 三级校验机制与数据追溯
检测体系包含设备级(每日空载测试)、方法级(每周标准样品验证)及体系级(季度第三方审核)。采用区块链技术存储检测数据,确保从原料入库到成品出厂的全周期可追溯。东莞某检测中心通过 认证的松装密度实验室,年出具报告2.3万份,数据复现率达到99.6%。
### 智能化技术赋能检测升级
引入机器视觉系统后,粉末填充过程的边界识别精度提升至0.1mm,结合AI异常值剔除算法,将单次检测时间缩短40%。三一重工依托该技术建立的“粉末特性数据库”,已收录1.2万组工艺参数,支持快速匹配最佳烧结温度曲线。
## 未来发展与建议
随着功能性粉末材料的复杂度提升,传统体积法已难以满足纳米级粉末的检测需求。建议行业重点攻关两项技术:一是开发基于X射线断层扫描的三维密度分布检测设备,二是建立跨区域的“粉末特性共享云平台”。同时,应加快制定针对磁性粉末、超轻金属粉末的专项检测标准,推动检测技术从单一参数向多模态耦合分析演进,为新材料产业高质量发展提供技术底座。
上一篇:数字传输系统,调频系统和无牌照局域网设备检测下一篇:药物相容性检测
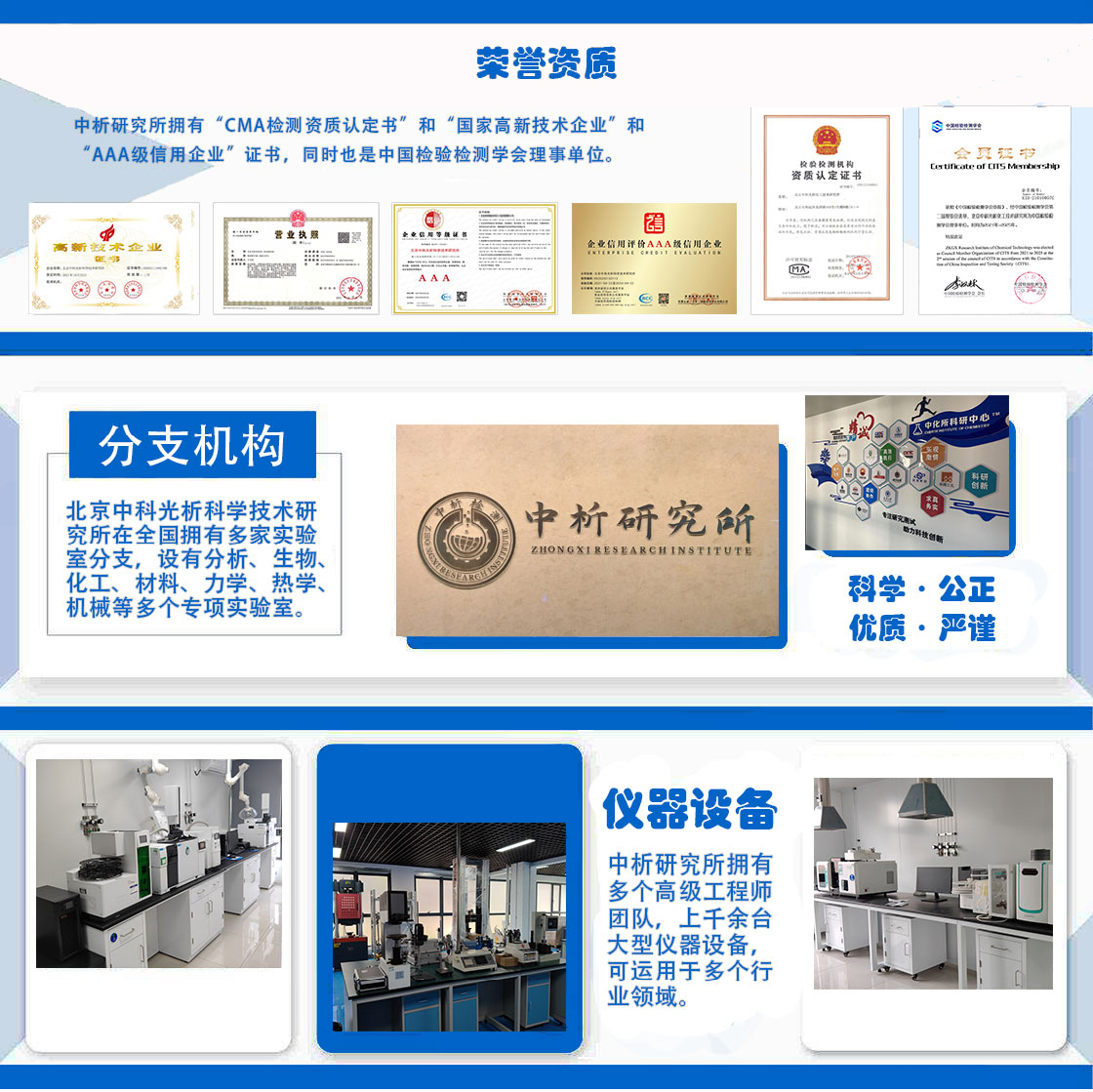
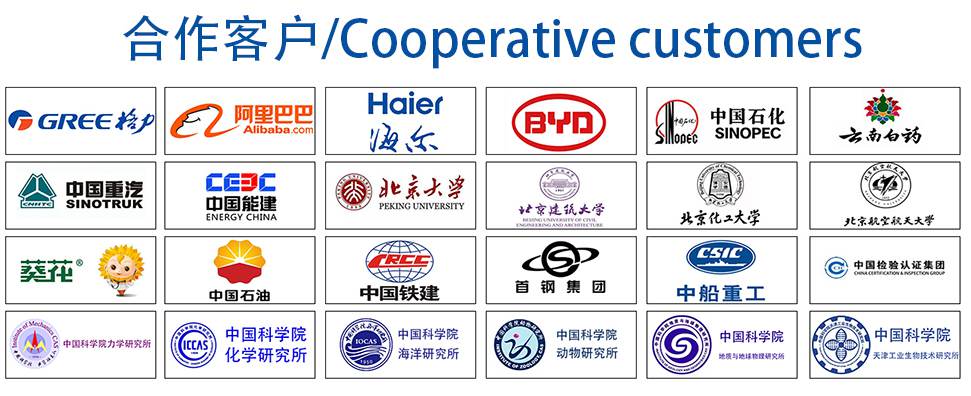
材料实验室
热门检测
11
12
13
13
14
13
14
10
12
11
9
14
11
13
13
18
14
14
17
13
推荐检测
联系电话
400-635-0567